连续铸钢原理探析:二冷区传热与凝固
需积分: 0 157 浏览量
更新于2024-08-22
收藏 27.79MB PPT 举报
"二冷区的传热与凝固-连续铸钢原理"
连续铸钢,简称连铸,是钢铁行业中的一项先进技术,与传统的模铸法相比,它具有显著的优势,如提高金属收得率,节约能源,提升铸坯质量和生产效率。连铸的基本原理是将钢水直接浇注成形,通过连续铸钢机完成整个凝固过程。
1933年,德国的Junghans建造了第一台连铸机,随后在二十世纪五十年代,连铸技术在欧美国家迅速发展,70年代进入快速发展期,80年代逐渐成熟,至今已成为钢铁生产的主流工艺。中国在1957年开始试验研究,1958年在重钢建成双流连铸机,至1964年,重钢的弧形板坯连铸机成为世界上最早的弧形连铸机。
连铸过程中的关键环节之一是二次冷却,即铸坯离开结晶器后直至完全凝固的阶段。这个过程中,二次冷却传热主要有四种方式:冷却水加热与蒸发占据了55%的比例,铸坯辐射占25%,辊子传导占17%,空气对流占3%。这些传热方式共同决定了铸坯的凝固速度和质量。
连铸技术的进步体现在多个方面,包括结晶器自动调宽、流式结晶器液面控制、漏钢预报、中间包等离子加热等。此外,预防性维护、人员培训和教育制度的建立也是确保连铸稳定运行的重要措施。90年代以来,连铸技术进一步发展,诸如近终形连铸、高速浇铸、高清洁性产品连铸、低过热度浇铸、半凝固加工技术以及过程与质量控制系统等新技术不断涌现,推动了连铸技术的不断创新和完善。
在中国,连铸技术的应用极大地提升了钢铁生产的效率和产品质量,降低了生产成本,同时减少了能源消耗。为了提高连铸机的作业率,采用了多炉连烧技术、连铸机设备长寿命技术、防漏钢的稳定化操作技术以及缩短非浇注时间的维护操作技术等,这些技术的实施有力地保障了连铸生产的安全性和稳定性。
连续铸钢原理及其工艺是现代钢铁生产的核心技术,涉及到铸坯的传热与凝固、连铸机的发展历程、技术优势以及提升生产效率的各种策略。随着科技的不断进步,连铸技术将持续优化,为钢铁行业带来更多的创新和效益。
点击了解资源详情
点击了解资源详情
点击了解资源详情
2021-09-16 上传
2022-11-17 上传
2021-06-12 上传
2021-06-05 上传
2021-05-23 上传
2021-05-23 上传
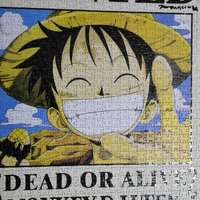
无不散席
- 粉丝: 32
- 资源: 2万+
最新资源
- Raspberry Pi OpenCL驱动程序安装与QEMU仿真指南
- Apache RocketMQ Go客户端:全面支持与消息处理功能
- WStage平台:无线传感器网络阶段数据交互技术
- 基于Java SpringBoot和微信小程序的ssm智能仓储系统开发
- CorrectMe项目:自动更正与建议API的开发与应用
- IdeaBiz请求处理程序JAVA:自动化API调用与令牌管理
- 墨西哥面包店研讨会:介绍关键业绩指标(KPI)与评估标准
- 2014年Android音乐播放器源码学习分享
- CleverRecyclerView扩展库:滑动效果与特性增强
- 利用Python和SURF特征识别斑点猫图像
- Wurpr开源PHP MySQL包装器:安全易用且高效
- Scratch少儿编程:Kanon妹系闹钟音效素材包
- 食品分享社交应用的开发教程与功能介绍
- Cookies by lfj.io: 浏览数据智能管理与同步工具
- 掌握SSH框架与SpringMVC Hibernate集成教程
- C语言实现FFT算法及互相关性能优化指南