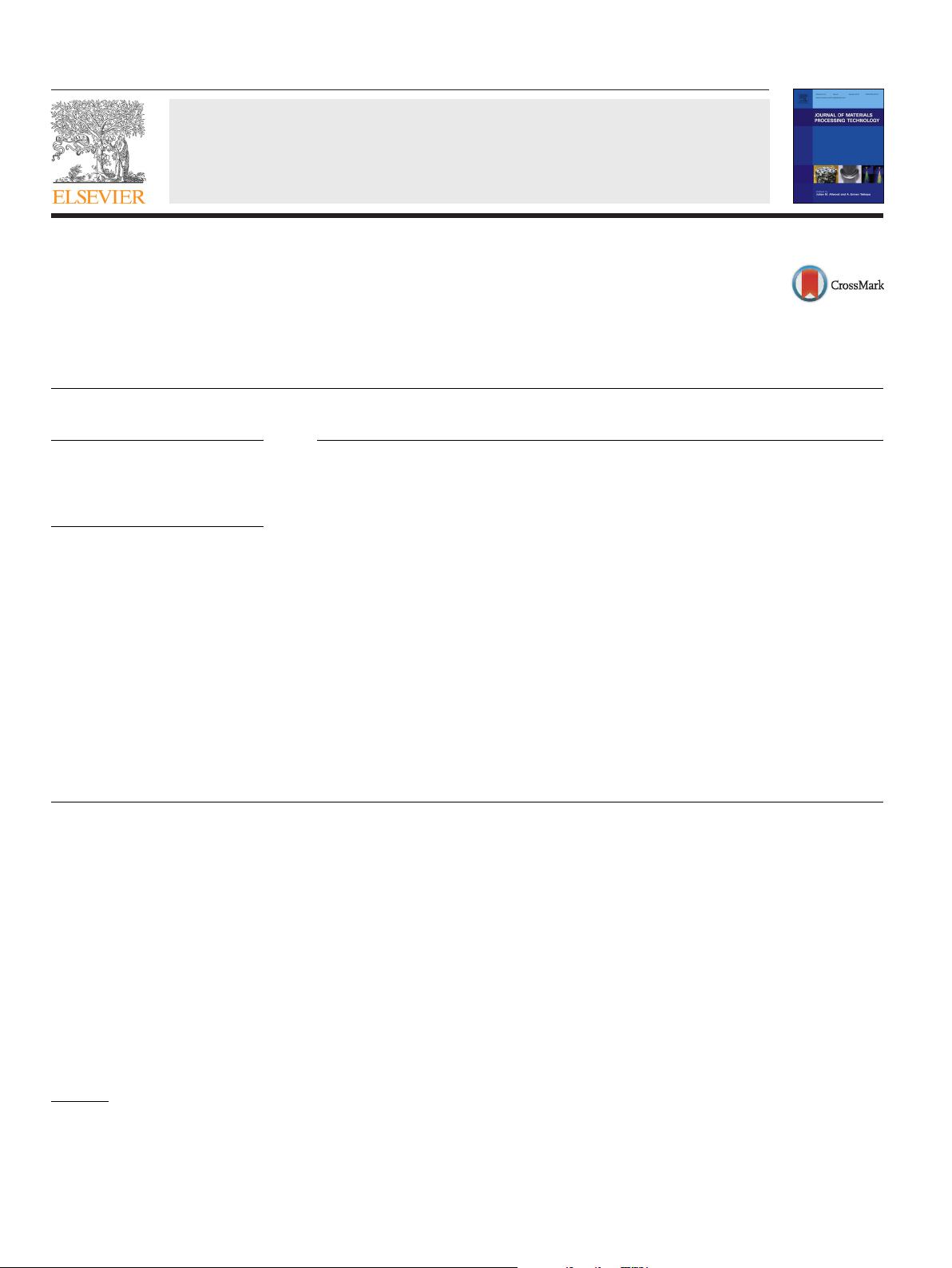
Journal
of
Materials
Processing
Technology
232
(2016)
34–42
Contents
lists
available
at
ScienceDirect
Journal
of
Materials
Processing
Technology
jo
ur
nal
home
p
ag
e:
www.elsevier.com/locate/jmatprotec
Nanosecond
laser
processing
of
Zr
41.2
Ti
13.8
Cu
12.5
Ni
10
Be
22.5
with
single
pulses
E.
Williams,
E.B.
Brousseau
∗
Cardiff
School
of
Engineering,
Cardiff
University,
Cardiff
CF24
3AA,
UK
a
r
t
i
c
l
e
i
n
f
o
Article
history:
Received
10
July
2015
Received
in
revised
form
13
January
2016
Accepted
22
January
2016
Available
online
25
January
2016
Keywords:
Nanosecond
laser
machining
Zr-based
bulk
metallic
glass
Vitreloy
1
Single
pulse
processing
a
b
s
t
r
a
c
t
In
addition
to
their
attractive
mechanical
properties,
the
amorphous
structure
of
bulk
metallic
glasses
(BMGs)
leads
to
favourable
conditions
for
their
processing
using
micro
machining
operations.
