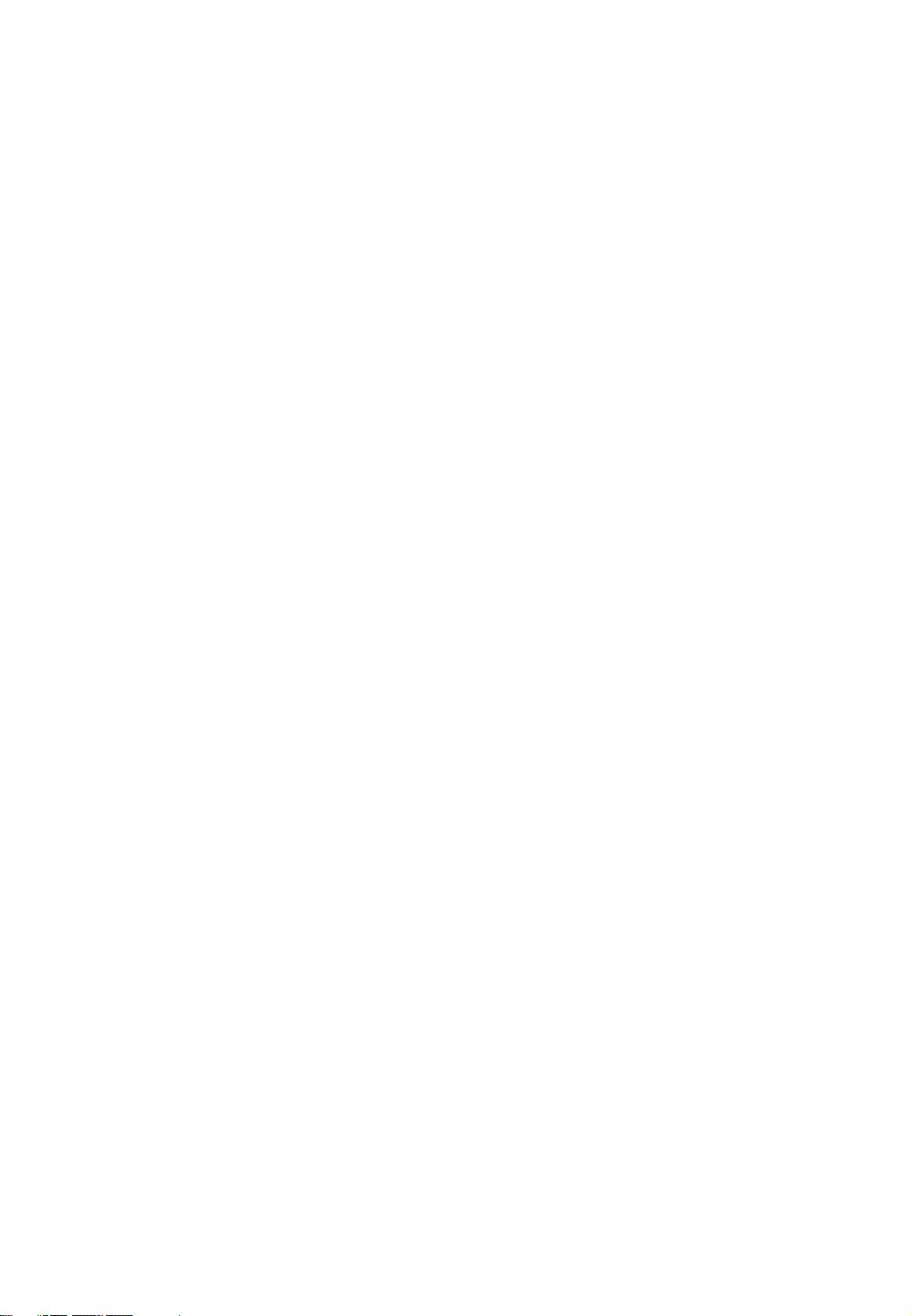
NI 635, Sec 1
8 Bureau Veritas December 2017
Outputs from a Fire and Explosion Risk Analyses (FERA),
Smoke and Gas Dispersion Analysis (SGDA) and recom-
mended practices along with understanding of personnel
distribution are commonly used to develop escape, evacua-
tion and rescue scenarios in order to:
• evaluate the adequacy of the escape, evacuation and
rescue means under identified emergency scenarios (i,e,
effects of thermal radiation, blast and smoke/toxic gas)
• assess the adequacy of the evacuation philosophy in
terms of primary, secondary and tertiary means of evac-
uation and circumstances in which different evacuation
routes take precedence
• assess the integrity and endurance time of temporary
refuges, and
• assess the escape from the individual areas of the instal-
lation (i.e. process area decks, accommodation, hull
and utility rooms).
