没有合适的资源?快使用搜索试试~ 我知道了~
工程科学与技术,国际期刊20(2017)1653完整文章AISI1045钢改进钻削工艺的混合优化SaeidAmini,Iman Alinaghian,Mohammad Lotfi,Reza Teimouri,Mahnoush Alinaghian伊朗卡尚卡尚大学机械工程学院制造系阿提奇莱因福奥文章历史记录:2017年5月29日收到2017年9月4日修订2017年11月19日接受2017年11月28日在线发布关键词:优化钻井LS-SVM灰色分析MQL超声振动A B S T R A C T在钻削过程中,可以采用最小量润滑(MQL)和超声振动(UV)的混合方法来改善切削条件和刀具寿命。本文对四种工况下的钻削过程进行了实验分析。普通、MQL、UV和UV-MQL),其中测量了特定旋转主轴速度和进给速率下的推力(Fz)和表面粗糙度(Ra)。在此基础上,提出了一种基于最小二乘支持向量机(LS-SVM)预测模型和灰色关联分析的混合优化方法。获得的结果证据表明,紫外线钻井优于普通和MQL方法。在单目标优化问题中,与普通情况相比,该方法显著降低了推力和表面粗糙度。然后,在多目标优化研究(即灰色关联分析)下,对UV钻井的Fz和Ra的最佳点进行了评估。此外,在UV-MQL钻削中,钻头上较低的组合刃导致较好的表面质量。在切削过程中产生的短切屑和断屑直接影响摩擦系数,从而影响切削力。由于其训练速 度 和 精 度 , LS-SVM 在 优 化 问 题 方 面 表 现 出 优 越 的 性 能 , 其 中 对 于 最 佳 点 ( N= 931 RPM 和 f= 90mm/min),获得了近似的Fz和Ra,误差约为6%。©2017 Karabuk University. Elsevier B.V.的出版服务。这是CCBY-NC-ND许可证(http://creativecommons.org/licenses/by-nc-nd/4.0/)。1. 介绍在钻孔过程中,刀具与工件持续接触,由于摩擦,温度升高摩擦直接影响切削力和表面粗糙度。因此,建议应用MQL和UV来改善这种情况[1MQL是一种有用的润滑方法,能够通过显著减少冷却剂消耗来最大限度地减少对环境的这是通过在刀具表面喷射少量冷却液来完成的。冷却剂薄层减少了钻头切削刃与工件之间的直接接触,从而减少了摩擦[5]。此外,超声波辅助切削是另一种高频振动改变切屑形成的加工工艺[6]。该工艺减少了切屑与钻头表面的接触,从而显著降低了切削力并提高了表面质量。由于混合钻削过程的建模和优化,对于特定的参数,如推力和表面粗糙度是复杂的,因此建议基于实验数据的人工智能和统计方法来找到最优的*通讯作者。电子邮件地址:amini. kashanu.ac.ir(S. Amini)。由Karabuk大学负责进行同行审查溶液Dvivedi和Kumar[7]对纯钛及其合金的超声钻削进行了研究,并采用田口方法评估了最小表面粗糙度的切削参数的最佳设置。Nam等人[8]采用响应面法和遗传算法(GA)对MQL钻孔过程进行优化。在他们的研究中,找到了使钻削扭矩和推力最小化的工艺因素的最佳点。在Saravanan et al.[9]采用遗传算法进行多目标优化,以最小孔偏心极限和最大材料去除率为目标,求出钻头扭矩和进给速度的最佳值。遗传算法作为一种人工智能技术在许多其他研究中[10-在钻削过程中,利用人工神经网络(ANN),以切削速度、进给量和推力为输入值,对UDIMET 720试样的表面粗糙度在这项由Vrabel等人完成的研究[14],从实验装置中收集输入数据,并说明如何将人工神经网络应用于钻井工况监测。Akin和Karpuz用类似的方法进行了比较研究[15]在粗糙度估计的情况Gai- tonde和karnik[16]对钻孔的研究试图使用人工神经网络开发微粒群优化的应用。在这项研究中,机器已经通过提出的人工神经网络进行了训练,以找到最佳的进给值,https://doi.org/10.1016/j.jestch.2017.11.0052215-0986/©2017 Karabuk University.出版社:Elsevier B.V.这是一篇基于CC BY-NC-ND许可证的开放获取文章(http://creativecommons.org/licenses/by-nc-nd/4.0/)。