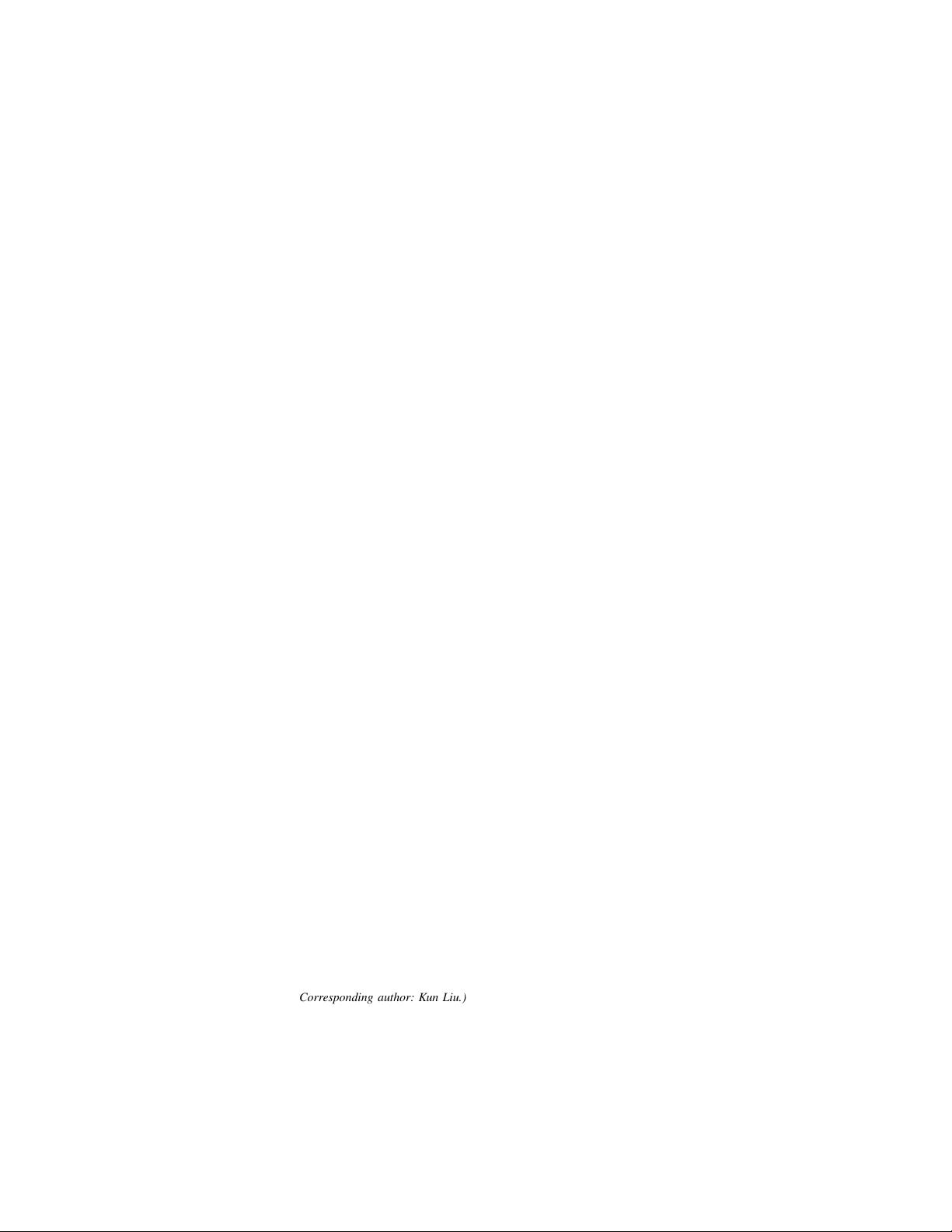
IEEE PHOTONICS TECHNOLOGY LETTERS, VOL. 27, NO. 19, OCTOBER 1, 2015 2055
Distributed Optical Fiber Current Sensor Based
on Magnetostriction in OFDR
Zhenyang Ding, Yang Du, Tiegen Liu, Kun Liu, Bowen Feng, and Junfeng Jiang
Abstract—We present a distributed optical fiber current
sensor based on magnetostriction using Rayleigh backscatter-
ing spectra (RBS) spectral shift in optical frequency-domain
reflectometry. In the proposed sensor, the magnetostrictive
Fe–Co–V alloy thin films as sensing materials are attached
to a 63-m standard single-mode fiber (SMF). We detect the
strain variation coupled to the SMF caused by the magnetic
field variation by measuring the RBS shift. As the magnetic
field variation is proportional to the current variation in the
electric line, the current can be measured. In our experiment,
we measure the current range from 0 to 11.8 A and 0 to 12.14 A
at two locations using proposed method and obtain distributed
current trace. We achieve the linear relationship between the
RBS shift and the current variation. The minimal measurable
current variation is 0.3 A when the sensing spatial resolution
is 14 cm.
