【动态检查的高级功能】:CATIA中形位公差的动态检查技术
发布时间: 2024-12-21 12:14:28 阅读量: 13 订阅数: 11 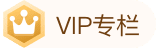
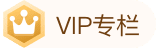
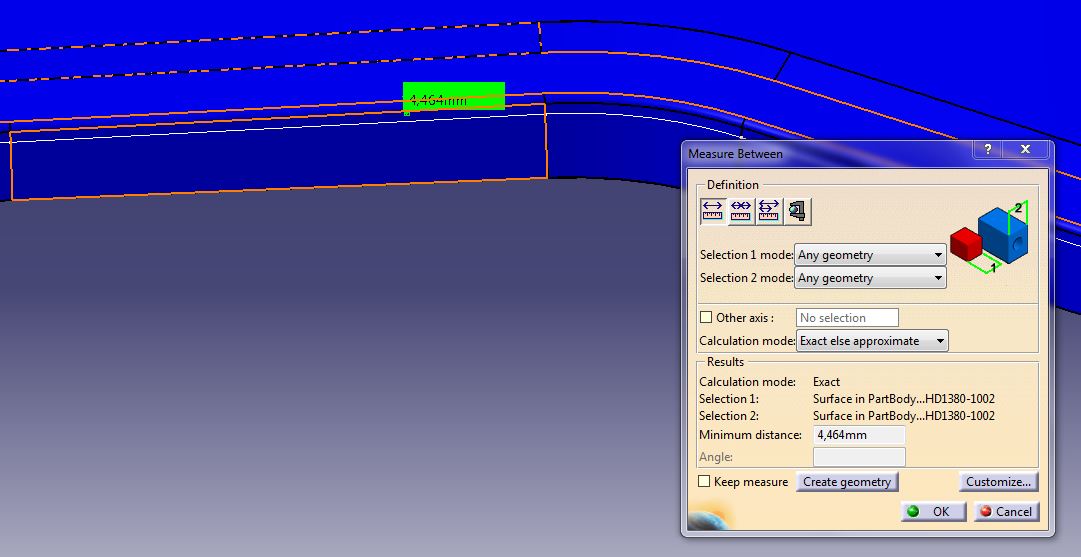
# 摘要
形位公差是现代机械设计和制造中的关键质量控制参数,其准确度直接影响产品的性能和寿命。本文首先介绍了形位公差的基本概念和重要性,随后深入探讨了在CATIA软件中实现的形位公差动态检查技术,包括其理论基础、功能操作和应用案例分析。进而,文章阐述了形位公差动态检查的高级功能实现,如自适应检查技术原理和智能化反馈机制设计,以及相应的操作技巧和实战演练。在数据管理方面,本文分析了数据存储、调用、分析以及质量控制策略,并探讨了数据驱动设计优化的影响和策略。最后,文章展望了形位公差动态检查技术的未来趋势,包括新兴技术的影响、智能化与自动化的发展方向,以及持续学习与技术更新的必要性。通过最佳实践与案例研究,本文旨在为行业内提供可借鉴的成功经验和实践效果评估。
# 关键字
形位公差;动态检查;数据管理;质量控制;智能化反馈;设计优化
参考资源链接:[CATIA V5 形位公差标注教程:参照图解](https://wenku.csdn.net/doc/5p3t5f4st9?spm=1055.2635.3001.10343)
# 1. 形位公差的基本概念与重要性
## 形位公差的基本概念
形位公差是指在产品的制造过程中,对产品零件的形状和位置的精度要求进行规定的一种技术标准。它涵盖了产品的尺寸、形状、方向、位置和跳动等五个方面的公差。形位公差是现代制造业产品质量控制的关键,它确保了产品的几何精度,满足了设计要求。
## 形位公差的重要性
在机械制造行业,形位公差控制是保证产品质量的核心环节。精确的形位公差确保零件之间的正确配合,有助于提升设备的运行效率和可靠性。忽视形位公差可能会导致设备故障频繁,增加维护成本,甚至造成安全事故。因此,深入理解形位公差的基本概念及其重要性,对于制造出高质量的机械产品至关重要。
# 2. ```
# 第二章:CATIA中的形位公差动态检查技术
## 2.1 动态检查技术的理论基础
### 2.1.1 形位公差的定义和分类
形位公差是确定零件几何形状和位置精度的一项重要指标,其反映了加工精度、装配关系和功能要求。在机械设计和制造中,形位公差被分为尺寸公差和几何公差两大类。
尺寸公差控制零件的实际尺寸与设计尺寸间的偏差,是基于长度、角度等标量量度的公差。相对地,几何公差关注的是形状、方向、位置以及轮廓的变异。几何公差包括平面度、圆度、圆柱度、同轴度、位置度、对称度等分类。
### 2.1.2 动态检查技术的工作原理
动态检查技术是一种在三维模型环境中实时分析和评估形位公差的方法。它利用计算机辅助设计软件(如CATIA)进行模拟,并提供即时反馈,从而在产品设计阶段就能发现可能存在的问题。
在CATIA中,动态检查技术通过模拟不同的条件和装配关系来检查零件的公差配合。这种技术不仅能够评估公差本身,而且可以分析公差累积效应和公差敏感性。通过这种技术,工程师能够更加直观地理解设计的可制造性,及时调整设计以优化产品质量。
## 2.2 动态检查技术的功能与操作
### 2.2.1 动态检查的主要功能
动态检查技术的主要功能包括:
- **公差分析**:对零件的形位公差进行分析,判断是否符合设计要求。
- **动态模拟**:在不同工况下动态模拟产品,查看关键部位的形位变化。
- **优化建议**:基于分析结果提出设计和制造的优化建议。
- **数据记录**:记录检查过程中的关键数据,便于后续分析和管理。
### 2.2.2 动态检查的操作流程
在CATIA软件中,进行动态检查的操作流程如下:
1. **加载模型**:首先,在CATIA中打开要检查的3D模型。
2. **设置公差**:在模型中定义形位公差的参数。
3. **运行检查**:执行动态检查命令,软件将模拟零件的装配过程,并实时显示公差数据。