可在ScienceDirect上获得目录列表工程科学与技术国际期刊杂志主页:www.elsevier.com/locate/jestchXðÞXXTi@bnnXXnð Þ22><一杯!w¼n2. 方法22我函数erXXX小行星1654 Amini等人/工程科学与技术,国际期刊20(2017)1653在钻孔过程中最小化毛刺高度和毛刺厚度的角度点。在这种情况下,粒子群优化算法(PSO)被用来搜索最优点。2007年,Gaitonde和karnik[17]Noorul Haq等人[18]评估了切削速度、进给和尖角的最佳值对应于表面粗糙度、切削力和扭矩的多个响应量。该方法先用正交表和灰色关联分析法进行分析,再用方差分析法确定各参数的贡献率。Tosun[19]使用灰色关联来确定最佳钻孔参数,以最大限度地降低毛刺高度和表面粗糙度。MQL和UV辅助加工等混合方法的应用使切削力和表面粗糙度的预测变得复杂。具体来说,当数据量很小时,即使是人工智能方法和数据挖掘方法在估计和优化过程其中ai是可以在训练机器之后获得的常数,b是可以称为BIOS的常数。Kx;xi可以被称为核函数,其中它的各种形式在表1中示出。常用的核函数有线性核函数、多项式核函数和径向基函数,并给出了相应的函数。对于非线性问题,通常采用RBF。一旦要解决这个优化问题,最好创建拉格朗日函数:nL1w;b;ni;ai;mi;I1w;ni-aifyi½wTuxib]g-1nig1/1n-cini 21/1哪里n表演,也是。在这种情况下,可以应用像支持向量机(SVM)在最小w;niI1w;ni12019 - 02 -23 01:03:001/1摘要提出了一种新的支持向量机方法,即最小二乘支持向量机(LS-SVM),用于超声振动和最小润滑钻削过程的实验输入和输出(即目标)数据集的函数估计。旋转速度(N)和进给速率(f)被认为是输入数据集,粗糙度(Ra)和推力(Fz)是响应。输入值与各目标值之间的关系(即Ra和Fz)可以是其中系数ai≥ 0 ci≥0 ci 1;. ;n是拉格朗日乘数,ni是不可分数据的误差,但ci被称为正则化参数。找到最佳点的解可以通过以下条件获得:8>@LX1/1最后,将最小二乘支持向量机(LS-SVM)与最小二乘支持向量机(LS-SVM)进行匹配,分别得到最小Ra和最小Fz的一个最优点,@L1½0! aiyi¼01/1@nii¼ 1;.. . ;n;ð4Þ通过灰色分析。:>个@L1½0 !0 ≤ai≤c;在本节中主要介绍了支持向量机和最后给出了其最小二乘解,并进行了灰色关联分析。如果uxTux ikx;x i,则等式(3)可以改写如下:1maxa Q 1ai; kx i; x m-y y kx i; x maiamai5对多目标优化问题进行了分析,建立了相应的数学模型。最后,两步优化(即,单目标和多目标优化)算法我这取决于:nI mi;k¼11/1以阐明优化过程。2.1. SVM和LS-SVM最初,支持向量机被引入解决模式识别问题[20]。该方法能够将数据映射到高维空间,通过构造最优超平面来分离数据。分离的数据被用作分类模式或找到输入和输出之间的关系的函数。根据可分离和不可分离的数据输入集,可以使用各种SVM模型。基于在这一领域进行的发展,对于SVM的最新版本,[21]引入的最小二乘支持向量机(LS-SVM)被用作不可分割数据集的预测。LS-SVM的支持值与误差成比例而对于经典的SVM,他们认为是零。以下部分aiy i<$0; 0 ≤ ai≤ c; i <$1;.. . ; n;1061/1当量(5)是基于核函数编写的,因此不需要计算w和ux来找到决策曲面[22]。2.1.2. 最小二乘支持向量机最小二乘误差模型的SVM分类器可以重写为拉格朗日函数:nL2w;b;e;al2w;b;e-aifyi½wTuxib] -1eig71/1哪里min w;b;eI2w; b; e 1 w Twc1 Pe 2,和通过应用1/1Suykens和Vandewalle在1999年[21]提出了SVM和LS-SVM的数学模型。2.1.1.支持向量机它假设给定的训练集有n个数据点fxi;yij1≤i≤ng,其中x i R n是输入点,y i R是输出点。支持向量机即将分类器做成如下形式:Karush-Kuhn-Tucker(KKT)最优性条件[22]表1通用内核函数。核函数注释Linearx:xi这是多项式函数的一个特例Polynomial1/2 <$x;xi<$1]pPower p由用户先验指定“Xn#1/1径向基宽度r2由用户n@waiyiuyx符号aiykiKx;x ibð1Þ2>@bð Þ ð ÞXð Þ<@L2¼0!Dmin:@ai 1/4!