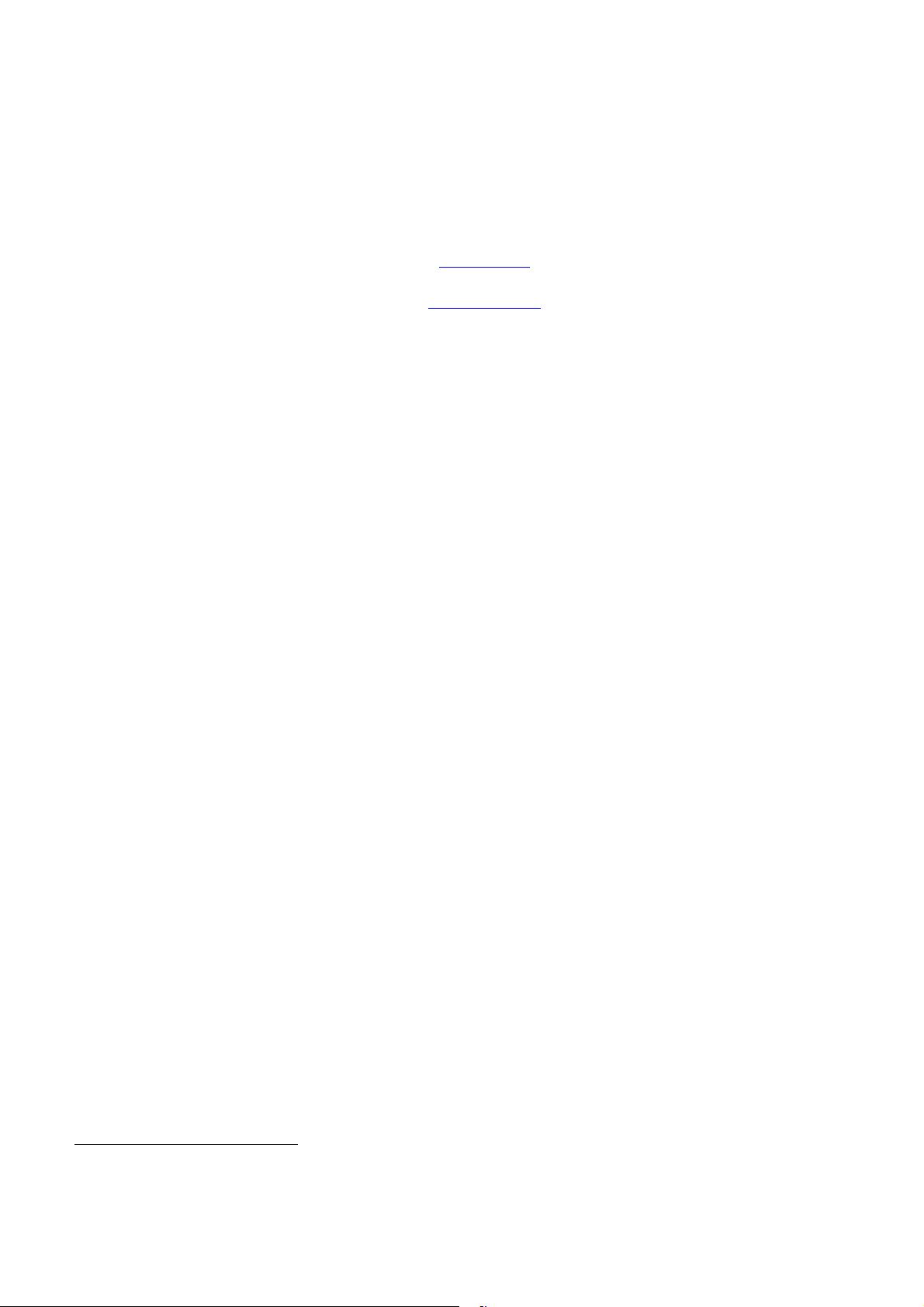
Adaptive cross-coupled sliding mode control for synchronization of
dual-cylinder electro-hydraulic servo systems
SUN Mengfei
1
, LI Jianxiong
1
, FANG Yiming
1,2
1. Key Lab of Industrial Computer Control Engineering of Hebei Province, Yanshan University, Qinhuangdao 066004, China
E-mail: jxli@ysu.edu.cn
2. National Engineering Research Center for Equipment and Technology of Cold Strip Rolling, Qinhuangdao 066004, China
E-mail: fyming@ysu.edu.cn
Abstract: To improve the equality of continuous casting billet, synchronization control is investigated for continuous casting
mold driven by dual-cylinder electro-hydraulic servo systems (EHSS) in this paper. A second-order super twisting sliding mode
controller is developed for each cylinder EHSS, in which cross-coupled errors are employed to construct the sliding mode
surfaces, which guarantee that trajectory tracking errors of each cylinder EHSS and the synchronization error can rapidly
converge to zero in finite time even in presence of the parameter uncertainties and external disturbances. Furthermore, to reduce
the chartering caused by the discontinuous control law of sliding mode control, adaptive gains are employed during the sliding
mode controller design. Thus, an adaptive sliding surface cross-coupled synchronization controller is presented by employing
Lyapunov stability theorems. Simulation results in a model obtained from a real continuous casting mold demonstrate the
effectiveness of the method.
