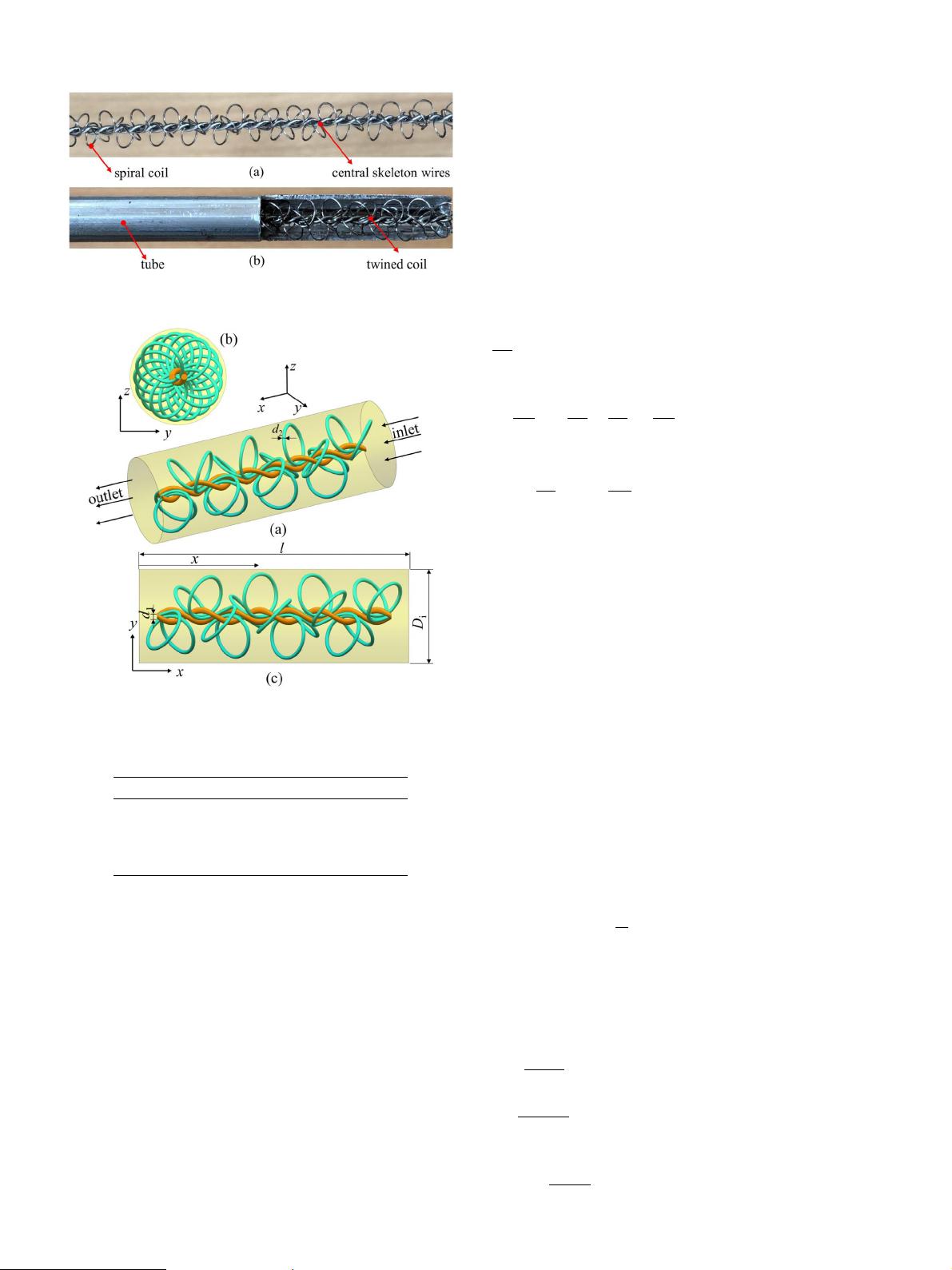
W. Dang and L.-B. Wang International Journal of Heat and Mass Transfer 169 (2021) 120960
Fig. 1. The views of the twined coil insert: (a) the twined coil; (b) the tube with
the twined coil insert.
Fig. 2. Computational model: (a) 3D view of tube with the twined coil insert; (b) y -
z view; (c) x - y view.