At
the
same
time,
the
generally
high
hardness
and
strength
of
such
amorphous
metals
make
short
or
ultra-
short
pulsed
laser
ablation
a
fabrication
technology
of
interest
for
generating
micro
scale
features
on
BMG
workpieces
in
comparison
with
mechanical
material
removal
means.
In
spite
of
this,
relatively
little
research
has
been
reported
on
the
prediction
and
observation
of
the
thermal
phenomena
that
take
place
when
processing
BMGs
with
pulsed
laser
irradiation
for
a
range
of
delivered
fluence
values
and
pulse
lengths.
Such
investigations
are
important
however
as
they
underpin
reliable
laser
processing
opera-
tions,
which
in
turn
lead
to
more
predicable
material
removal
at
micro
scale.
In
this
context,
this
paper
reports
complementary
theoretical
and
experimental
single
pulse
laser
irradiation
analyses
conducted
in
the
nanosecond
(ns)
regime
for
possibly
the
most
prominent
BMG
material
due
to
its
relatively
high
glass
forming
ability,
namely
Zr
41.2
Ti
13.8
Cu
12.5
Ni
10
Be
22.5
,
which
is
also
known
as
Vitreloy
1.
To
achieve
this,
different
pulse
lengths
comprised
between
15
ns
and
140
ns
and
varied
fluence
values
were
con-
sidered
when
delivering
single
pulses
on
a
Vitreloy
1
substrate
using
a
Yb
fibre
laser
system.
A
simple
thermal
model
of
the
laser
material
interaction
process
for
single
pulses
was
also
developed
to
support
the
observations
and
interpretations
of
the
experimental
data
obtained.
One
of
the
main
conclusions
from
this
research,
with
respect
to
potential
micro
machining
applications,
is
that
shorter
pulses,
i.e.
25
ns
and
less,
could
lead
to
the
formation
of
relatively
clean
craters.
For
higher
pulse
lengths,
the
low
thermal
conductivity
and
melt
temperature
of
this
BMG
substrate
mean
that
laser
irradiation
easily
leads
to
the
formation
of
a
relatively
large
melt
pool
and
thus
to
the
re-solidification
of
material
ejected
outside
craters.
©
2016
The
Authors.
Published
by
Elsevier
B.V.
This
is
an
open
access
article
under
the
CC
BY
license
(
http://creativecommons.org/licenses/by/4.0/
).
1.
Introduction
Metallic
alloys
have
an
internal
structure
that
is
crystalline
in
nature.
Glass,
on
the
other
hand,
does
not
possess
a
structure
with
the
long
range
atomic
order
found
in
such
alloys.
Metallic
glasses
display
a
morphology
from
both
of
these
types
of
materials,
having
metal
elements
and
bonds,
whilst
possessing
an
amorphous
inter-
nal
structure.
This
mixture
in
contents
for
metallic
glasses
results
in
electrical
and
thermal
characteristics,
which
are
common
to
metals
while
it
also
leads
to
superior
mechanical
and
chemical
properties
compared
to
their
crystalline
counterparts,
such
as
an
enhanced
tensile
strength
and
elastic
limit
as
well
as
better
corrosion
resis-
tance.
∗
Corresponding
author.
E-mail
address:
BrousseauE@cf.ac.uk
(E.B.
Brousseau).
The
first
reported
metallic
glass
alloy
was
produced
at
California
Institute
of
Technology
in
1960
(Klement
et
al.,
1960)
with
fur-
ther
glassy
metals
formed
by
Chen
and
co-workers
in
the
1970’s
(
Chen
and
Turnbull,
1969).
The
formation
of
bulk
metallic
glasses
(BMGs)
takes
advantage
of
the
difference
in
atomic
sizing
of
all
the
elements
present
in
the
alloy
system,
which
results
in
“con-
fusion”
upon
cooling.
This
means
that
during
the
process
used
to
cool
down
the
liquid
phase
of
the
alloy,
the
different
atoms
do
not
organise
themselves
into
an
ordered
structure
in
sufficient
time
before
they
become
“frozen”
in
place.
However,
to
avoid
crystalli-
sation
when
synthesising
a
metallic
glass
from
its
liquid
state,
it
is
essential
that
the
cooling
rate
applied
is
higher
than
the
critical
cooling
rate
of
the
particular
alloy
system
processed.
As
a
result,
early
fabrication
attempts
of
amorphous
metals
were
limited
to
the
formation
of
samples
with
thin
dimensions
as
such
specimens
enabled
the
required
fast
heat
dissipation
rate.
In
the
1990’s,
the
synthesis
of
metallic
glasses
further
improved
through
the
ability
http://dx.doi.org/10.1016/j.jmatprotec.2016.01.023
0924-0136/©
2016
The
Authors.
Published
by
Elsevier
B.V.
This
is
an
open
access
article
under
the
CC
BY
license
(http://creativecommons.org/licenses/by/4.0/).