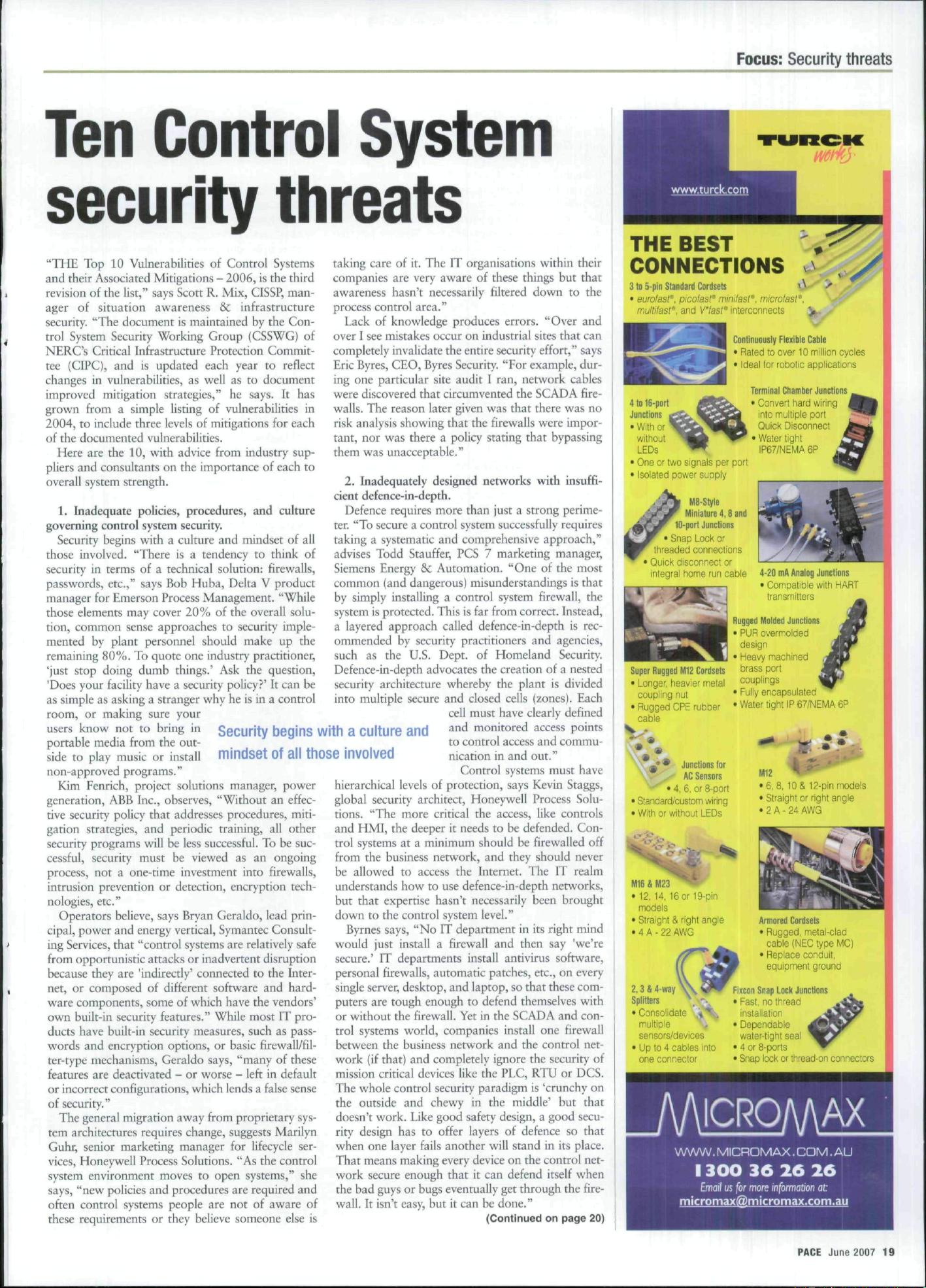
Focus:
Security threats
Ten Control System
security threats
"THE Top 10 Vulnerabilities of Control Systems
and their Associated Mitigations - 2006, is the third
revision of the list," says Scott R. Mix, CISSP, man-
ager of situation awareness & infrastructure
security. "The document is maintained by the Con-
trol System Security Working Group (CSSWC) of
NERC's Critical Infrastructure Protection Commit-
tee (CIPC), and is updated each year to reflect
changes in vulnerabilities, as well as to document
improved mitigation strategies," he says. It has
grown from a simple listing of vulnerabilities in
2004,
to include three levels of mitigations for each
of the documented vulnerabilities.
Here are the 10, with advice from industry sup-
pliers and consultants on the importance of each to
overall system strength.
1.
Inadequate policies, procedures, and culture
governing control system security.
Security begins with a culture and mindset of all
those involved. "There is a tendency to think of
security in terms of a technical solution: firewalls,
passwords, etc.," says Bob Huba, Delta V product
manager for Emerson Process Management. "While
those elements may cover 20% of the overall solu-
tion, common sense approaches to security imple-
mented by plant personnel should make up the
remaining 80%. To quote one industry practitioner,
'just stop doing dumb things.' Ask the question,
'Does your facility have a security policy?' It can be
as simple as asking a stranger why he is in a control
room, or making sure your
users know not to bring in
portable media from the out-
side to play music or install
non-approved programs."
Kim Eenrich, project solutions manager, power
generation, ABB Inc., observes, "Without an effec-
tive security policy that addresses procedures, miti-
gation strategies, and periodic training, all other
security programs will be less successful. To be suc-
cessful, security must be viewed as an ongoing
process, not a one-time investment into firewalls,
intrusion prevention or detection, encryption tech-
nologies, etc."