我我nn哪里K 是区分系数0联系我们1(k)= 0.5是正式的),>8X@wS. Amini等人 /工程科学与技术,国际期刊20(2017)1653-16611655其中k在1到对象数之间Func. m是数量@L2¼0!w¼>X1/1 aiyiu数据灰色关联系数的计算方法如下方程式:1/1>@L2¼0!0≤a≤c;i/1;.. . ;n;ð8ÞnikD0iDmaxð11Þ>@L3@ei我wT½uxib] -1ek¼0;i¼ 1;.. . ; nD0i kkx0k-xi kk12对于上述目标函数和KKT约束,拉格朗日乘子a和biosb系数可以通过将它们应用于以下方程来计算,函数y(x)Dmin是D0i的最小值,Dmax是D0i的最大值。在对灰色关联系数进行平均之后,灰色关联度ci可以计算为:它可以通过RBF核函数n n估计任意输入集xKx; x。估计函数y(x)可以写成如下:nyxaiKx;xib 91/4为了显示函数如何工作,函数估计y(x)的架构在图1中呈现。2.2. 灰色关联分析灰色关联度分析(GRA)可以用来解决多目标问题。它可以有效地用作实验数据的复杂多目标优化方法。该方法能将多个响应特征转化为一个灰色关联度(GRG)。程序是所有的质量特性都应该标准化,以找到0到1之间的数量。其次,基于归一化数据计算灰色关联系数。然后对各系数取平均值,得到灰色关联度(GRG)。最后由GRG值中最大值的位置决定最优值的位置。在这项研究中,有两个目标函数,一个是Fz,一个是Ra。Fz和Ra的灰色系数应分别计算,然后对系数取平均值,得出这两个参数的GRG数据可以通过以下方式进行标准化最大xmk-xm kc/1Xwini; Xwi¼11 3k¼1k¼1其中n是过程响应的数量,wi是与多目标问题中每个响应的优先级相关的在目前的工作中,平等的权重因素(即。0.5),所有的答案都考虑在内2.3. 基于LS-SVM和灰色关联分析的优化方法支持向量机的最小二乘版本可以用于优化问题,特别是在加工领域。最小二乘支持向量机模型是一种强有力的工具,它可以通过一些输入和目标数据集进行训练。新生成的N和f的最小值和最大值之间的100个随机值应用于函数估计(y),可以是力或表面粗糙度,以评估新的100个力[23]。然后对这些新值进行排序,得到相应转速和进给量下的最小力。应该注意的是,随机数据是在约束(即每个输入的下限和上限)之间生成的。在本研究中,转速可以取828和955(RPM)之间的值,在进料速率的情况下,它们是83和165(mm/min)。此外,LS-SVMlab v1.8 Matlab工具箱已被用于基于输入(N和f)和目标(力)值来估计函数。为最大值xmkðkÞð10Þ每种类型的加工(普通,MQL和超声波)随机优化已经完成,结果报告在下一节。在本研究中,径向基函数核被认为是在算法中,由于其独特的能力,在非线性建模问题。在LS-SVM算法中,除了输入和目标训练数据集之外,还需要输入训练机器需要两个参数:带宽λr和正则化参数c在本研究中,R2和C分别选择了10和15的数量[24]。在第二部分中,采用基于灰色模型的多目标优化,以获得所有两个响应的最优点(即,Fz和Ra)。GRA是由于无法提出单目标随机优化。在本研究中,GRA部分被用于仅在一定的条件下,已经从以前的算法中选择的钻孔最优化问题的方法流程图如图所示。 二、3. 的实验Fig. 1. 功能估计的架构。钻孔实验已经在配备有超声波和MQL设置的4301TABRIZ CNC铣床上进行,如图所示。3.第三章。超声波装置包括旋转头、压电环、升压器、喇叭和MPI电源(图1)。 3)。有限元分析(即模态分析)设计合适的变幅杆,以有效地将超声振动从换能器传递到钻头。将测得的频率输入电源装置naiyi¼ 0克·DMax小行星1656 Amini等人/工程科学与技术,国际期刊20(2017)1653图二. LS-SVM辅助优化流程图图三. 实验装置。并通过LABVIEW软件进行验证。在超声波振动下的钻孔过程中,钻头以20 kHz的频率和10m m的振幅线性振荡。提供了手工MQL设置,以形成纳米-在钻头和工件表面形成液雾。MQL喷嘴瞄准加工区,以有效支持钻孔期间的纳米流体喷射。