Key Words: Dual-cylinder electro-hydraulic servo systems, synchronization, sliding mode control, cross-coupling, continuous
casting mold
1 Introduction
The mold oscillation is one of the key technologies for
developing high efficiency continuous casting of steel. And
the mold is the key device in continuous casting mold,
which is used for molten steel cooling and solidification, and
the mold oscillates vertically tracking reference trajectory to
avoid adhesion
[1]
. The casting mold oscillation is often
driven by Electro-hydraulic servo systems (EHSS) because
of the EHSS’ high property, such as high power-to-weight
ratio, high stiffness, and high payload capability, and
usually two cylinders are employed to drive the mold. While
in practice the dynamics of the two servo systems are often
different due to the presence of the parameter uncertainties,
unmodeled nonlinearities and external disturbances, which
would cause the two cylinders be asynchronous, and the
asynchronization will affect the quality of the casting billet.
So the synchronization of the continuous casting mold
driven by dual-cylinder EHSS should be considered.
The problem of the synchronization control has always
attracted much attention in recently years. Difference
approaches have been proposed to achieve motion
synchronization for multiple actuators
[2-8]
. PID control
technique adopted in the position loop and/or the cylinder
drives
[2,3]
, but there exist weak robustness of the system
dynamic performance and the inaccurate synchronization
performance in the presence of parameter uncertainties and
unmodeled nonlinearities of the hydraulic components as
well as external disturbances. And then robust control and
fuzzy control strategies
[4,5,6]
were utilized to handle uneven
loads as well as uncertainties and external disturbances
associated with the hydraulic systems. [5] developed a
nonlinear control algorithm based on the estimate of the
disturbance to address motion synchronization of a
*
This work is supported in part by National Natural Science Foundation
(NNSF) of China under Grant 61403332, in part by NNSF of China and
Baosteel Group Co. Ltd. under Grant No.U1260203, and in part by Natural
Science Foundation of Hebei Province under Grant No. F2015203400.
dual-cylinder electro-hydraulic lifting system. [6] proposed
an integrated fuzzy controller consisting of a pair of cylinder
controllers and a motion synchronization controller for
synchronous motion and positioning in a hydraulic lifting
system. In [7], active disturbance rejection controller
(ADRC) was employed to realize the both sides
synchronization control of rolling mill driven by EHSS. [9]
proposed a model-free cross-coupled control for
synchronization of multi-axis motions. The cross coupling
synchronous control method regards the tracking error and
the synchronous error as the input of the controller in each
side
[10]
, and this method can not only accelerate the
synchronous convergence speed, but also simplify the
controller design. And this method is used in this paper.
On the other side, to overcome the uncertainties of the
system, disturbances, sliding mode control (SMC) is
employed in the controller design in this paper. To weaken
the chattering of the SMC, second order super-twisting
SMC
[11,12]
method is employed, in which an adaptive
method is used to estimate the parameters of the controllers.
To sum up, a cross coupled synchronization control
method based on second-order SMC is presented for dual-
cylinder EHSS of continuous casting mold oscillation
system, the Lyapunov functional stability theory and
adaptive estimation method are employed to design the
sliding mode synchronous controller. With the help of the
proposed controller, the system tracking errors and
synchronization error can rapidly converge to zero in finite
time even in the presence of the nonlinearities and
uncertainties and as well the external disturbances.
Moreover, simulation results are given to verify the
effectiveness of the proposed control technique.
2 System modelling and problem formulating
The structure of the dual-cylinder EHSS of continuous
casting mold oscillation system is shown in Fig.1.
Proceedings of the 34th Chinese Control Conference
Jul
28-30, 2015, Han
zhou, China
3361