没有合适的资源?快使用搜索试试~ 我知道了~
正交面齿轮在油浴中搅动损失的计算及飞溅润滑试验
pp工程科学与技术,国际期刊41(2023)101383正交面齿轮Xiang Zhu,YuDai中南大学机电工程学院,长沙410083阿提奇莱因福奥文章历史记录:2022年12月15日收到2023年2月16日修订2023年3月9日接受关键词:搅拌损失理论模型正交面齿轮飞溅润滑试验验证A B S T R A C T作为正交面齿轮在油浴中运行的基本消能方式之一,面齿轮的搅动功率损失还没有公开的本文提出了一系列计算正交面齿轮在油浴中半浸运行时的搅动损失的公式。搅动阻力的分析模型基于流体力学和边界层理论,其能够以最小的努力定量计算旋转速度、流体属性和齿轮几何构造的影响。然后,建立了一个特设的试验台,进行了特定的飞溅润滑试验单面齿轮在不同的转速和初始浸入深度。最后,考虑搅拌和风阻效应,采用实时浸入深度代替静态浸入深度,建立了飞溅润滑面齿轮非载荷损失的从这一点来看,理论结果进行了比较,以及与直接测量的实验结果。同时,还利用该模型定量计算了飞溅润滑条件下面齿轮各部分对总的载荷无关损失的贡献。©2023 Karabuk University. Elsevier B.V.的出版服务。这是CCBY-NC-ND许可证(http://creativecommons.org/licenses/by-nc-nd/4.0/)。1. 介绍汽车或航空工业对高功率密度的需求持续飙升,促使人们开发精确的方法来计算齿轮传动系统的效率,以减少能耗,防止过热,避免故障并延长使用寿命。面齿轮传动被认为是一种新型的、特殊的圆柱齿轮与锥齿轮啮合的传动形式,并以其众多的优点在武装直升机传动中得到了很好的应用[1即使对于设计良好的齿轮系统,其效率可以达到98%至99%,传输功率超过100 MW,超过2 MW的能量耗散也不能忽略[4]。一般认为,能量损失分为与负载有关的损失和与负载无关的损失。前者主要来自于齿轮啮合摩擦,由此产生的功率损失可根据齿轮部分油膜轴承的混合EHD润滑理论计算[5后者是由流体阻力产生的,包括无润滑或喷油润滑时的风阻损失和飞溅润滑时的搅动损失当齿轮切向速度超过*通讯作者。电子邮件地址:210143@csu.edu.cn(Y. Dai)。https://doi.org/10.1016/j.jestch.2023.1013832215-0986/©2023 Karabuk University.出版社:Elsevier B.V.100 m/s时,表明与负载无关的损失(搅动损失和风阻损失之和)可能占总齿轮损失的50%以上【8,9】。因此,研究一种有效的中低速飞溅润滑面齿轮传动的搅动损失预测方法,对于提高其润滑和传动性能,扩大其工程应用范围是十分必要的。针对搅动现象,人们广泛地研究了最常见的圆盘或圆柱齿轮部分或全部浸没在油浴中旋转运动所产生的搅动力矩。目前,直齿圆柱齿轮的搅动损失预测模型很多。根据大量的实验数据和拟合分析,Terekhov等。[10]根据流体推导出阻力矩Tch特性(油密度q油)、工作参数(角速度x)、齿轮特性(节圆半径Rp、齿面宽度b)和无量纲搅动扭矩Cch,表示为:Tch 1/4克机油x2bR4C通道其 中 , 无 量 纲 扭 矩 Cch 与 流 态 相 关 联 取 决 于 雷 诺 数 Re(Re=qoi1xRo2/loi1)和弗劳德数Fr(Fr1xRo=gh),具体如下:如果围绕旋转齿轮的油流是层流,(10Re = 2250),Re- 0.6Fr-0.25> 8.7× 10- 3,则:这是一篇基于CC BY-NC-ND许可证的开放获取文章(http://creativecommons.org/licenses/by-nc-nd/4.0/)。可在ScienceDirect上获得目录列表工程科学与技术国际期刊杂志主页:www.elsevier.com/locate/jestchX. Zhu和Y. 戴工程科学与技术,国际期刊41(2023)1013832.- 是的- 是 的Σp.- 是的- 是 的Σ.- 是的- 是的Σ.- 是的- 是 的ΣDC第四章O:=00=0ch0 0ODCh v I¼Cch4:57 Re-0:6Fr-0:25 h=Rp一比五 b=Rp-0:4Vp=V0-0:5 2- 1否则:Cch2:63 Re-0:6Fr-0:25h=Rp1:5b=Rp-0:17Vp=V0-0:732 - 2如果是湍流(2250 Re 36000),则:Cch20:373 Re-0:3Fr-0:25h=Rp1:5b=Rp-0:124Vp=V0-0:5762 - 3其中Vp和V0分别表示齿轮的浸没体积和总油体积在忽略流态影响的情况下,Lauster和Boos[11]建立了行李箱变速器特有的无量纲扭矩Cch的Cch 2:95 Re-0:15 Fr-0:7 h=Rp一比五 