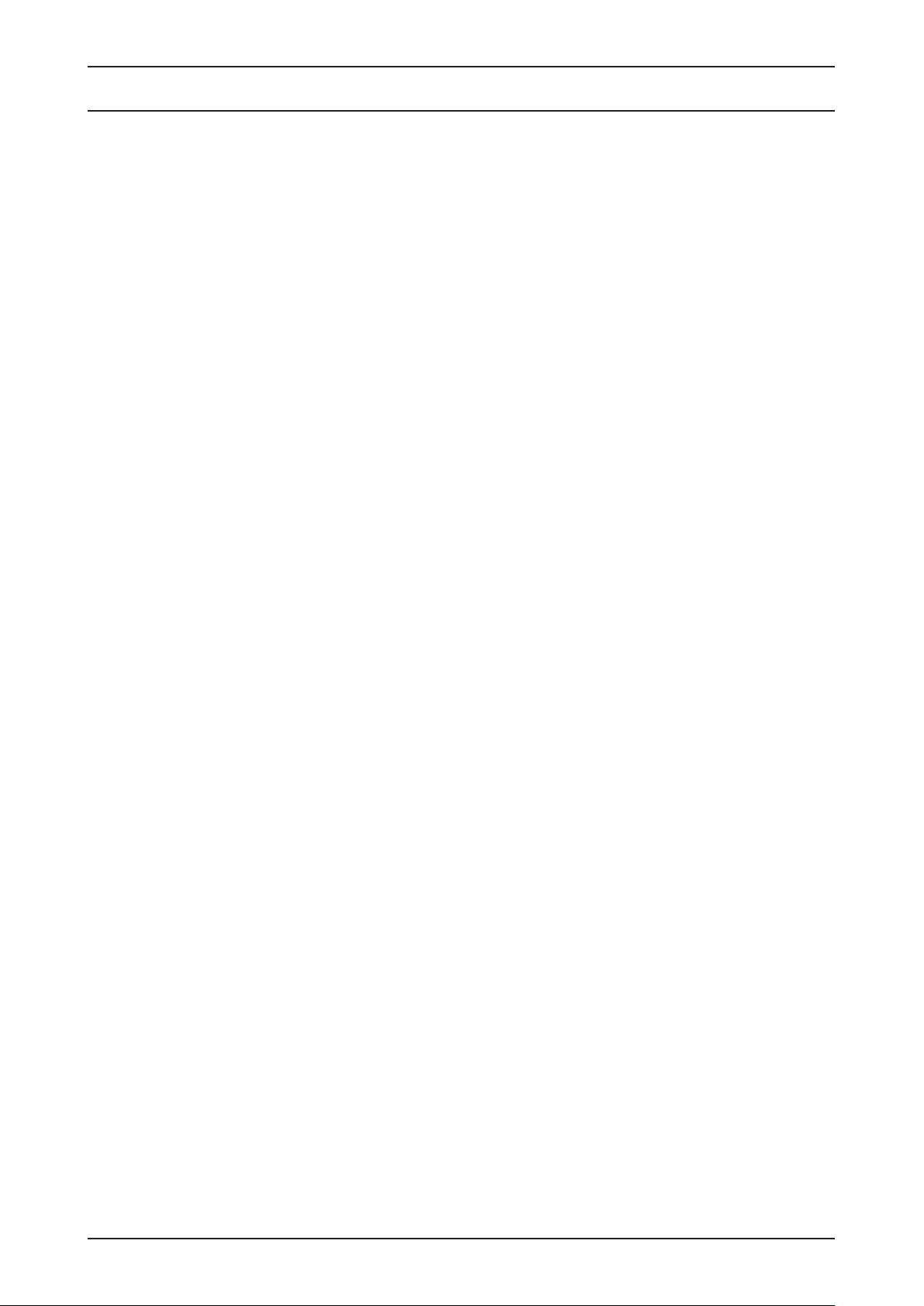
12
Introduction
also have to increase efficiency by reducing their
operating costs, minimize the utilization of natural
resources and improve the safety of their products
and that of their workers.
This White Paper describes how factories of the
future will use a system of systems (SoS) approach
in which the product to be manufactured will
have available all of the data necessary for
its manufacturing requirements. The resulting
self-organization of networked manufacturing
equipment will take into account the entire value
added chain, with the manufacturing sequence
being determined on a flexible basis, depending
on the current situation, and with the human
being remaining essential as the creative planner,
supervisor and decision maker of the process.
The global smart factory market is expected to
total nearly USD 67 billion by 2020, increasing
at a compound annual growth rate of 6% from
2014 to 2020 [1]. Communication, automation,
robotics and virtual simulation will change the
product sector as we know it today. What will the
production world of the future look like? How will
humans and machines communicate with each
other, and what role will our thoughts play?
The developed world is confronted with economic
and monetary constraints that make it harder to
maintain the production levels of recent years,
while developing countries are recording a
rapid increase in output. The result is that for
those industrialized countries looking to remain
competitive, one element, often neglected in the
past but now an integral part of any bill of materials
(BOM) calculation, is the cost of the energy used
to produce the goods. In manufacturing, energy
has always been viewed as a cost of doing
business, an expense to be controlled and a large
contributor to indirect costs. For example, many
production lines continue to operate during holiday
breaks and weekends, even in the absence of any
workers. Since the industrial sector – which uses
roughly 30% to 40% of total world energy – is
highly sensitive to changing economic conditions, it
follows that cost reduction measures introduced as
the result of regulatory and consumer pressures are
pushing companies to use energy more efficiently.
Enhanced compatibility levels can only be
achieved through the existence of consistent
international standards ensuring that components
from different suppliers and technologies can
interact seamlessly. Continued development of
common standards will ensure that data can flow
between automation systems without requiring
an expensive conversion or interpretation of the
meaning of the data if the logic is not commonly
understood. IEC International Standards enable
common terminologies and procedures to ensure
that organizations and businesses can efficiently
communicate and collaborate.
There are many initiatives underway, such as smart
manufacturing, Industrie 4.0, e-Factory or Intelligent
Manufacturing; however this White Paper is not
about a specific programme but about a future
(global) manufacturing in the long term.
This White Paper is the seventh in a series whose
purpose is to ensure that the IEC can continue
to address global problems in electrotechnology
through its International Standards and
Conformity Assessment services. The White
Papers are developed by the IEC Market Strategy
Board (MSB), responsible for analyzing and
understanding the IEC’s stakeholder environment,
in order to prepare the IEC to strategically face the
future.
The main objectives of this White Paper are:
§ To assess potential worldwide needs and
benefits for the factory of the future
§ To identify the concepts and trends in related
technologies and markets including value
chains
§ To review and assess the driving technologies
and their impact
§ To predict the future landscape of manufactur-
ing, taking into account the sometimes con-