Table 1
Parameters of the computational domain.
Geometrical parameters Value
The diameter of central skeleton wires d
1
/ D
i
0.0625
The diameter of spiral coil d
2
/ D
i
(mm) 0.0375
The turns of spiral coil N (-) 17
The diameter of tube D
i
(mm) 8
The length of simulation domain l / D
i
(mm) 2.875
Numerical model
2.1. Physical problem statement
A type of twined coil is formed by rotating two central skele-
ton wires and a spiral coil. The picture of the twined coil insert is
shown in Fig. 1 . The twinned coil is shown in Fig. 1 (a). A tube with
the twinned coil insert is shown in Fig. 1 (b).
The physical model of the tube having the twined coil is shown
in Fig. 2 . The diameter of tube is D
i
= 8 mm, the length of tube is
l = 23 mm, the diameter of the spiral coil is d
2
= 0.3 mm, the diam-
eter of central skeleton wires of the twined coil is d
1
= 0.5 mm, the
detail geometric parameters is shown in Table 1 .
In the present study, 45# transformer oil is employed as the
working fluid, and the thermal properties of the transformer oil is
evaluated at the mean inlet temperature. They are set as ρ= 852
kg/m
3
, c
p
= 1993 J/(kg
•
K), μ= 0.014228 kg/(m
•
s), λ= 0.123 W/(m
•
K),
respectively. The heat transfer and friction characteristics in the
tube with the twined coil insert are numerically investigated at
Reynolds number range of 40 0-180 0. The corresponding fluid in-
let velocity is 0.036-0.161 m/s.
2.2. Mathematics formulation
To build up the mathematical model, the following assumptions
are made: (1) fluid flow is assumed to be incompressible and in a
steady state without considering the viscous dissipation; (2) fluid
(transformer oil) is Newtonian fluid; (3) the gravity effect is negli-
gible. Based on these assumptions, the compact forms of the gov-
erning equations in physical space are as follow:
Continuity equation:
∂ u
i
∂ x
i
= 0
(
i = 1 , 2 , 3
)
(1)
Momentum equation:
ρu
i
∂ u
j
∂ x
i
= −
∂ p
∂ x
j
+
∂
∂ x
i
μ
∂
u
j
∂ x
i
(
j = 1 , 2 , 3
)
(2)
Energy equation:
ρc
p
u
i
∂
∂ x
i
= λ
∂
2
T
∂x
2
i
(3)
Where p is pressure, ρ is fluid density, μ is dynamic viscosity.
On inlet and outlet cross section, the periodic boundary condi-
tion is adopted:
u (x, y, z)
|
in
= u (x, y, z)
|
out
, v (x, y, z)
|
in
= v (x, y, z)
|
out
,
w (x, y, z)
|
in
= w (x, y, z)
|
out
, (x, y, z)
|
in
= (x, y, z)
|
out
(4)
where is the dimensionless temperature and defined as follows:
(x, y, z) =
(
T (x, y, z) − T
bulk
)
/
(
T
w
− T
bulk
)
(5)
where T
bulk
is the average temperature at cross section, and T
w
is
the wall temperature:
T
bulk
=
u (x, y, z) T (x, y, z)d y d z/
u (x, y, z) d y d z (6)
On the tube wall, no-slip condition for velocity and uniform wall
temperature thermal boundary conditions is applied:
u (x, y, z)
|
w
= 0 , v (x, y, z)
|
w
= 0 ,
w (x, y, z)
|
w
= 0 , T (x, y, z)
|
w
= T
w
(7)
On the twined coil surfaces of the computational regions, no-slip
condition for velocity and adiabatic thermal boundary conditions
is applied:
u (x, y, z)
|
w
= 0 , v (x, y, z)
|
w
= 0 ,
w (x, y, z)
|
w
= 0 , −λ
∂T
∂n
|
w
= 0
(8)
The upstream temperature is 313.15K, and the temperature of wall
is 303.15K.
2.3. Parameter definitions
The Reynolds number and friction factor are:
Re =
ρu
in
D
i
μ
(9)
f =
p D
i
0 . 5 ρu
2
in
l
(10)
Local Nusselt number is defined as:
N u
local
=
h
local
D
i
λ
(11)
3