b=Rp-0:4Vp=V0-0:53Boness[12]提出了部分浸没在油中运行的齿轮的搅动扭矩,给出为:Tch 1/40: 5qoilx2Sm R3Cch40与方程(1)相比,方程(4)考虑了油润湿表面积Sm的影响,并且同样,Cch也取决于流态,写为:关于层流区(Re 2000)Cch1/420=Re1/4-10过渡区(2000 Re 100,000)Cch¼8: 6× 10- 4Re1= 3μ 4 -2 μ湍流区(100,000 Re)Cm¼5× 108=Re2μ 4 -3 μ随后,考虑到两种流动状态,Changenet等人[13,14]提出了一系列经验或半经验公式,以根据尺寸分析和实验验证精确评估单个小齿轮或小齿轮-齿轮副的阻力损失在此基础上,Laruelle等人[15]和Fossier等人[16]分别建立了一个专门的试验台来量化飞溅润滑弧齿锥齿轮的阻力矩,同时改进了直齿轮的阻力公式来应用于锥齿轮,如下:对于层流区(Re≤ 20000)C1/4:5R e-0:2 5Fr-0:5 3μh=Re0:1 5。V=R3-0:25-1对于湍流区Re > 20000搅拌功率损失。在直齿圆柱齿轮方面,Chernoray和Jahanmiri[27]研究了在不同转速下绕光滑轮和直齿圆柱齿轮的两相流。诺伊罗特等人[28]通过实验探索了在不同操作条件下一个小齿轮和一个小齿轮-齿轮副之间的关系。据报道,通过利用一些轴向可移动壁的杠杆作用,搅拌损失将显著减少[29刘等人[32,33]和Conclusion等人[34-Li等人[40]使用了三种替代的移动网格策略(即动态网格[DM]、滑动网格和浸入实体方法)来探索齿轮搅动功率损失。至于螺旋锥齿轮,Arisawa等人[41]开发了一种CFD技术,用于分析无护罩和有护罩螺旋锥齿轮的油搅动和风阻损失。Peng等人[42]描述了模拟准双曲面齿轮箱中飞溅油流以及油分布和搅动损失的数值方法。Hu等人[43-一般来说,没有公开的文献对搅动飞溅润滑条件下面齿轮的功率损失严重限制了其性能的提高和工程应用。因此,本文提出了一种基于物理的分析方法,在考虑搅动和风阻特性的情况下,预测正交面齿轮在油底壳中部分啮合时的搅动功率损失,该方法能够以最小的努力定量计算转速、流体属性和齿轮结构特性然后,建立了一个特设的试验台,在不同的转速和初始浸入深度进行特定的飞溅润滑试验最后,将基于该模型的理论计算结果与直接测量的实验结果进行了比较和验证2. 搅拌损失.面齿轮飞溅润滑面齿轮的搅动行为与螺旋锥齿轮的搅动行为类似,与负载无关的损失来自旋转面齿轮与周围油或空气的相互作用按照Dai等人的观点,部分或全部浸没的面齿轮的搅动功率损失Pch可分为三部分:前/后端面的损失Pf,C0 12 Fr-0:53h R0:15。VR3-0:25-2侧面Pp以及齿Prf。此后,Quiban等人[17]注意到由风阻现象引起的幻影,改进了考虑风阻效应的部分浸没螺旋锥齿轮的总空载损失分析模型,其有趣的计算结果与实验一致。然而,这些由实验得出的经验公式低估了牙 形 的 影 响 , 似 乎 不 符 合 物 理 规 律 . 为 了 缓 解 这 一 矛 盾 ,Seetharaman等人[18,19]引入了一种基于边界层理论的理论物理模型,以估算典型的与负载无关的功率损耗,包括搅动和风阻2.1. 侧面功率损失如Seetharaman et al.[18,19]中,作用在周边上的阻力扭矩源于周围的润滑油,而齿侧处的相应功率损失是扭矩和油速的乘积 根据简化的Navier-Stokes方程,沿半径方向的速度分布v_h_(?)和压力分布p可表示为[18,19]:正/斜齿轮的性能。受此启发,Dai等人[20]最近提出了进一步改进的螺旋锥齿轮搅动损失物理模型。由于计算流体的迅速发展,v和xr2r7动力学(CFD)技术[21的复杂性的油流周围的齿轮运行部分沉浸在油浴,以及预测的qoiljujujujujujujujujujujujujujujujujujujujujujujujujujujujujujujujujujujujujujujujujujujuð8ÞðÞPch< $PpPf Prf6X. Zhu和Y. 戴工程科学与技术,国际期刊41(2023)1013833DCDC¼DFDFOODFvðhÞxr2F¼2O 2---::油O:2 -ð -Þ-ð-Þð -ÞFp¼2/Robsrh¼4lxRobarccos1-h-vUy=d0:142 2Ro=公司简介油O2不其中r表示距圆心的径向距离(平面齿轮)。Ro是最大径向距离,即面齿轮的外半径。则剪应力分布S_r_h为其中U(U=xRo)表示通过面齿轮表面的进油流速。y是与齿轮。表面摩擦系数fL:如[18,19]:“的。!#srlR油O @DC¼-下午0:578时30分ð9Þð12Þ直流油@r r r2然后将该剪应力乘以润湿表面积Sp在前/后表面的阻力和相应的损失是确定为:为了得到面齿轮侧面上的阻力Fp,如下:F我们的服务ppF1qU2fLR2“p反正弦1h-h。