Operators believe, says Bryan Geraldo, lead prin-
cipal, power and energy vertical, Symantec Consult-
ing Services, that "control systems are relatively safe
from opportunistic attacks or inadvertent disruption
because they are 'indirectly' connected to the Inter-
net, or composed of different software and hard-
ware components, some of which have the vendors''
own built-in security features." While most IT pro-
ducts have built-in security measures, such as pass-
words and encryption options, or basic firewall/fil-
ter-type mechanisms, Geraldo says, "many of these
features are deactivated - or worse - left in default
or incorrect configurations, which lends a false sense
of security."
The general migration away from proprietary sys-
tem architectures requires change, suggests Marilyn
Guhr, senior marketing manager for lifecycle ser-
vices,
Honeywell Process Solutions. "As the control
system environment moves to open systems," she
says,
"new policies and procedures are required and
often control systems people are not of aware of
these requirements or they believe someone else is
Security
begins with a culture and
mindset
of all those involved
taking care of it. The IT organisations within their
companies are very aware of these things but that
awareness hasn't necessarily filtered down to the
process control area."
Lack of knowledge produces errors. "Over and
over
1
see mistakes occur on industrial sites that can
completely invalidate the entire security effort," says
Eric Byres, CEO, Byres Security. "For example, dur-
ing one particular site audit I ran, network cables
were discovered that circumvented the SCADA fire-
walls.
The reason later given was that there was no
risk analysis showing that the firewalls were impor-
tant, nor was there a policy stating that bypassing
them was unacceptable."
2.
Inadequately designed networks with insuffi-
cient defence-in-depth.
Defence requires more than just a strong perime-
ter. "To secure a control system successfully requires
taking a systematic and comprehensive approach,"
advises Todd Stauffer, PCS 7 marketing manager,
Siemens Energy & Automation. "One of the most
common (and dangerous) misunderstandings is that
by simply installing a control system firewall, the
system is protected. This is far from correct. Instead,
a layered approach called defence-in-depth is rec-
ommended by security practitioners and agencies,
such as the U.S. Dept. of Homeland Security.
Defence-in-depth advocates the creation of a nested
security architecture whereby the plant is divided
into multiple secure and closed cells (zones). Each
cell must have clearly defined
and monitored access points
to control access and commu-
nication in and out."
Control systems must have
hierarchical levels of protection, says Kevin Staggs,
global security architect, Honeywell Process Solu-
tions.
"The more critical the access, like controls
and HMI, the deeper it needs to be defended. Con-
trol systems at a minimum should be firewalled off
from the business network, and they should never
be allowed to access the Internet. The IT realm
understands how to use defence-in-depth networks,
but that expertise hasn't necessarily been brought
down to the control system level."
Byrnes says, "No IT department in its right mind
would just install a firewall and then say 'we're
secure.' IT departments install antivirus software,
personal firewalls, automatic patches, etc., on every
single server, desktop, and laptop, so that these com-
puters are tough enough to defend themselves with
or without the firewall. Yet in the SCADA and con-
trol systems world, companies install one firewall
between the business network and the control net-
work (if that) and completely ignore the security of
mission critical devices like the PLC, RTU or DCS.
The whole control security paradigm is 'crunchy on
the outside and chewy in the middle' but that
doesn't work. Like good safety design, a good secu-
rity design has to offer layers of defence so that
when one layer fails another will stand in its place.
That means making every device on the control net-
work secure enough that it can defend itself when
the bad guys or bugs eventually get through the fire-
wall. It isn't easy, but it can be done."
(Continued
on page 20)
THE
BEST
CONNECTIONS
3
to 5-pin
Standard
Cordsets \,
•
eurotasf-, picofasr minifast*. microfast",
multifast'. and Vlasf interconnects
Continuously
Flexible Cable
•
Rated to over 10 million cycles
•
Ideal for robotic appiications
4
to 16-poft
Junctions
•
With or
without
LEDs
•
One or two signals per port
•
Isolated power supply
M8-Style
Miniature
4.8 and
10-part
Junctions
Snap
Lock or
threaded
connections
Quick
disconnect or
integral
home run cable
Terminal
Chamber Junctions
•
Convert hard wiring
into
multiple port
Quick
Disconnect
•
Waler tight
IP67/NEMA
6P
4-20
mA
Analog
Junctions
•
Compatible with HART
transmitters
Super Rugged
M12
Cordsets
•
Longer, heavier metal
coupling
nut
•
Rugged CPE rubber
cable
•
»
N,
^^ Junctions for
AC
Sensors
'
4, 6, or 8-port
>
Standard/custom wiring
'
With or without LEDs
Rugged
Molded Junctions
•
PUR overmolded
design
•
Heavy machined
brass
port
couplings
•
Fully encapsulated
•
Water tight IP 67/NEMA 6P
M12
•6,8,
10 & 12-pin models
•
Straight cr right angle
• 2 A -
24 AWG
|||
M16 & MZ3
•
12, 14, 16 or 19-pin
models
•
Straight & right angle
« 4
A
-
22 AWG
2,3
&
4-wav
Splitters
•
Consolidate
multiple
sensors/devices
•
Up to 4 cables into
one
connector
Armored
Corflsets
•
Rugged,
metal-clad
cable
(NEC type MC)
•
Replace conduit,
equipment
ground
Fixcon Snap
Lock Junctions
•
Fast, no thread
installation
•
Dependable
water-tight
seal
•
4 or 8-ports
•
Snap lock or ihread-on connectors
WWW.MICRDMAX.CQM.AU
I 3OO 36 26 26
Email
us for more
information
at:
micromax@fnicromax.com.au
PACE
June 2007 19