通过一系列的初步实验,得到了MQL参数的最佳条件最后,最佳MQL的流速、注射频率、循环次数和进气压力分别为100 ml/h、10cycle/min和4 bar。此外,MQL装置(Royal-R50)用于提供润滑条件。为了避免传统切削液的环境缺点,使用Accu-lube FG-2000植物油。壁的表面粗糙度通过使用马赫粗糙度测试仪(MarSurf PS1)测量。此外,钻头尖端的照片S. Amini等人 /工程科学与技术,国际期刊20(2017)1653-16611657表2钻孔加工的切削条件。用视觉测量机(VMM)测量芯片的大小。所有实验均在AISI 1045碳上进行切削条件描述具有尺寸为150*75*10 mm带材几何形状的钢3.使用具有5mm直径的HSS钻头普通这种情况代表普通钻孔,这意味着没有润滑剂,补充过程等。MQL这意味着最小量的液体用作润滑剂。UV这是一个补充过程,可以与钻孔过程结合。在这种情况下,工具沿其轴线具有线性UV-MQL顾名思义,它是MQL和UV的组合。这意味着存在润滑或超声波振动。在进行每个实验期间,通过测力计KIS-TLER 9257 B测量推力。以主轴转速、进给量和钻削方式为工艺因素,采用面心中心复合设计(FCCCD)进行试验设计。对于9组输入的转速(N)和进给速率(f),已经获得了以下结果。作为它可以可以看出(表2),在四种条件表3用于训练的实验数据集。号输入值输出值普通MQLUVUV-MQLN(RPM)f(mm/min)Fz(N)Ra(mm)Fz(N)Ra(mm)Fz(N)Ra(mm)Fz(N)Ra(mm)1828835505.115004.614724.534284.1828281247655.926955.346745.866165.0138281659586.438705.88685.97975.564891834503.884093.53863.443552.9758911246284.495704.055534.064893.868911658384.887624.47594.486814.267955834193.323812.993592.943212.7189551245903.845163.465203.474713.2599551657554.176863.766843.836293.49见图4。用于以下的输入训练数据集的推力的估计函数的曲线图:(a)普通钻孔,(b)MQL钻孔,和(c)UV钻孔,(d)UV-MQL钻孔。小行星1658 Amini等人/工程科学与技术,国际期刊20(2017)1653(i.e.普通,MQL,超声振动和UV-MQL),对于每种钻孔条件,测量推力(Fz)和表面粗糙度(Ra)。4. 结果和讨论本节表示从实验和LS-SVM算法获得的结果。它包括三个小节。第一个是推力和表面粗糙度的Meta模型,描述了它们在各种切削条件下的函数估计。第二种是基于最小二乘支持向量机的单目标随机优化方法,对切削条件下的推力和表面粗糙度进行了比较。为了更好地理解两个单目标优化问题之间的最优点,第三部分给出了基于GRA和LS-SVM的多目标优化问题。最后,为了支持这些结果,给出了最后一部分关于积屑和切屑形成的研究(表3)。4.1. Fz Ra如前所述,表2中的力和表面粗糙度的训练集值已经被馈送到LS-SVM算法中,以函数估计输入(Nf)和输出(Fz Ra)集。此外,对于每个特定的N和f,存在单独的值在一定的加工条件下(即普通、MQL、UV和UV-MQL)的力和表面粗糙度。因此,可以得到预测推力和表面粗糙度的总共六个函数。每个函数都可以通过其特定的a和b系数在某些条件下的力函数和表面质量的图示在图1和图2中给出。分别为4和5。对于每种类型的加工功能,估算如下图所示。黑色LS-SVM的建模时间仅为几分之一秒(在本研究中约为0.011 s),这表明它比多层感知器神经网络等其他建模方法快得多。4.2. 基于LS-SVM的为了进行单目标优化,在四种切削条件下,将N和f的100个随机生成值应用于力相关的Meta模型(预测模型)中,该元模型通过前一节中的训练LS-SVM算法获得,因此可以获得每个条件下的推力的100 个值,然后评估和绘制每个特定Fz的最小值(对于普通、MQL、UV、UV-MQL钻井),此外,结果如图6a所示对表面粗糙度(Ra)采用了类似的方法,结果如图2所示。 6 b. 关于绘制的结果,可以推断,对于UV条件可以获得更好的切割条件。UV钻孔使推力减小约14%,而MQL钻孔使推力减小约10%。