1h-rh-。第二章第三章第四章第五章第六章第七章第八章第七章第当径向距离接近最大值时,即,r=Ro,则Sp2/Rob. f是平面齿轮的浸入角,表示为f/4arccos。1-h-从图中1.一、尺寸ss-和P0205ql05x25R4hp反正弦1 h-2013 -11 - 131h-ph-2h-i深度h被定义为面f/4的浸入深度h的比率齿轮的外半径Ro。显然,面齿轮部分地浸没在面齿轮中psinfarccos1-h-g2013 -02 - 21即,06h-61,与图1所示的相同。1.一、关于湍流,速度分布vT因此,根据普朗特七分之一幂定律[47],阻力和侧面的相应损失:[18][19][.联系我们DC油10 -200067. m油1=71=7U和表面摩擦系数fT:Pp¼ 4升油bx2R2cos-1h1 -h-i10 -3000上午10时02分油 =.UdTi0:167152.1.1. 前/后表面根据Seetharaman等人[18,19],因此,面上的对应搅动损失被获得为:描述搅拌面前/后表面的搅拌功率损失1qU2fTR2“p-arcsin。1-h-n-。1-h-r-h-r-h-r-h-r-h-r-h。ffiffiffi2ffiffiffiffi-ffiffiffiffihffi-ffiffiΣffiffiffi#齿轮是建造的。阻力和速度分布取决于层流或湍流状态,这可以通过雷诺数来判断(对于层流,Re¼q油xR2=l油5×104;对于湍流,f2油o 22016-11 - 01o5和Re1/4油xR2=l油>5×10)。对于齿面上的层流,速度分布为:线性处理0:0125qoil ll l0:14x2:86R4:72hp-arcsin1-h--1-h-phhhcf-零点十四分DFvLLU y=.3:46p2moilRo=U11fsin ½arccos1-h]g2016 -02 - 16HRoORo2L其中,m油(m油1/4l油1=q油1)是油的运动粘度。所以10 -1000油--油ð14ÞX. Zhu和Y. 戴工程科学与技术,国际期刊41(2023)1013834图1.一、部分浸入油浴中的面齿轮的特性参数X. Zhu和Y. 戴工程科学与技术,国际期刊41(2023)1013835rirr/·¼×·Rr Rp2*CRoDc博2.2. 齿部功率损失当面齿轮部分或全部浸没在油槽中时,由于齿轮旋转的作用,润滑油将在齿隙中旋转并形成涡流,并伴有搅动损失Prf。齿轮的轮齿形状是沿半径方向变化的,很难得到一种有效而简单的方法来直接计算。考虑到齿轮的啮合原理,用直齿面齿轮插齿刀的齿距代替复杂的正交面齿轮来估算该功率损失Prf油腔中的油流被视为蠕动流[19],则:Pfs¼nl油 xhcri-rr2rirr。k3-k4线17线其中n是浸没在油槽中的齿的平均数量hc表示穿过空腔的角度(图2)的情况。 ri(r r≤ ri≤ ro)是蠕动流的外半径。根据上述条件确定k1、k2、k3和k4k1k2r2k3logrk4r2 logr< $0 atr<$rrjhj6hc orr¼ri jh j6hcð18Þ和D.k1k2r2k3logrk4r2 logrk. -xr rat r¼r rjhj6hc图三. 临时测试台架的架构。博士-xr iat r <$r ijhj6hc(394 mm 266 mm 100 mm)由有机玻璃制成,3. 实验和分析3.1. 试验台ð19Þ检查平面齿轮周围的油流量(图 4)。Gradu-静态油位的刻度附在油槽的壁上。对于所有试验,阻力矩达到稳定状态,阻力矩的最大相对偏差为5%,然后记录转速和扭矩值。为了进行正交面齿轮的搅拌试验,建立了专用试验台,该专用试验台由变频器Transformer组成,变频器控制高速电机驱动轴和面齿轮,最高转速可达12,000 r/min(图3)。采用精度为± 0.001Nm的动态扭矩传感器直接测量扭矩,以确定搅拌功率损失。具体地说,主要由轴承阻力扭矩产生的附件功率损失是从不存在油的齿轮系统的基线测试中通过实验获得的,然后从飞溅润滑面齿轮系统的总扭矩中减去以确定净搅动贡献,还使用相同的方法分离出风阻贡献。 平 行六面体油底壳图二. 齿P fs处功率损失的参数定义[19]。3.2. 实验结果本文所提供的实验数据是通过利用由9400树脂制成的3D打印面齿轮测量的,其主要参数列于表1中。面齿轮逆时针旋转高达3500 r/min,以防止shud的干扰来自悬臂梁结构的震动。齿轮部分浸入46液压油(q油= 760 kg/m3,l油= 0.06134Pas,通过原位测试测量)中,0:2;0:3;0:4;0:5和25 °C(q空气= 1.169 kg/m3,l空气= 1.8410- 5 Pa s)。关于面由于没有经验公式或分析模型来预测风阻扭矩,因此首先利用相同的试验台,通过使用第3.1节中的方法来量化面齿轮在没有润滑的情况下的风阻扭矩(图3)。 