3.3.5 ESSA - Emergency System Survivability
Analysis
An Emergency Systems Survivability Analysis (ESSA) is car-
ried out to assess the ability of emergency systems to with-
stand accident conditions such as fire, smoke, blast and
hazardous gas releases. It is vital to ensure that these sys-
tems perform their function during Major Accident Events.
3.4 Reliability and integrity
3.4.1 FMECA - Failure Mode, Effects and Criticality
Analysis
A Failure Mode, Effects and Criticality Analysis (FMECA)
study considers each mode of failure for every component
of a system, and determines local effects and end effects on
system operation, on personnel safety and environment pro-
tection. Failure modes are classified in relation to likelihood
of the failure occurring and severity of failure effects. Likeli-
hood in combination with severity will generate a criticality
rating for each failure mode, which is based upon a prede-
termined risk matrix.
Starting from the basic failure characteristics of elements
and functional structure of the system, FMECA systemati-
cally documents the ways equipment can fail, the possible
causes, the effects these failures can produce on system per-
formance and ranks each potential failure according to the
combination of its severity, its probability of occurrence and
the possibility that it can be detected.
These three parameters are qualitatively evaluated referring
to defined levels. Five levels for probability, consequences
and non-detection are defined. The combination of these
three figures (probability, consequences, and non-detection)
provides the criticality score associated to the considered
failure mode.
The FMECA is carried out on a series of worksheets, where
the results are listed in a tabular format, equipment item (or
function) by equipment item (or function), following a sys-
tematic bottom up approach starting from the lowest level
of component failure and rising through the next level of
system hierarchy up to the overall system level.
3.4.2 SIL - Safety Integrity Level allocation and
verification
Assessing the safety, availability and reliability of Safety
Instrumented Systems (SIS).
3.4.3 RAM - Reliability, Availability and Maintainability
Reliability, Availability and Maintainability study (RAM) is a
simulation of the configuration, operation, failure, repair
and maintenance of equipment. It includes the physical
components, equipment configuration and maintenance
philosophy in a system. It generates sufficient data needed
in order to make decisions for possible systems changes that
may increase system efficiency, and therefore increase proj-
ect profits.
RAM modeling can simulate the configuration, operation,
failure, repair and maintenance of equipment. The inputs to
RAM modeling will include the physical components,
equipment configuration and maintenance philosophy in a
system and the outputs can determine average production
of the system over the facility or vessel life. RAM studies
will generate sufficient data on which to base decisions for
possible systems changes that may increase system effi-
ciency, and therefore increase project profits.
3.4.4 RCM - Reliability Centered Maintenance
Reliability Centered Maintenance study (RCM) is a logical,
systematic decision making process for defining optimum
maintenance tasks (part of Asset Integrity Management Sys-
tems, AIMS):
• to focus the preventive maintenance effort on equip-
ment essential to health, safety, environment and/or
operation
• to implement an optimized maintenance plan (what,
when, how), oriented as far as possible on Condition-
Based-Maintenance
• increase inherent reliability and availability of the
unit/system in its operating context Validate the ade-
quacy between the installation design, the operation
and preventive maintenance
• demonstrate a commitment to improve the reliability,
safety and environmental integrity in front of insurers,
charterers, regulatory bodies…
3.5 Risk quantification/reduction
3.5.1 RA - Risk Assessment
Generally, the risk assessment study has the following
objectives:
• evaluation of the design, taking into account the opera-
tional procedures
• determination of limiting conditions of operations (e.g.
loading/offloading)
• assessment of safety and operability through risk assess-
ment techniques (e.g. for transfer system).
Risk assessment methodology may be based on the provi-
sions of EN 1474-3 or other recognized standards, such as
EN ISO 17776 "Guidelines on tools and techniques for haz-
ard identification and risk assessment".