翻译The complex 3D geometries of these submillimeter-scale robots originate from planar (2D) multilayer assemblies formed with deposition and patterning techniques used in the semiconductor industry. Figure 1 (A and B) illustrates the process of transformation that converts these 2D precursors into 3D shapes for the case of a design inspired by the geometry of a peekytoe crab (Cancer irroratus) but engineered to a much smaller dimensions (~1/150 of the actual size; fig. S1). The precursors incorporate layers of SMA (nitinol; 2.5 m in thickness) as a collection of dynamic mechanical joints for locomotion, a film of polyimide (PI; ~8 m in thickness) as a static skeleton for structural support, and pads of silicon dioxide (SiO2; 100 nm in thickness) as bonding sites in the 2D to 3D transformation process (left frames in Fig. 1, A and B). This process begins with transfer printing to deliver these 2D precursors onto the surface of a prestretched silicone elastomer (Dragon Skin 10 Slow, ~500 m in thickness) that supports structures of polydimethylsiloxane (PDMS; blocks) located near the claws and back legs (middle frame in Fig. 1B). Releasing the prestrain imposes compressive stresses at the bonding sites, with forces sufficient to convert the 2D structures into 3D architectures via a set of controlled bending/ twisting deformations and translational/rotational motions (31, 32). During this process, the distance between the two PDMS blocks also decreases, thereby deforming the claws and back legs. This transformation involves peak strains (<4%) that lie below the maximum phase transition strain of the SMA (right frame in Fig. 1B).
时间: 2024-03-30 10:34:48 浏览: 158
这些亚毫米级机器人的复杂三维几何形状源于半导体工业中使用的沉积和图案化技术形成的平面(二维)多层组装。图1(A和B)说明了转化过程,将这些二维前体转化为三维形状,以一个以peekytoe蟹(Cancer irroratus)几何形状为灵感设计但缩小了许多尺寸(约为实际尺寸的1/150;图S1)为例。前体包括SMA(nitinol;厚度为2.5μm)层作为一组用于运动的动态机械连接件、聚酰亚胺(PI;厚度约为8μm)薄膜作为静态骨架用于结构支撑,并且二氧化硅(SiO2;厚度为100nm)垫片作为2D到3D转化过程中的粘合位点(图1A和B中的左侧框架)。该过程始于转移印刷,将这些二维前体传递到预拉伸的硅弹性体(Dragon Skin 10 Slow,厚度约为500μm)表面上,该弹性体支撑着位于爪和后腿附近的聚二甲基硅氧烷(PDMS;块)结构(图1B中间框架)。释放预应力在粘合位点处施加压缩应力,其力量足以通过一组受控的弯曲/扭曲变形和平移/旋转运动将二维结构转化为三维结构(31, 32)。在此过程中,两个PDMS块之间的距离也会减小,从而使爪和后腿变形。这种转化涉及峰值应变(<4%),低于SMA的最大相变应变(图1B中的右框架)。
相关问题
翻译This SiO2 shell is a key component in the mechanism for reversible actuation, as illustrated by finite element analysis (FEA) in Fig. 1C. An increase in temperature transforms the SMA (nitinol) from the martensitic to the austenitic phase, causing the 3D structure to flatten into a 2D shape. The responses of the SMA elements at the joints act as driving forces to deform the PI skeleton. This process also elastically deforms the SiO2 shell, resulting in a counter force that limits the magnitude of the deformation. The change in shape ceases when the forces from the shell balance those from the joints (right frame in Fig. 1C). Upon a reduction in temperature, the SMA changes from the austenitic back to the martensitic phase, thereby reducing the force produced by the SMA at the joints to zero. The elastic forces associated with the shell then push the entire system