5)。阻力矩曲线与直齿、斜齿和弧齿锥齿轮相似,随转速的变化服从抛物线率定律(Twx2),呈现然后使用特设测试台来测量搅拌用同样的方法计算飞溅润滑下的平面齿轮扭矩(图6)。如图所示,搅拌扭矩随着转速和无量纲浸没深度的增加而增加。搅拌转矩与转速的关系不符合抛物线规律(Tc/x2)。在换句话说,无量纲搅动扭矩Ccm不是常数并且随旋转速度和浸入深度而变化,并且不同于无量纲搅动扭矩Cwm(取决于几何参数的常数)。在某种程度上,面齿轮可以看作是一种特殊的螺旋锥齿轮。Quiban等人[17]报告了一个实验观察的幻影,即飞溅润滑螺旋锥齿轮的负载相关功率损失首先在X. Zhu和Y. 戴工程科学与技术,国际期刊41(2023)1013836hRohRoh见图4。 特设测试台的照片。表1面齿轮数据的几何数据。可变值齿数51模块2.5毫米压力角25°内径128 mm外径164毫米图五. 风力扭矩随转速的变化。低速,然后在中速(约2500 r/ min)下降低,他们的先驱工作引入了动态浸入深度来解释这种现象,而不是静态浸入深度。根据这一概念,在飞溅润滑下,面齿轮的油位被认为达到了稳定状态,由高速摄像机捕捉,以定性地表示动态浸入深度,如图所示。7.第一次会议。结合Quiban见图6。 搅拌扭矩随转速的变化规律。i. 低油位(h/Ro= 0.2)下的无油表面比高油位(h/Ro= 0.4)下的无油表面更均匀、更稳定,特别是在ng1020 r/min、h/Ro= 0.2(左侧液面接近静止)的情况下。随着转速和无因次深度的增加,液面的晃动更加剧烈。在低油位时,实时浸没深度即动态浸没深度约为初始静态浸没深度,而实时浸没深度小于静态浸没深度。ii. 在高转速和高深度下,旋转面齿轮正面和右侧的搅拌油滴和油膜的数量和粒径越来越大。在低浸入深度时,齿轮箱前壁比高油位时更清晰。在高油位的情况下,面齿轮左侧出现了一些油滴,甚至在前透明板上形成了一层油层。3.3. 解析关系首先,对低速(约1000 r/min)运转的面齿轮的X. Zhu和Y. 戴工程科学与技术,国际期刊41(2023)1013837图7.第一次会议。面齿轮搅拌行为照片:(a)ng= 1020 r/min,h/Ro= 0.2;(b)ng= 1000 r/min,h/Ro= 0.4;(c)ng= 2010 r/min,h/Ro= 0.2;(d)ng= 2000 r/min,h/Ro= 0.4;(e)ng= 3025 r/min,h/Ro= 0.2;(f)ng= 3000 r/min,h/Ro= 0.4。min)与实验扭矩进行了比较,如图8所示。结果表明,除油浸深度为0.5(油浸深度越大,油气比越大)外,理论值与实验值同时指出,面齿轮在低速时的搅动行为趋向于锥形,不必考虑风阻行为。同 时 , 本 文 还讨 论 了 经 验 或 半 经验 公 式 ( Terekhov 等 [10];Lauster等[11]; Boness等[12])的结果。[12]; Laruelle等人。[13])和第2节中提出的搅动功率损耗分析模型叠加在图中。 9与实验值进行比较。如图所示,Terekhov等[10]、Lauster等[11]、Boness等[12]的经验或半经验公式和实验结果远多于Laruelle等[13]和引入的搅动损失模型。结果表明,适用于直齿轮的经验模型不再适用于面齿轮,而适用于弧齿锥齿轮的预测方法则适用于面齿轮。为提高预报精度,结合试验观测和动态浸水深度假设,提出了考虑浸水深度演变和风振贡献影响的解析模型为了结合搅动(Pch)和风阻(Pwi)分布,作为油液润湿面积Sm的函数的总负载无关功率损失(Pall)可以分解为:h Rongh Rongh Rongh Rong见图8。单面齿轮搅动扭矩理论值与实验值随浸入深度的比较。图9.第九条。单面齿轮搅动功率损失(h/Ro= 0.2)的理论结果与实验数据的比较X. Zhu和Y. 戴工程科学与技术,国际期刊41(2023)1013838---p2O//Pall¼PchPwi20虽然风阻损失源于由齿泵送和排出的气流。目前,还缺乏一种理论方法来估算面齿轮的风功率损失。风损失PWi与非湿润面积S呈正相关-Sm ),即Pwi S Sm。此后,在不同的浸没深度的风阻贡献可以近似估计。Quiban et al.[17]和Dai et al.[20]中,利用半逆方法得到了动态浸没深度与弗劳德数的关系曲线动态深度将被认为是由第一恒定部分(Fr*≤25)、第二线性过渡部分(25 ≤Fr*≤50)和第三常数部分(Fr*≤50),其中Fr*(Fr ω1 ×Ro=gh,g表示重力加速度)。是无油表面流动的佛汝德数第一部分中的最大油浸深度等于静态深度(如第3.2节中的实验观察结果),第三部分中的最小油浸深度计算如下:.h-β1/4。