Index Terms—Current, optical fibers, Rayleigh scattering,
frequency domain analysis, reflectometry.
I. INTRODUCTION
F
IBER optic current sensors have attracted a lot of interest
for researchers these years, thanks to their many
advantages such as immunity to electromagnetic interference,
lightweight, small size, high sensitivity, wide bandwidth,
compactness and ease in signal light transmission, fiber optic
current sensors are suitable to the applications for power
system or industrial control area when compared with the
traditional current sensors [1]–[4]. According to this mech-
anism, the fiber optic current sensors may be divided into
several categories. The first widely used method is based on
Faraday effect [5]–[7], as silica fibers have a very small Verdet
constant, a very long fiber is often needed to improve the
sensitivity. However, how to reduce the birefringence in the
Manuscript received May 14, 2015; revised June 22, 2015; accepted
June 24, 2015. Date of publication July 6, 2015; date of current version
August 31, 2015. This work was supported in part by the National Basic
Research Program of China (973 Program) under Grant 2010CB327806
and Grant 2010CB327802, in part by the Shenzhen Science and Tech-
nology Research Project under Grant JCYJ20120831153904083, in part
by the Science and Technology Key Project through the Ministry of
Education, China, under Grant 313038, in part by the Tianjin Natural
Science Foundation under Grant 13JCYBJC16200, in part by the National
Instrumentation Program under Grant 2013YQ030915, and in part by the
National Natural Science Foundation of China under Grant 61475114,
Grant 61108070, Grant 61227011, and Grant 61378043. (Zhenyang Ding and
Yang Du contributed equally to this work.) (Corresponding author: Kun Liu.)
The authors are with the College of Precision Instrument and
Opto-electronics Engineering, Tianjin University, Tianjin 300072, China,
and also with the Key Laboratory of Opto-Electronics Information Technical,
Ministry of Education, Tianjin University, Tianjin 300072, China (e-mail:
zyding@tju.edu.cn; yangdu@tju.edu.cn; tgliu@tju.edu.cn; beiyangkl@
tju.edu.cn; 1244459356@qq.com; jiangjfjxu@tju.edu.cn).
Color versions of one or more of the figures in this letter are available
online at http://ieeexplore.ieee.org.
Digital Object Identifier 10.1109/LPT.2015.2450237
long fiber length caused by temperature and stress will be a
challenge in this method [8].
The second method is based on thermal effect, this method
needs a short fiber length but requires complex manufacturing
techniques to coat the fibers with metals [9]. The third type is
using magnetic force to stretch the fiber Bragg grating [10].
The fourth type is based on magneto-optical materials. For
example, Li et al. [11] propose a point current sensor based
on magnetic fluid with a single-mode–multimode–single-mode
structure. Another more common used material is magne-
tostriction material, in this method, fiber Bragg grating is
coated with or bonded to magnetostriction material that utilize
the current induced magnetostrictive effect [2], [12].
Almost all these techniques mentioned above are point
current sensors, so they lack the unique ability of optical
fiber sensors of performing distributed measurements.
Palmieri et al. [13] present polarization sensitive OFDR to
achieve distributed current sensing using 130 m long fibers
helically wounded around wires. However, in this method,
as the nature of the Faraday effect is very weak [14], the
sensitivity is only about 0.1 kA and the spatial resolution is
only 10 m.
The spectral shift of Rayleigh backscattering spectra (RBS)
can be used to achieve distributed strain measurements
with high sensitivity and high spatial resolution based
on OFDR [15], [16]. Rayleigh backscattering is caused by
random refractive index fluctuations along an optical fiber,
and it can be modeled as a long, weak FBG with random
periods. The strain change will cause a local RBS spectral
shift, which can be calculated by the cross-correlation between
the measured RBS and a reference RBS [15], [16]. We have
combined the technologies of magnetostriction and distributed
stain sensing by RBS spectral shift in OFDR to develop a
distributed magnetic field sensor [17]. As this method has
high sensitivity and high spatial resolution, it is attractive for
distributed current sensing.
In this letter, we present a distributed optical fiber current
sensor based on magnetostriction using RBS shift in OFDR.
In the proposed sensor, the magnetostrictive Fe-Co-V alloy
thin films as sensing materials are attached to a 63 m standard
single mode fiber (SMF). Magnetic field generated by a
DC current can cause the variation of strain on the magne-
tostrictive thin films. By dectecting the strain variation coupled
to SMF by measuring RBS spectral shift in OFDR, we can
measure the current variation in the electric line. In our
experiment, we measure the range of the current variation are
from 0 A to 11.8A and 0 A to 12.14 A at the location 56 m
and 56.9 m respectively using proposed method and obtain the
1041-1135 © 2015 IEEE. Personal use is permitted, but republication/redistribution requires IEEE permission.
See http://www.ieee.org/publications_standards/publications/rights/index.html for more information.