由于在UV条件下钻孔过程中的力减小,这导致刀具寿命的显著改善在表面粗糙度的情况下,可以实现类似的方法,因此可以观察到MQL和U.V钻孔条件下几乎减少了11%此外,最佳N和f为931 RPM和90 mm/s。图五、输入训练数据集的表面粗糙度估计函数图:(a)普通钻孔,(b)MQL钻孔,(c)UV钻孔和(d)UV-MQL钻孔。S. Amini等人 /工程科学与技术,国际期刊20(2017)1653-16611659图六、比较各种钻孔条件(包括最佳点)的最小值:(a)推力(b)表面粗糙度。最大推力为954 RPM,最大推力为110 mm/min。根据上述结果可以推断,从力的角度来看,UV钻削比普通钻削和MQL钻削好得多,但从表面粗糙度来看,MQL钻削和UV钻削差别不大,可以得到相似的最后,本文提出了UV钻削技术,以减小推力,提高孔的表面质量,而超声振动技术与MQL技术相结合,更能减小最小推力,提高孔的表面粗糙度。与普通钻削相比,该复合钻削技术可使最小推力降低因此,UV-MQL钻孔可能是其他钻孔工艺中的最佳选择。4.3. 基于GRA和LS-SVM如前所述,在UV-MQL条件下钻孔可提供最小的推力和表面粗糙度。但在UV-MQL条件下,钻削过程中应存在一个最佳点,使钻削过程中同时提供的推力和表面粗糙度最小。为了利用灰关联分析选择最优解,首先必须对实验数据进行归一化(灰关联生成)。对于推力和表面粗糙度,选择了更好的标准。表4给出了灰色关联生成、灰色关联系数和灰色关联度,它们是由方程计算的。10每个响应的这些系数已被累积以评估灰色关联度(Eq. (13)),其是推力和表面粗糙度的总体代表(表4)。从而将多目标优化问题转化为等价的单目标函数优化问题.最佳值是GRG在该点具有最大值的地方,该点应该具有最小可能的推力和表面粗糙度。对于N和f的100个生成值,可以在第72行获得931 RPM和90mm/min的量,其中灰色关联度有其最大值(GRG = 0.5)(见表4)。对于该最优点,Fz和Ra分别为364(N)和3.10(mm),这与单目标随机优化几乎4.4. 积屑瘤与切屑形成的研究结果背后的逻辑可以通过理解刀具失效和切屑形成来解释.钻削过程中切屑的形成直接影响着钻削推力的大小。由于切屑和钻头之间的接触面较大,连续且较长的切屑会增加摩擦力和推力[25]。可以观察到,在UV条件下钻孔产生破碎和短切屑(图7c),南纬1660号Amini等人/工程科学与技术,国际期刊20(2017)1653表4灰关联代数、D0i和灰关联系数.行输入灰关联生成D0i灰色关联系数灰色关联度号N(rpm)f(mm/min)菲兹岭FZRAFZRA19501420.5220.78950.4780.21050.51130.7038 0.30382923900.98240.95860.01760.04140.9660.9236 0.47243861890.81860.57940.18140.42060.73380.5431 0.319249161430.40980.59020.420.45860.5435 0.25055849830.83290.54040.16710.45960.74950.5211 0.317669111630.18370.41870.81630.58130.37980.4624 0.210679331260.64480.79520.35520.20480.58470.7095 0.323589371130.79260.89940.20740.10060.70680.8325 0.384899501420.24460.28570.75540.71430.39830.4118 0.303872931901 100110.50美元908951290.60390.47050.39610.52950.55790.4857 0.2690918621050.84460.96780.15540.03220.76280.9394 0.2609928701120.24830.17140.75170.82860.39950.3763 0.4256939481100.34370.45470.65630.54530.43240.4783 0.19399485713900.035710.96430.33330.3415 0.2277958991440.19220.39590.80780.60410.38230.4529 0.1687968591630.8509 0.9940.14910.0060.77020.9882 0.2088979051600.68960.41980.31040.58020.6170.4629 0.4396989541100.34990.67710.65010.32290.43470.6076 0.270099846970.60990.35380.39010.64620.56180.4362 0.26061009471580.36830.23960.63170.76040.44180.3967 0.2495图7.