h-β=h-7:8 8.h-β2019 - 06-2501:01:01图十一岁单面齿轮理论计算结果与实验数据的比较与负载无关的总功率损耗。现在,可以估计与动态浸入深度集成的搅动贡献和用于平面齿轮的总负载无关功率损耗评估的模型(等式(6) 图 11给出了考虑这种新的动态油浸深度模型的理论预测与实验值之间的比较。如图11所示,改进后的面齿轮解析模型的理论计算结果与实验结果相吻合。计算值与实测值的最大相对误差为31%,平均相对误差为18%。比较图9,Fig. 10和图11(与传统方法比较),改进后的理论方法所得结果更接近实验数据。此外,无论是低速还是中等转速,面齿轮的搅动行为都贡献了总的与负载无关的损失(搅动损失和风阻损失之和)的90%以上,如图所示。 12个。在低速时,风阻损失小得可以忽略不根据发展-基于动态浸没深度的理论模型,图。图13还显示了面齿轮的侧面和前/后面处的搅动损失,齿P rf处的功率损失几乎对总搅动损失或总负载无关损失没有贡献。因此,图中未列出。 13岁显然,前/后表面的功率损失远远大于侧面的功率损失,特别是在较高的速度下。具体地说,平面齿轮齿面上的功率损失与齿轮宽度和半径的平方成正比,即P p- bR o,符合公式(10-根据等式(13-2),表面上的功率损失与半径的四次方成比例,即PfR 4.外半径超过齿轮宽度的四倍,因此齿面上的功率损失远低于端面上的功率 与Fig. 12、搅动损失主要来自前/后端面,而风阻损失主要来自齿面(风阻效应不容忽视,特别是在中速或高速时)。这也表明,在中速时面齿轮搅动功率损失的预测需要考虑搅动现象和风阻行为。图10个。单面齿轮理论计算结果与实验数据的比较h Rongh Rongh Rongh Rong搅拌功率损失(h/Ro= 0.3)。见图12。 与负载无关的损耗分布。h Roh Roh Roh Roh Roh RohDynDynstatX. Zhu和Y. 戴工程科学与技术,国际期刊41(2023)1013839确认该研究由中国国防部初步研究项目资助,资助号为KY-44-2018-0219。引用h Rongh Rongh Rongh Rong[1] G.F.希思,R. R。陈志荣,工业齿轮传动技术之发展,国立成功大学机械工程研究所硕士论文,2002年。[2] R.R. 填料,G.F.南卡罗来纳州希思Slaughter等人, 同心面齿轮传动的扭矩分配,美国直升机学会第58届年会,论坛(2002)。[3] G.F.希思体育会Slaughter D. J. Fisher等人,根据增强型旋翼机驱动系统计划开发螺旋面齿轮,第67届年度论坛和技术展示(论坛67)2011(AHS 2011[4] T.T. Petry-Johnson,P. Johnson,A. Kaharan,N.E. Anderson,D.R.蔡志华,正齿轮传 动 效 率 的 实 验 研 究 , 机 械 工 程 学 报 。 130 ( 6 ) ( 2008 ) ,https://doi.org/10.1115/1.2898876。[5] V.V. 许国忠,准双曲面齿轮加工中齿轮油润滑特性的研究,硕士Theory 44(5)(2009)923https://doi.org/[6] V.V. Simon,减少齿面不对中对弹性流体动力润滑的影响的面滚切螺旋锥齿轮的最佳齿修形,J.Mech.Des.136(7)(2014),https://doi.org/10.1115/1.4026264071007。[7] V.V. Simon,通过优化制造参数改进准双曲面齿轮的混合弹性流体动力润滑,磨损438(2019),https://doi。图十三. 各部分的搅动损失贡献与无量纲深度的关系。4. 结论为了准确预测正交面齿轮在油池中部分浸没运行时的总功率损失,提出了一种考虑搅动和风阻影响的采用动态浸没深度和静态浸没深度的在飞溅润滑试验台上直接测量了一个面齿轮的实验值,验证了阻力矩模型的可以得出一些结论:(1) 在低转速下(即,Frω6 25)。还注意到,理论扭矩比实验扭矩中等转速下的数据(即,FrωP 25)。(2) 实验结果表明,当转速超过2000 r/min时,风阻的贡献虽较小,但不可忽略。还观察到,实时油浸深度是动态的,不等于静态深度。因此,改进了分析模型,采用动态浸入深度代替静态浸入深度,可以在中等转速下(即, ngP2000 r= min;FrωP 25)。(3) 该理论模型能以最小的计算量准确地定量计算转速、流体性质和面齿轮特性对飞溅润滑条件下面齿轮的搅动损失的影响。然而,通过建立与面齿轮特性相关的更精确和可靠的动态浸入深度模型以及该模型在低静态浸入深度或高转速下的适用性,正在进行进一步的工作以提高搅动损失模型的准确性。竞争利益作者声明,他们没有已知的竞争性财务利益或个人关系,可能会影响本文报告的工作。org/10.1016/j.wear.2019.01.053。[8] H.