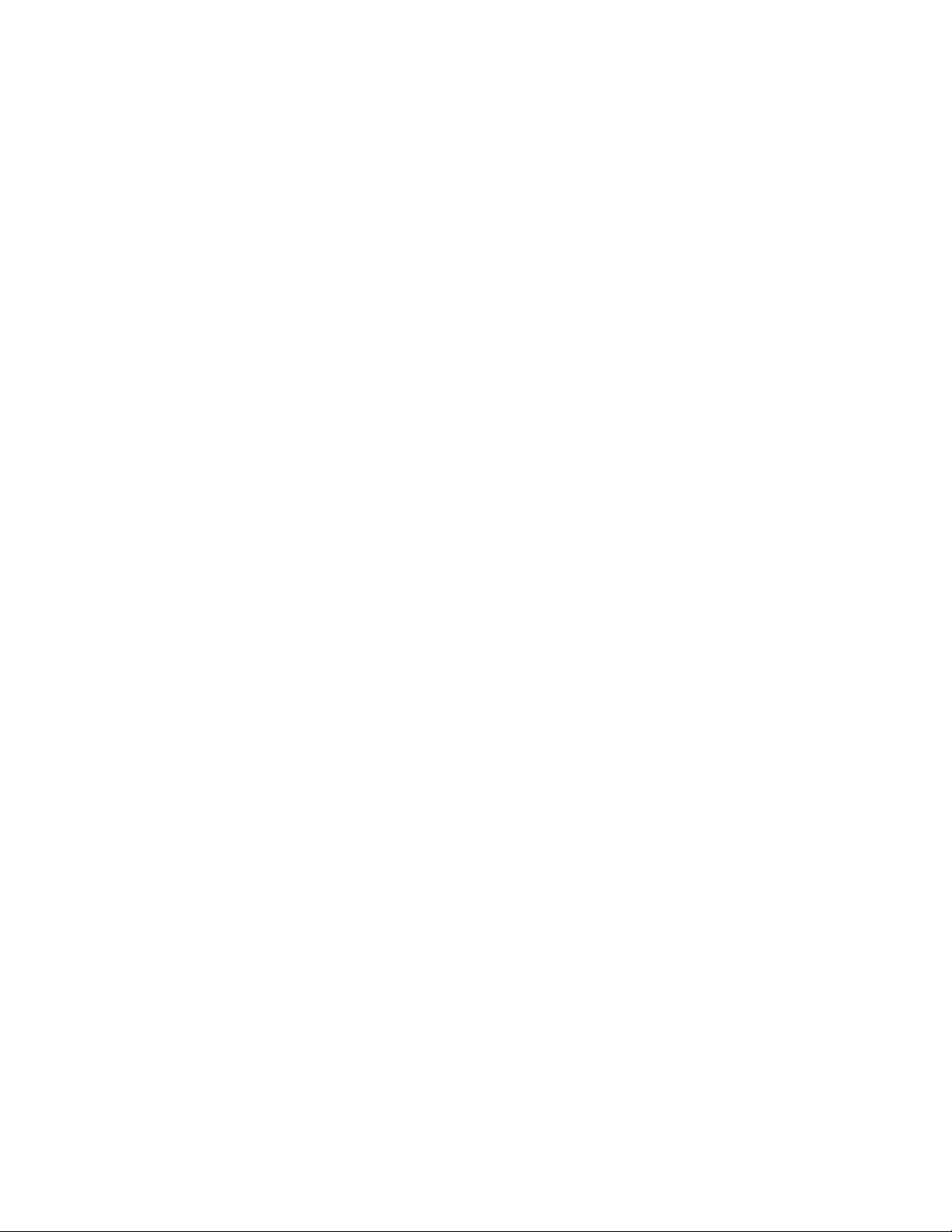
systems and robot learning algorithms to fine-tune parameters, and then the second shift is put
into operation, doubling plant output in four days. Then, a change by a key supplier requires that
the assembly sequence be modified to accommodate a new tolerance in the battery pack assembly.
Engineers use computational tools to quickly modify the assembly sequence: then they print new
instructions for workers and upload modified assembly programs to the assistant robots.
Vignette 2: One-of-a-kind, discrete-part manufacture and assembly
A small job shop with 5 employees primarily catering to orders from medical devices companies is
approached by an occupational therapist one morning to create a customized head-controlled input
device for a quadriplegic wheelchair user. Today the production of such one-of-a-kind devices
would be prohibitively expensive because of the time and labor required for setting up machines
and for assembly. The job shop owner reprograms a robot using voice commands and gestures,
teaching the robot when it gets stuck. The robot is able to get the stock to mills and lathes, and runs
the machines. While the machines are running, the robot sets up the necessary mechanical and
electronic components asking for assistance when there is ambiguity in the instruction set. While
moving from station to station, the robot is able to clean up a coolant spill and alert a human to
safety concerns with a work cell. The robot responds to a request for a quick errand for the shop
foreman in between jobs, but is able to say no to another request that would have resulted in a
delay in its primary job. The robot assembles the components and the joystick is ready for pick-up
by early afternoon. This happens with minimal interruption to the job shop’s schedule.
Vignette 3: Rapid, integrated, model-based design of the supply chain
The packaging for infant formula from a major supplier from a foreign country is found to
suffer from serious quality control problems. The US-based lead engineer is able to use
a comprehensive multi-scale, discrete and continuous model of the entire supply chain,
introduce new vendors and suppliers, repurpose parts of the supply chain and effect a complete
transformation of the chain of events: production, distribution, case packing, supply and
distribution. An important aspect of the transformation is the introduction of 20 robots to rapidly
manufacture the redesigned package
These vignettes may seem far-fetched today, but we have the technology base, the collective expertise,
and the educational infrastructure to develop the broad capabilities to realize this vision in 15 years with
appropriate investments in the critical technology areas.
3.3. Critical Capabilities for Manufacturing
In this section, we briefly discuss the critical capabilities and give examples of possible 5, 10, and 15
year milestones. After this, in Section 4 we describe some promising research directions that could
enable us to meet these milestones.
3.3.1. Adaptable and Recongurable Assembly
Today the time lag between the conceptual design of a new product and production on an assembly line
in the U.S. is unacceptably high. For a new car, this lead-time can be as high as twenty four months.
Given a new product and a set of assembly line subsystems that can be used to make the product, we
want to achieve the ability to adapt the subsystems, reconfigure them and set up workcells to produce
the product. Accordingly the roadmap for adaptable and reconfigurable assembly includes the
following goals over the next fifteen years.
Chapter 1 – Robotics and Automation Research Priorities for U.S. Manufacturing 13