第一次会议。用于:(a)普通、(b)MQL、(c)UV、(d)UV-MQL钻孔的组合刃口和切屑形成因此,超声波辅助钻孔提供了更少的所需力,使得这是证实图1中所示结果的证据。早上6积屑瘤是刀具失效的一种形式,直接取决于切削力。此外,堆焊刃厚度越大,对工件表面粗糙度的影响越大,微槽深度也越大。如前所述,UV钻孔降低了推力,从而由于切削刃和工件表面的不连续接触而导致较低的组合刃(图7c)。表面粗糙度的结果(图6b)也可以有力地支持这一点,该结果说明UV在改善表面质量方面具有更好的性能。 所有上述主张,积屑边缘和切屑形成的变化,在一定的条件下(见图。 7)。 在普通钻井中,大的钻屑利用率和长的连续切屑(图1)。 7 a)可以观察到,这使表面质量差,增加了切削力。超声振动钻削使钻头上的积屑瘤区变薄,形成断屑(图 7 c),这导致更光滑的表面粗糙度和更小的切削力。MQL钻孔显示出更好的切削力和表面质量后,UV钻孔(图。 7 b)。 然而,尽管有上述所有条件,UV和MQL条件的组合与其他条件相比提供了最小的BUE,并且芯片也像UV一样破碎(图11)。 7 d)。通过实验尝试确认了最佳值,并获得了最佳和最佳结果的约5- 7%的误差。实验结果表明,基于LS-SVM的算法能够很好地处理优化问题。5. 结论在本研究中,已进行了实验,以评估推力和工件的表面质量这涉及四种条件下的钻井过程(ordi-S. Amini等人 /工程科学与技术,国际期刊20(2017)1653-16611661Nary、MQL、UV和UV-MQL)。提出了基于最小二乘支持向量机和灰色关联分析的单目标和多目标优化算法,以获得在表面粗糙度和所需力最小的条件下的最佳转速和进给速度。此外,积屑瘤和切屑形成的相互作用,明确解释了推力和表面粗糙度在每个切削条件下。简而言之,可以给出以下结果:与普通钻孔相比,超声振动下的钻孔显著降低了所需的力(14%)和表面粗糙度(11%),与MQL方法相比,降低幅度更大。然而,与其他条件相比,UV和MQL的组合提供了最小的推力和表面粗糙度。从单次随机的角度来看,所有四种类型钻孔的最佳力点对于最小推力的观点等于N= 931(RPM)和f= 90(mm/min),并且在表 面 粗 糙 度 的 情 况 下 , 它 等 于 N = 954 ( RPM ) 和 f= 110(mm/min)。关 于 多 目 标 优 化 , 推 力 和 表 面 粗 糙 度 的 最 佳 点 等 于 N = 931(RPM)和f= 90(mm/min),使得它同时使它们最小化。在UV和UV-MQL条件下进行钻削时,会产生断屑,从而减少了刀具与切屑之间的摩擦,从而降低了所需的力。因此,在钻削过程中应用超声振动可以获得最小的切削力。而且在UV-MQL条件下钻孔时,其下降幅度更大。UV-MQL钻削减少了钻头上的积屑瘤,从而获得更好的表面质量这是由于工具和工件之间的摩擦力较低引用[1] E.A. Rahim,H.李文,高强度切削液对钛合金表面完整性的影响,硕士论文。Eng.Mater.443(2010)359-364,https://doi.org/10.4028/www.scientific.net/KEM.443.359。[2] R. Heinemann,S.兴都贾湾巴罗湾Petuelli,MQL对刀具寿命的影响小麻花钻在深孔钻削中的应用,Int.J.Mach.ToolsManuf.46(2006)1https://doi.org/10.1016/j.ijmachtools.2005.04.003[3] S.阿米尼湾索莱马尼湾帕克蒂纳特湾Lotfi 2016超声辅助钻井中纵扭振动的影响制造过程。1 7[4] M. Lotfi,S.Amini,超声辅助钻孔的实验和数值研究,超声75(2017)185-193。[5] B.L. 泰,地方检察官。