有泽湾西村湾今井Goi CFD Simulation for Reduction of Oil Turbning Loss andWindage Loss on Aeroengine Transmission Gears Proc of ASME Turbo Expo No.GT 2009 -59226 2009年6月美国奥兰多10. 1115/gt 2009 - 59226.[9] S.松本湾浅锅湾高野湾高速齿轮功率损失的Yamamoto评估方法,日本润滑工程师学会摩擦学会议,1985年7月,日本东京,1165 - 1170。[10] A.S.张文,齿轮箱油浸时的液压损失,北京:机械工业出版社,2000。55(5)(1975)7-11。[11] E. Lauster , M. Boos , Zum Wärmehaushalt mechanischer SchaltgetriebefürNutzfahrzeuge,VDI-Berichte 488(1983)45-55.[12] R. J. Boness,部分浸没在水中运行的盘和齿轮的搅动损失美国机械工程师协会国际动力传动和齿轮传动会议论文集。Chicago,1(1989)355-359.[13] C. Changenet,P. Velex,齿轮传动中搅动损失的预测模型-初步结果,J. Mech. Des。129(2007)128doi.org/10.1115/1.2403727[14] C. Changenet,G.Leprince,F.Ville等人, 关于流态和搅动损失建模的说明,J.Mech. Des. 133(12)(2011),https://doi.org/10.1115/1.4005330121009。[15] S.拉吕埃勒角福西耶角Changenet,F.维尔,S. Koechlin,飞溅润滑螺旋锥齿轮搅 动 损 失 的 实 验 研 究 和 分 析 , 机 械 工 业 18 ( 4 ) ( 2017 ) 412 ,https://doi.org/10.1051/meca/2017007。[16] C. 福西耶角Changenet,D.Barday等人,驱动桥热行为的研究:功率损失和热传递估算,SAE国际。 J. 引擎11(1)(2018)55 https://doi.org/10.4271/03-11-01-0004。[17] R.基班角Changenet,Y. Marchesse,F.王文,高转速下螺旋锥齿轮的搅动损失,机械 工 程 学 报 , J 部 分 : J.Tribol 工 程 师 234 ( 2 ) ( 2020 )172https://doi.org/10.1177/1350650119858236[18] S. Seetharaman,A.Kahlovan,正齿轮副的与载荷无关的旋转功率损失:模型制定,J.Tribol。131(2)(2009),https://doi.org/10.1115/1.3085943022201。[19] S. Seetharaman,A. Kaharan,M. Moorhead,T. Petry-Johnson,齿轮副的油搅动功率 损 失 : 实 验 和 模 型 验 证 , J. Tribol 。 131 ( 2 ) ( 2009 ) 022202 。 doi :0.1115/1.3085942。[20] Y. Dai,F.妈,X。Zhu,B.欧阳,螺旋锥齿轮搅动功率损失分析模型的开发,Tribol。Int.151(2020),https://doi.org/10.1016/j.triboint.2020.106536106536.[21] M. Pandey,B.N.帕迪岛Mishra,I,夜间使用的废热回收太阳能烟囱的性能分析,工程科学。技术人员:Int.J.24(1)(2021)1https://doi.org/10.1016/j.jestch.2020.11.009[22] M. Das,E. 阿列什,E.K. 张文龙,太阳能干燥系统干燥过程中传热传质的数值模拟与实验研究,北京:机械工程出版社。技术人员:J. 24(1)(2021)236https://doi.org/10.1016/-246,www.example.com j.jestch.2020.10.003。[23] M. Bakirc,S. Yılmaz,水平轴风力涡轮机最佳叶尖速比的理论和计算研究,工程科学。技术人员:Int.J. 21(6)(2018)1128https://doi.org/10.1016/j.jestch.2018.05.006[24] A. Turner,H.P.莫尔万湾Simmons,使用颗粒注入和壁膜模型的螺旋锥齿轮的两相CFD建模,在:Turbo Expo:陆地、海洋和空中的动力,美国机械工程师协会,2013年,第55270页,https://doi.org/10.1115/GT2013-94735。