back to the original 3D geometry (left frame in Fig. 1C). Figure S3A simulates the moments generated by the SMA and the SiO2 shell. In the FEA model, the SiO2 shell appears on both the outer and inner surfaces of the 3D robot, consistent with experiments (fig. S3B). Although a single layer of the SiO2 shell at the outer or inner surface can also provide restoring force, the double-layer shell structure follows naturally from the conformal deposition process. This actuation scheme allows for reversible shape transformations using a one-way shape memory material. Without the shell, the structure only supports a single change in shape, from 3D to 2D, as illustrated in fig. S3C. Figure 1D shows optical images of a freestanding 3D peekytoe crab on the edge of a coin, highlighting the preserved 3D geometry enabled by the SiO2 shell after release from the elastomer substrate. Other 3D structures in geometries that resemble baskets, circular helices, and double-floor helices also exhibit high shape storage ratios (>85%) after cycles of heating and cooling (fig. S4). This ratio (s) is defined as s = 1 − |L1 − L0|/L0 × 100%, where L0 and L1 are the distances between the bonding sites at both ends at the initial stage and subsequent stages, respectively
这个SiO2壳是可逆作用机制的关键组成部分,如图1C所示的有限元分析所示。温度的升高将SMA(尼钛)从马氏体相转变为奥氏体相,导致3D结构变成2D形状。连接处SMA元件的响应作为变形PI骨架的驱动力。这个过程也会弹性变形SiO2壳,产生抵消变形幅度的对抗力。当壳体受力平衡连接处的力时,形状的变化停止(图1C右侧)。温度降低时,SMA从奥氏体相变回马氏体相,因此连接处由SMA产生的力减少到零。与壳体相关的弹性力将整个系统推回原始的3D几何形状(图1C左侧)。图S3A模拟了SMA和SiO2壳体产生的力矩。在有限元分析模型中,SiO2壳体出现在3D机器人的外表面和内表面,与实验结果一致(图S3B)。虽然在外表面或内表面只有一个SiO2壳层也可以提供恢复力,但双层壳体结构自然地遵循共形沉积过程。这种作用机制使用单向形状记忆材料实现可逆形状转换。没有壳体,结构只支持从3D到2D的单次形状变化,如图S3C所示。图1D显示了一只自由站立的3D Peekytoe蟹在硬币边缘的光学图像,突出了SiO2壳在从弹性体基底释放后保留的3D几何形状。几何形状类似于篮子、圆螺旋和双层螺旋的其他3D结构在加热和冷却循环后也表现出高形状存储比率(>85%)(图S4)。这个比率(εs)定义为εs = 1-|L1-L0|/L0×100%,其中L0和L1分别是初始阶段和随后阶段两端结合点之间的距离。
After the range processing and static clutter removal steps, the Capon beamformer based on the steering vectors over a fine 1D azimuth grid (i.e., zero-elevation) is applied to generate the 2D rangeazimuth spectrum matrix (i.e., heatmap). In the Capon beamformer, the azimuth-only transceiver pairs (TX-RX) are utilized to estimate the covariance matrix across the received chirps per range bin. The details about the antenna geometries of the radar boards are given in Section 3.3.1.翻译一下
在经过距离处理和静态杂波去除步骤后,利用在细致的1D方位网格上的定向向量(即零仰角)的基于Capon的波束成形器被应用于生成2D范围-方位谱矩阵(即热图)。在Capon波束成形器中,仅使用方位发射机-接收机(TX-RX)对来估计每个范围距离峰值处的接收到的啁啾信号的协方差矩阵。有关雷达板天线几何的详细信息请参见第3.3.1节。
阅读全文
相关推荐
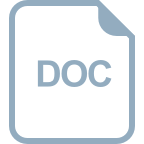
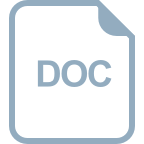
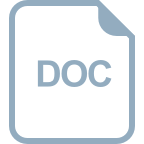
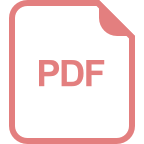
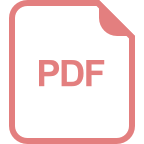
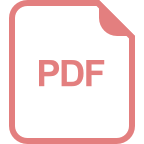
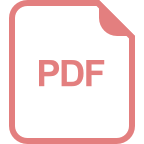
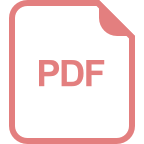
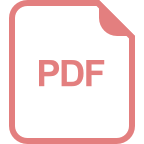
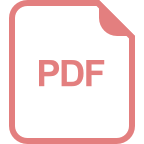
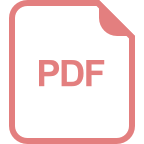
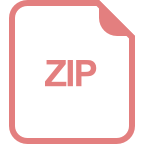
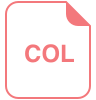
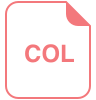