Stephenson,R.J.Furness,A.J.Shih,Minimum quantitylubricating ( MQL ) in automotive powertrain machining , Procedia CIRP(2014)523-528.[6] M. Lotfi,S.Amini,2016,超声振动对刀-屑界面摩擦行为的影响机械工程师学会会刊,B部分:工程制造杂志,0954405416666895。[7] A. Dvivedi,P.Kumar,通过田口技术进行超声钻削的表面质量评价,Int. J.Adv. 制造商Technol. 34(2007)131doi.org/10.1007/s00170-006-0586-3[8] J.S.南,智-地Kim,H. Chung,S.W. Lee,使用响应曲面法和遗传算法优化环境友好的纳 米 流 体 最 小 量 润 滑 的 微 钻 削 过 程 , J. Clean Prod. 102 ( 2015 )428https://doi.org/10.1016/j.jclepro.2015.04.057[9] M. Saravanan,D.拉马林加姆湾Manikandan,R.R. Kaarthikeyen,使用遗传算法的钻井参数的多目标优化,Procedia Eng.(2012)197-207。[10] S. Jayabal,U.Natarajan,使用Nelder-Mead和遗传算法方法对椰壳纤维增强复合材料钻孔中的推力、扭矩和工具磨损进行优化,Int. J. Adv. Manuf. Technol.51(2010)371 doi.org/10.1007/s00170-010-2605-7。[11] R.Q. Sardinas,P. Reis,J.P. Davim,基于遗传算法的层压复合材料钻孔切削参数多目标优化,Compos. Sci. 66(2006)3083https://doi.org/[12] V.N. Gaitonde S.R. Karnik,B.T. Achyutha湾Siddeswarappa,基于遗传算法的AISI 316L不锈钢钻孔毛刺尺寸最小化,J。Mater. 工艺技术 197(2008)225https://doi.org/10.1016/j。 jmatprotec.2007.06.029。[13] G. Kanagaraj,S.G. Ponnambalam,W.C.E.林,应用布谷鸟搜寻-基因演算法于PCB钻孔路径最佳化之研究,IEEE Int. Conf. 自动Sci. Eng. (2014)373-378。[14] M. 弗拉贝尔岛Mankova,J. Beno,J. Tuharsky',钻孔时使用人工神经网络预测表面粗糙度https://doi.org/10.1016/j.proeng.2012.09.572[15] S.阿金角张文龙,金刚石钻头钻进参数的人工神经网络预测,北京:机械工程出版社。8(2008)68-[16] V.N. Gaitonde S.R.张文,张文,等.人工神经网络-粒子群优化方法在钻削中的应用. 内特尔制造商23(2012)1783https://doi.org/10.1007/s10845-010-0481-5[17] S.R. Karnik,V.N.Gaitonde,人工神经网络模型的开发以研究过程参数对钻孔中毛刺 尺 寸 的 影 响 , Int.J.Adv.Manuf.Technol.39 ( 2007 ) 439https://doi.org/10.1007/s00170-007--453,www.example.com 1231-5。[18] A.N. Haq,P.马里穆图河Jeyapaul,在田口方法中使用灰色关联分析对钻孔Al/SiC金属基复合材料的加工参数进行多响应优化,Int. J. Adv. Manuf. Technol. 37(2008)250 https://doi.org/10.1007/s00170-007-0981-4。[19] N.陶松,用灰色关联分析确定钻井多性能特性的最佳参数,国际工程技术期刊。 J.Adv. 28(2005)450https://doi.org/10.1007/s00170-004-2386-y[20] C. Cortes , V. Vapnik , Support Vector Networks , Mach. 学 习 . 