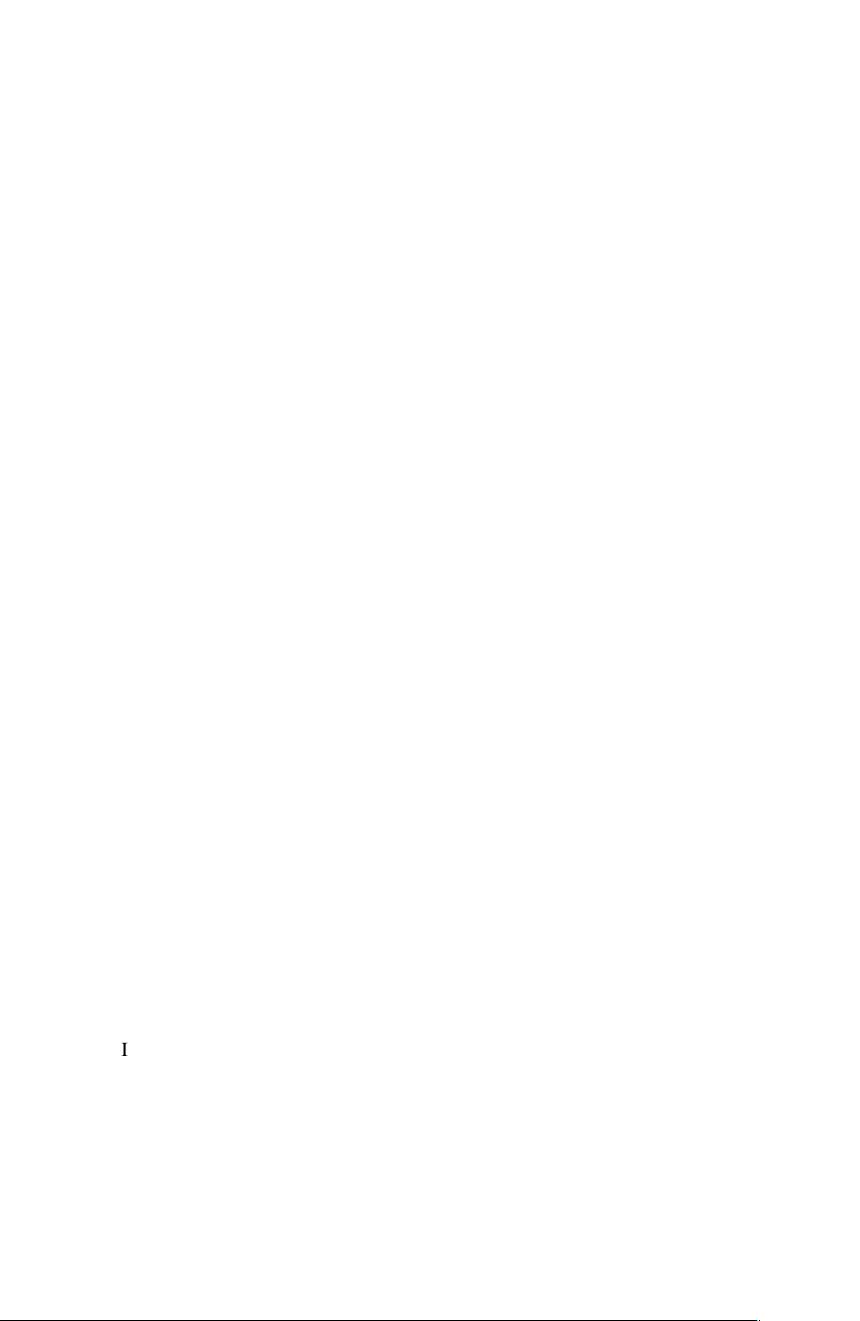
2 W. van Sark, L. Korte, and F. Roca
However the challenge of developing photovoltaic technology to a cost-
competitive alternative for established fossil-fuel based energy sources remains
enormous and new cell concepts based on thin films of various types of organic
and inorganic materials are entering the market. Thin film silicon (TFS), cadmium
telluride (CdTe), copper indium selenide (CIS) generally are denoted as the
second generation of PV technologies and are currently considered a very interest-
ing market alternative to crystalline silicon. Advanced thin film approaches such
as dye-sensitized titanium oxide (TiO
2
) and blends of polythiophene and C
60
(P3HT:PCBM) [8] are showing fast progress. World-record solar cell efficiencies
are regularly updated, see e.g. [9], and some interesting initiatives related to their
industrialization and commercialization have recently been undertaken.
For large scale PV deployment in large power plants or in building integrated
applications it is a prerequisite that the performance of solar energy systems is en-
hanced by assuring low cost in production and long term reliability (>25 years).
This requires the following issues to be addressed: 1) increase of the efficiency of
solar irradiation conversion; 2) decrease of the amount of materials that are used,
while these materials should be durable, stable, and abundant on earth; and 3)
reduction of the manufacturing and installation cost.
The fantastic boom of thin film technology in recent years can suggest further
development on the medium to long term due to the application of innovative con-
cepts to conventional materials and developments of new classes of thin film
materials stemming from nanotechnologies, photonics, optical metamaterials,
plasmonics and new semiconducting organic and inorganic sciences, most of them
recognized as next (third) generation approaches.
On the other hand the growth of the PV industry is also requesting well proven
technology in order to sustain the emerging market; here, crystalline silicon has a
long history of ‘pulling rabbits out of the hat’ [5].
Today, the industry has reached a new level of scale that is mobilizing vast new
resources, enthusiasm, skills, and energy in order to reduce wafer thickness, en-
hance efficiency and improve processes related to substrate cleaning, junction re-
alization, surface passivation, contact realization. We see that PV’s historic price
reduction is a result from the combined effects of step-by-step evolutionary im-
provements in a wide variety of areas rather than one or two huge breakthroughs
[5,6]. For example, processes such as dry texturing, spray-on phosphorus doping
sources or impurity gettering have become standard, while last but not least ac-
tions related to increase the factory size and automation further lead to cost reduc-
tions (“economies of scale”).
In contrast, larger values of the conversion efficiency of PV technology have
been reached with the realization of sophisticated crystalline silicon (c-Si) cell
structures, involving numerous and very complicated steps. This approach inevita-
bly implies an increase of costs, which is not compatible with industrial production
requirements that demand simple, high-throughput and reproducible processes.
In order to realize reliable devices characterized by high efficiency and low
cost, an approach has been developed on the basis of amorphous/crystalline silicon
heterojunction solar cells (SHJ), which combines wafer and thin film technologies.
In this area impressive results were achieved by Sanyo Electric with the so called
a-Si/c-Si Heterojunction with Intrinsic Thin layer (HIT) solar cell [10,11]. This
technology showed excellent surface passivation (open circuit voltage (V
oc
) values