The liquid inflow represents starch that is being heated from a temperature of 30°C to 60°C. The change in temperature of the starch was observed to be 20°C under this change. Plot the response of a system having the deadtime and time constant determined above to ensure that your transfer function represents the experimental data well. The dead time and time constant for the process with respect to changes in the inlet temperature of the starch were determined separately and found to be 35 s and 25 s. Write the complete process transfer function(s) for the outlet temperature. A proportional controller is used with a gain (Kc) of 0.05 and 0.2. Demonstrate the response to the feed temperature change of 10°C and show how the controller acts to control the temperature. Find the proportional offset in each case.
时间: 2024-03-25 19:39:47 浏览: 81
To plot the response of a system that represents the experimental data well, we first need to determine the transfer function of the system.
The dead time and time constant for the process with respect to changes in the inlet temperature of the starch are given as 35 s and 25 s respectively. This suggests that the process can be modeled as a first-order plus dead time (FOPDT) system.
The transfer function for a FOPDT system is given by:
G(s) = K * exp(-Ls) / (Ts + 1)
where:
K = process gain
L = dead time
T = time constant
Substituting the given values, we get:
G(s) = K * exp(-35s) / (25s + 1)
To find the complete process transfer function for the outlet temperature, we need to add a controller to the above transfer function. The transfer function for a proportional controller with gain Kc is:
C(s) = Kc
The overall transfer function for the closed-loop system is given by:
H(s) = G(s) * C(s) / (1 + G(s) * C(s))
Substituting the values of G(s) and Kc, we get:
H(s) = 0.05 * exp(-35s) / (25s + 1 + 0.05 * exp(-35s))
or
H(s) = 0.2 * exp(-35s) / (25s + 1 + 0.2 * exp(-35s))
To demonstrate the response to the feed temperature change of 10°C, we can use the step function as the input. The Laplace transform of a step function with magnitude A and time delay L is:
F(s) = A * exp(-Ls) / s
Substituting A = 10°C and L = 0 (since the step function starts at t = 0), we get:
F(s) = 10 / s
The output temperature response can be found by multiplying the input and transfer function in the Laplace domain:
Y(s) = H(s) * F(s)
Taking the inverse Laplace transform of Y(s) using partial fraction decomposition, we get the time-domain response of the system.
The proportional offset can be found as the steady-state error between the setpoint (desired temperature) and the process output at steady-state. It can be calculated as:
Offset = (Setpoint - Steady-state output) / Setpoint
The response of the system can be plotted using Matlab's step function. The code for the first case (Kc = 0.05) would look like:
```
Kc = 0.05;
G = tf(0.05*[1], [25 1], 'InputDelay', 35);
C = tf([Kc], [1]);
H = feedback(G*C, 1);
F = tf([10], [1 0]);
Y = H*F;
step(Y);
```
The code for the second case (Kc = 0.2) would look like:
```
Kc = 0.2;
G = tf(0.05*[1], [25 1], 'InputDelay', 35);
C = tf([Kc], [1]);
H = feedback(G*C, 1);
F = tf([10], [1 0]);
Y = H*F;
step(Y);
```
The proportional offset can be calculated by finding the steady-state output of the system using Matlab's stepinfo function:
```
stepinfo(Y)
```
This will give the steady-state output, rise time, settling time, and other performance parameters of the system.
阅读全文
相关推荐
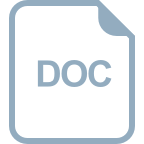
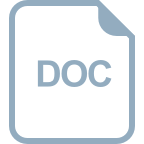
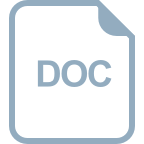
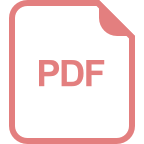

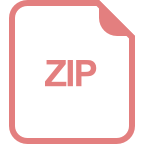
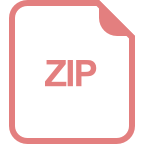
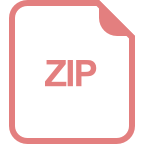
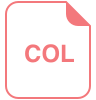
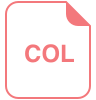
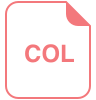




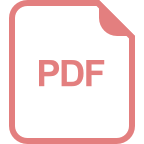
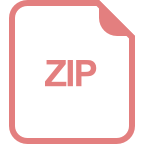
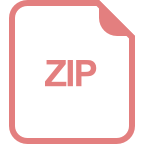
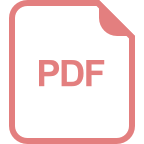