[25] T. Fondelli,A.安德烈伊尼河Da Soghe等人,高速齿轮油喷射润滑的数值模拟,国 际 航 空 航 天 杂 志 。 Eng.2015 ( 2015 ) , https : //doi.org/10.1155/2015/752457。[26] Y. Dai,F.妈,X。Zhu等人,正交面齿轮传动喷油润滑性能的评估和优化:建模、仿真和X. Zhu和Y. 戴工程科学与技术,国际期刊41(2023)10138310实 验 验 证 , 能 源 12 ( 10 ) ( 2019 ) 1935 , https://doi.org/10.3390/en12101935。[27] 诉 Chernoray , M. 杨 文 , 多 相 流 在 齿 轮 箱 模 型 中 的 实 验 研 究 70 ( 2011 )153https://doi.org/10.2495/[28] A.诺伊鲁思角Changenet,F. Ville,M. Octrue,E. Tinguy,高速齿轮飞溅润滑的实验研究,J.Tribol。139(6)(2017),https://doi.org/10.1115/1.4036447061104。[29] L.M. Yao,Z.M. Xiao,J.B.刘,智-地Zhang,M.王,流体-颗粒耦合动力学分析的一种优化的CFD-DEM方法,Int.J.Mech.Sci.174(2020),https://doi.org/10.1016/j.ijmecsci.2020.105503105503.[30] A.S. Kolekar,A.V. Olver,A.E. Sworski,F.E. Lockwood,Windage and churningeffects in dipped lubrication , J. Tribol. 136 ( 2 ) ( 2014 ) 0221801 ,https://doi.org/10.1115/1.4025992。[31] C. Changenet,P. Velex,齿轮传动中壳体对搅动损失的影响,J. Mech. Des。130(6)(2008),https://doi.org/10.1115/1.2900714062603。[32] H. Liu,G. Arfaoui,M.斯坦尼克湖Montigny,T. Jurkschat,T. Lohner,K.张文,齿轮箱油液分布和搅拌齿轮功率损失的数值模拟,机械工程学报,J部分:J.Eng. Tribol. 233(1)(2019)74https://doi.org/10.1177/[33] H. Liu,T. Jurkschat,T. Lohner,K. Stahl,通过有限体积CFD方法确定齿轮箱的油分布和搅动功率损失,Tribol。Int.109(2017)346https://doi.org/10.1016/j.triboint.2016.12.042[34] F.康诺利角Gorla,齿轮传动中功率损失的数值建模:采用新的集成方法进行风阻 、 搅 动 和 气 穴 模 拟 , 大 大 减 少 了 计 算 工 作 量 , Tribol。 Int.103 ( 2016 )58https://doi.org/10.1016/j.triboint.2016.06.046[35] F.康诺利角郭伟,工业行星减速器中搅拌功率损失的计算和实验分析,WIT Trans.Eng. Sci. 74(2012)287https://doi.org/10.2495/AFM120261[36] F. Conventional,C,Gorla C,行星齿轮箱中搅动功率损耗的数值建模:一种基于分区的创新啮合方法,用于将计算工作量减少策略应用于复杂齿轮箱配置,Lubr。Sci. 29(7)(2017)455https://doi.org/[37] F.康诺利角Gorla,齿轮箱中功率损失和润滑剂流动的CFD模拟,在:美国齿轮制造商协会秋季技术会议,(2017年10月)2-14。https://doi.org/10.2495/MPF110131的网站。[38] F. Consideration,Low-loss gears precision planetary gearbox:reduction ofthe load dependent power losses and efficiency estimation through a hybridanalytical- numerical optimization tool,Forschung im Ingenieurwesen Eng.Res. 81(4)(2017)395https://doi.org/10.1007/s10010-017-0242-0[39] M. N. Mastrone , F. Consideration , Numerical modeling of fluid's aeration :analysis of the power losses and lubricant distribution in gearboxes , J. Appl.Comput. Mech.9(1)(2023)83-94. https://doi.org/10.22055/jacm.2022.40666.3625的网站。