掌握Cp、Cpk与Pp、Ppk:过程控制与品质提升的关键
需积分: 10 118 浏览量
更新于2024-08-24
收藏 8.13MB PPT 举报
统计过程控制(SPC)是一种通过统计技术来监控和改进制造业过程的方法,其核心在于理解和管理过程能力。Cp、Cpk、Pp和Ppk是SPC中的四个关键指标,它们衡量了过程的稳定性与一致性。
Cp(过程能力指数)代表了过程在规格范围内完成任务的能力,它考虑了规格宽度,即上下规格限之间的距离。Cp值越高,表示过程能够满足规格要求的程度越好。然而,Cpk(过程能力与规格中心的差距)更进一步,它不仅关注规格内,还关注规格边缘的表现,衡量了过程实际输出值落在规格中心两侧的能力,反映了“我们真正能做得多好”。
Pp(过程潜力)和Ppk(过程潜力与规格中心的差距)则是扩展了Cp和Cpk的概念,它们分别考虑了规格宽度内的最大可能偏差,即理论上的最佳情况和最差情况。高Pp和Ppk表明过程具有更大的潜力,即使在极端情况下也能保持良好的性能。
在SPC中,理解过程输入和输出的量化至关重要,这是实施控制的基础,而不是先进行控制再寻找依据。预防优于检验的理念强调了通过SPC预防质量问题的重要性,而不是等到产品出现问题后才去修复。SPC通过控制图分析,帮助识别过程中的异常波动,以便及时采取措施维持或提高过程的稳定性。
SPC不仅仅关注产品的最终质量,更重要的是对过程参数的控制,包括原料、机器、人员、方法和环境等因素。它强调在制造阶段就确保质量,因为产品质量是制造出来的,而非通过检查得出。过程控制反馈循环涉及所有这些元素,以及输入、过程、输出和顾客需求的持续沟通。
实施SPC可以带来诸多益处,如减少因过程波动导致的产品质量问题,降低报废率、返工成本和维护费用,提升生产效率,减少库存,保持客户满意度,并有助于降低成本和提高市场份额。统计学在生产中的应用目的包括监控总体性能、消除人为误差、调整规格、减少偏差以及评估规格的适用性。
Cp、Cpk、Pp和Ppk是SPC中衡量过程能力和稳定性的关键工具,通过预防性质量管理,企业能够有效地控制生产过程,提高产品质量,降低内外部成本,从而实现持续改进和竞争优势。
129 浏览量
2023-02-08 上传
2021-09-23 上传
点击了解资源详情
点击了解资源详情
2023-07-14 上传
点击了解资源详情
点击了解资源详情
点击了解资源详情
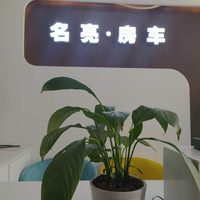
清风杏田家居
- 粉丝: 21
- 资源: 2万+
最新资源
- 智慧工厂数据平台建设方案.zip
- hf_trade_terminal:交易终端
- 毕设源码-VB流动资金贷款业务系统(源代码+系统+答辩PPT+开题报告+外文翻译+文献综述).rar
- golang-kv:将固定的Golang api捆绑到嵌入式DB(Badger&boltdb和leveldb)包装器中
- ramshorncms-api:Ramshorn CMS前端的API服务
- GoogleMapAPI
- js代码-Partion寻找中位数
- 61.原创歌曲分享平台的设计与实现(可运行源码+数据库+设计文档+lw)java期末大作业毕业设计项目管理系统计算机软件工程大数
- Git
- 数据库课程设计-员工工资管理系统
- the-right-price
- 毕设源码-vb电表管理系统(源代码+论文).rar
- COVID-movement
- cene:Cene是易于引导的Lisp方言,具有纯净和JS集成
- 大功率步进电机驱动器DXP资料及其相关资料_51单片机(论文+开题报告+源代码+详解图).zip
- java代码-编写一个程序判断字符串“Tom”是否在另一个字符串“I am Tom, I am from China”中出现。