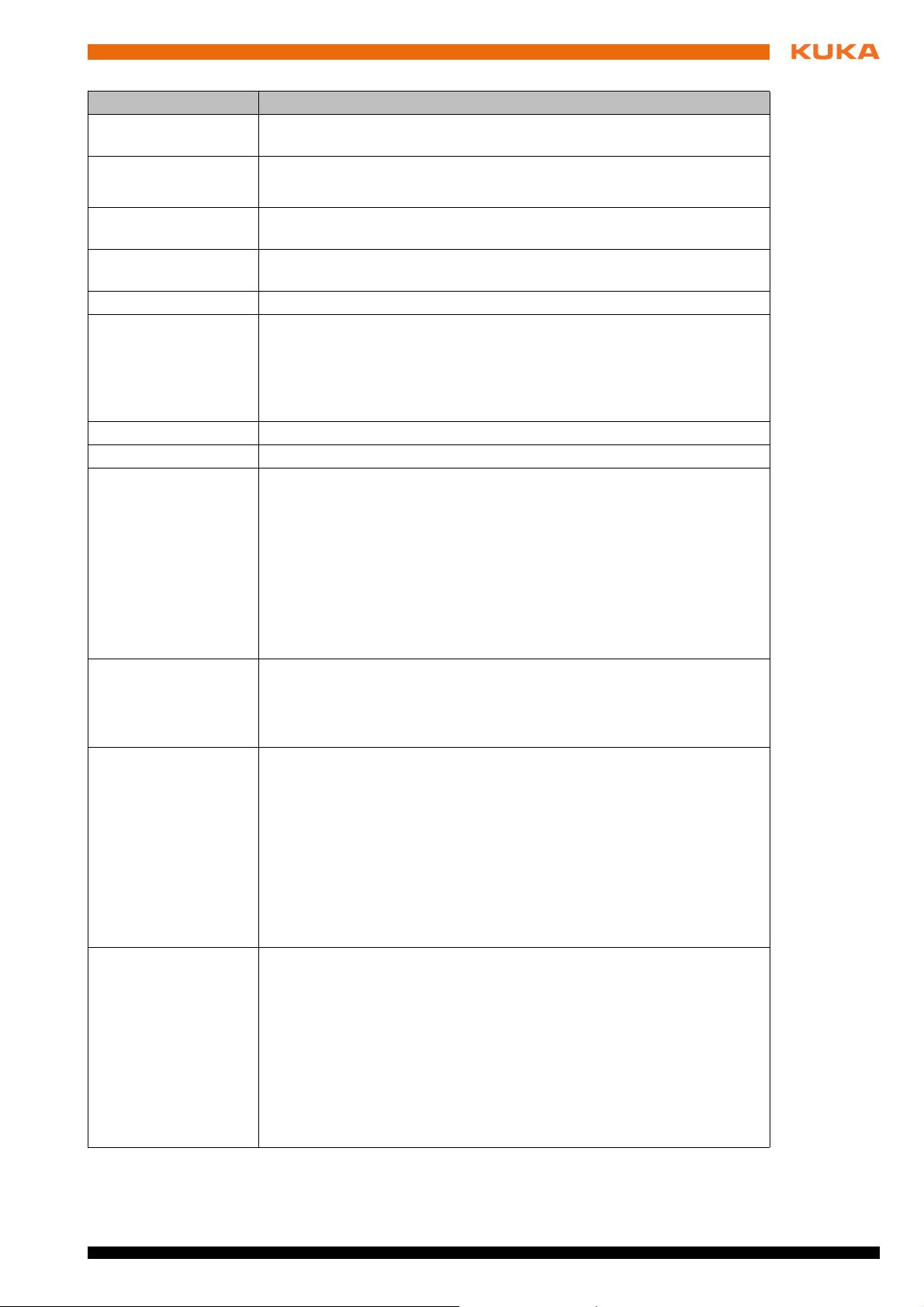
19 / 391Issued: 02.11.2011 Version: KSS 8.2 SI V3 en
3 Safety
Term Description
Axis range Range of each axis, in degrees or millimeters, within which it may move.
The axis range must be defined for each axis.
Stopping distance Stopping distance = reaction distance + braking distance
The stopping distance is part of the danger zone.
Workspace The manipulator is allowed to move within its workspace. The work-
space is derived from the individual axis ranges.
Operator
(User)
The user of the industrial robot can be the management, employer or
delegated person responsible for use of the industrial robot.
Danger zone The danger zone consists of the workspace and the stopping distances.
KCP The KCP (KUKA Control Panel) teach pendant has all the operator con-
trol and display functions required for operating and programming the
industrial robot.
The KCP variant for the KR C4 is called KUKA smartPAD. The general
term “KCP”, however, is generally used in this documentation.
Manipulator The robot arm and the associated electrical installations
Safety zone The safety zone is situated outside the danger zone.
Safe operational stop The safe operational stop is a standstill monitoring function. It does not
stop the robot motion, but monitors whether the robot axes are station-
ary. If these are moved during the safe operational stop, a safety stop
STOP 0 is triggered.
The safe operational stop can also be triggered externally.
When a safe operational stop is triggered, the robot controller sets an
output to the field bus. The output is set even if not all the axes were sta-
tionary at the time of triggering, thereby causing a safety stop STOP 0 to
be triggered.
Safety STOP 0 A stop that is triggered and executed by the safety controller. The safety
controller immediately switches off the drives and the power supply to
the brakes.
Note: This stop is called safety STOP 0 in this document.
Safety STOP 1 A stop that is triggered and monitored by the safety controller. The brak-
ing process is performed by the non-safety-oriented part of the robot
controller and monitored by the safety controller. As soon as the manip-
ulator is at a standstill, the safety controller switches off the drives and
the power supply to the brakes.
When a safety STOP 1 is triggered, the robot controller sets an output to
the field bus.
The safety STOP 1 can also be triggered externally.
Note: This stop is called safety STOP 1 in this document.
Safety STOP 2 A stop that is triggered and monitored by the safety controller. The brak-
ing process is performed by the non-safety-oriented part of the robot
controller and monitored by the safety controller. The drives remain acti-
vated and the brakes released. As soon as the manipulator is at a stand-
still, a safe operational stop is triggered.
When a safety STOP 2 is triggered, the robot controller sets an output to
the field bus.
The safety STOP 2 can also be triggered externally.
Note: This stop is called safety STOP 2 in this document.