[40] J. Li,X.钱氏C. Liu,不同移动网格策略用于研究齿轮箱内油流的比较研究,Int. J.Numer. Meth. Heat Fluid Flow 32(11)(2022)3504https://doi.org/10.1108/HFF-10-2021-0695[41] H. Arisawa,M. Nishimura,H. Imai等人,减少航空发动机传动齿轮中的油搅动损失和风阻损失的计算流体动力学模拟和实验,J. Eng. Gas Turbines Power136(9)(2014),https://doi.org/10.1115/1.4026952。[42] Q.彭湖,澳-地Gui,Z. Fan等人,准双曲面齿轮箱中飞溅油流的数值和实验研究。Fluid Mech.12(1)(2018)324https://doi.org/10.1115/1.4026952[43] X. Hu,Y.江角,澳-地Luo等人,螺旋锥
下载后可阅读完整内容,剩余1页未读,立即下载
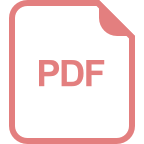
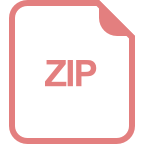
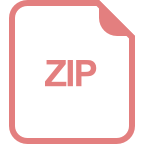
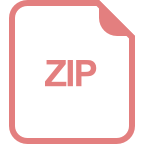
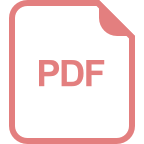
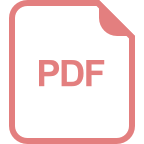
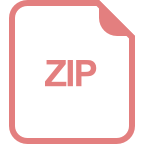
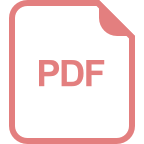
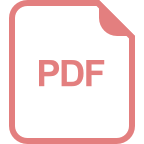
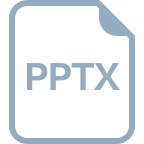
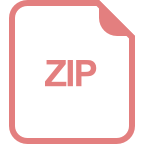
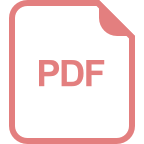
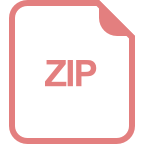
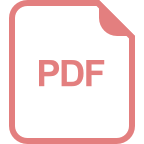
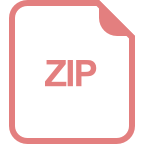
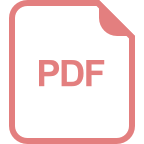
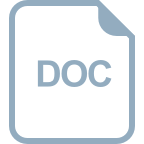
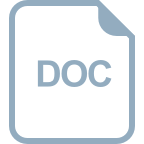

cpongm
- 粉丝: 5
- 资源: 2万+
上传资源 快速赚钱
我的内容管理 展开
我的资源 快来上传第一个资源
我的收益
登录查看自己的收益我的积分 登录查看自己的积分
我的C币 登录后查看C币余额
我的收藏
我的下载
下载帮助

最新资源
- Aspose资源包:转PDF无水印学习工具
- Go语言控制台输入输出操作教程
- 红外遥控报警器原理及应用详解下载
- 控制卷筒纸侧面位置的先进装置技术解析
- 易语言加解密例程源码详解与实践
- SpringMVC客户管理系统:Hibernate与Bootstrap集成实践
- 深入理解JavaScript Set与WeakSet的使用
- 深入解析接收存储及发送装置的广播技术方法
- zyString模块1.0源码公开-易语言编程利器
- Android记分板UI设计:SimpleScoreboard的简洁与高效
- 量子网格列设置存储组件:开源解决方案
- 全面技术源码合集:CcVita Php Check v1.1
- 中军创易语言抢购软件:付款功能解析
- Python手动实现图像滤波教程
- MATLAB源代码实现基于DFT的量子传输分析
- 开源程序Hukoch.exe:简化食谱管理与导入功能
资源上传下载、课程学习等过程中有任何疑问或建议,欢迎提出宝贵意见哦~我们会及时处理!
点击此处反馈


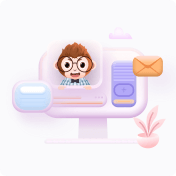
安全验证
文档复制为VIP权益,开通VIP直接复制