20 ( 1995 )273https://doi.org/10.1007/BF00994018[21] JAK 杨 文 , 最 小 二 乘 支 持 向 量 机 分 类 器 , 神 经 网 络 。 9 ( 1999 )293https://doi.org/10.1023/[22] R.王文,最优化方法,北京,高等教育出版社,1998。10.2 30 7 /2008742。[23] F. Dobeville,P. DymácZelek,M. Besterci,通过小冲头试验对等径角挤压后铝和 铝 复 合 材 料 的 机 械 性 能 的 估 计 , Mater 。 Sci. A 626 ( 2015 )313https://doi.org/10.1016/j.msea.2014.12.054[24] JAK Suykens,T. Van Gestel,J. De Brabanter,B.李明,2002,最小二乘支持向量机,北京。[25] S.阿米尼湾Lotfi,H.帕克蒂纳特湾张文,高振强。Technol.J. 20(2)(2017)403-410。●●●●●
下载后可阅读完整内容,剩余1页未读,立即下载
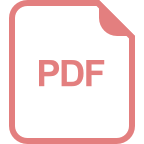
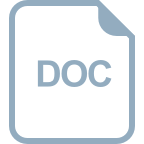
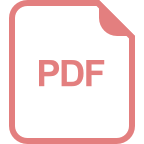
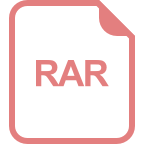
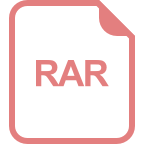
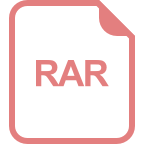
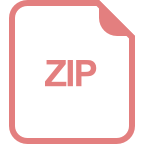
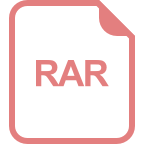
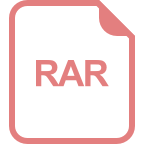
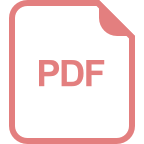
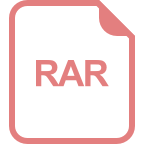
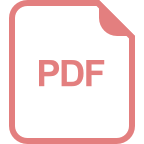
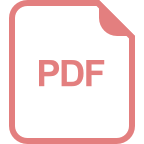
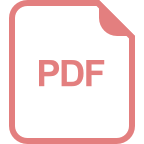
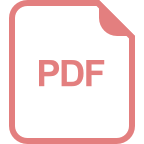
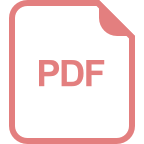

cpongm
- 粉丝: 5
- 资源: 2万+
上传资源 快速赚钱
我的内容管理 展开
我的资源 快来上传第一个资源
我的收益
登录查看自己的收益我的积分 登录查看自己的积分
我的C币 登录后查看C币余额
我的收藏
我的下载
下载帮助

最新资源
- 前端协作项目:发布猜图游戏功能与待修复事项
- Spring框架REST服务开发实践指南
- ALU课设实现基础与高级运算功能
- 深入了解STK:C++音频信号处理综合工具套件
- 华中科技大学电信学院软件无线电实验资料汇总
- CGSN数据解析与集成验证工具集:Python和Shell脚本
- Java实现的远程视频会议系统开发教程
- Change-OEM: 用Java修改Windows OEM信息与Logo
- cmnd:文本到远程API的桥接平台开发
- 解决BIOS刷写错误28:PRR.exe的应用与效果
- 深度学习对抗攻击库:adversarial_robustness_toolbox 1.10.0
- Win7系统CP2102驱动下载与安装指南
- 深入理解Java中的函数式编程技巧
- GY-906 MLX90614ESF传感器模块温度采集应用资料
- Adversarial Robustness Toolbox 1.15.1 工具包安装教程
- GNU Radio的供应商中立SDR开发包:gr-sdr介绍
资源上传下载、课程学习等过程中有任何疑问或建议,欢迎提出宝贵意见哦~我们会及时处理!
点击此处反馈


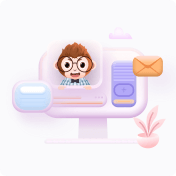
安全验证
文档复制为VIP权益,开通VIP直接复制