4. **结果解读**:根据动态检查的输出结果,解读零件是否满足公差要求。
## 2.3 动态检查技术的应用案例分析
### 2.3.1 实际工程案例
在某大型机械制造企业的实际工程案例中,使用CATIA软件的动态检查技术对汽车发动机缸体的装配公差进行了全面分析。通过模拟发动机工作时的热膨胀和负荷影响,成功地评估了缸体与活塞之间的公差配合情况。
### 2.3.2 动态检查结果的解读
在该案例中,动态检查结果显示,缸体在高温和高负荷条件下的形位变化超出了预定公差范围。根据这些结果,工程师对缸体结构进行了优化,以保证在各种工作条件下都能满足公差要求,从而提高了发动机的可靠性和寿命。
```
在本节中,我们介绍了形位公差的基本概念和重要性,并深入探讨了CATIA中的动态检查技术。下一部分我们将继续深入了解如何实现高级功能,以及如何在实际应用中操作和解析动态检查结果。
# 3. 形位公差动态检查的高级功能实现
## 3.1 高级功能的技术原理
### 3.1.1 自适应检查的实现原理
在现代制造行业,形位公差的动态检查已经不再局限于基本的几何元素校验,而是朝着能够适应不同复杂情况的自适应检查方向发展。自适应检查技术是利用先进的算法和丰富的经验知识库,自动识别零件的特征和公差要求,无需用户提前设定详尽的检查方案。
自适应检查的实现原理依赖于复杂的数学模型和计算机视觉技术。它能根据零件的三维模型数据,自动识别出需要检查的特征,并匹配相应的公差标准,从而实现实时的、动态的检查。例如,自适应检查能够在检测到一个孔特征时,自动应用圆度公差规则,并且根据孔的直径自动确定公差带的宽度。
### 3.1.2 智能化反馈机制的设计
智能化反馈机制是动态检查技术中的另一个高级功能。这一机制能够自动地根据检查结果提供反馈,这些反馈不仅包括简单的合格与否判断,还包括对加工过程中潜在问题的预警和改进建议。
这一机制的设计基于数据分析和机器学习技术。通过收集大量的历史检查数据,系统可以学习到特定类型零件在加工中可能出现的偏差模式,并在实时检查过程中,将这些模式与当前检查结果进行比对。一旦检测到偏离正常模式的行为,系统即刻提供反馈,帮助工程师或操作员在问题变得严重之前进行干预。
## 3.2 高级功能的操作技巧
### 3.2.1 参数设置与调整
实现高级功能的关键之一在于正确的参数设置。动态检查技术中的参数设置通常包括公差限值、检查区域、检查密度等。对于自适应检查而言,参数设置需要更加灵活,以便在不同的检查情况下提供最佳的检查效率和精度。
在调整这些参数时,工程师需要依据零件的加工精度要求和所使用的检测设备的性能。例如,在检查一个精密齿轮时,可能需要设置较高的检查密度以确保齿轮的齿形精度;而在检查大型零件时,则可能更关注检查速度和结果的概览,因此会降低检查密度。
### 3.2.2 问题诊断与解决方法
自适应检查和智能化反馈机制虽然强大,但在实际操作中也可能遇到一些问题。例如,在自适应检查中,系统可能会因为零件的缺陷而无法准确地识别出特征,或者智能化反馈给出的建议与实际操作情况不符。
问题诊断是解决这些问题的第一步。通常需要工程师结合实际的检查结果和零件状态,使用系统提供的日志文件和问题诊断工具进行排查。当发现问题所在后,可以通过调整检查参数或更新知识库的方式来解决问题。必要时,也可以手动干预检查过程,采用更细致的检查方案。
## 3.3 高级功能的实
0
0
相关推荐
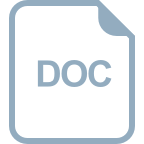
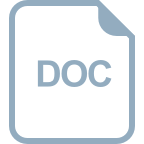
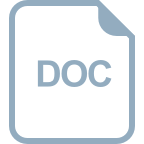
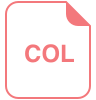
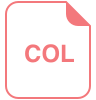
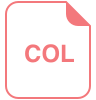
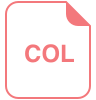
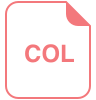
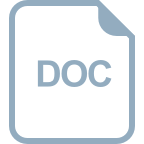