DEFORM-2D与CAD_CAE软件协同工作:实现无缝数据集成
发布时间: 2025-01-08 14:30:05 阅读量: 9 订阅数: 14 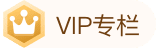
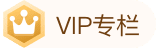
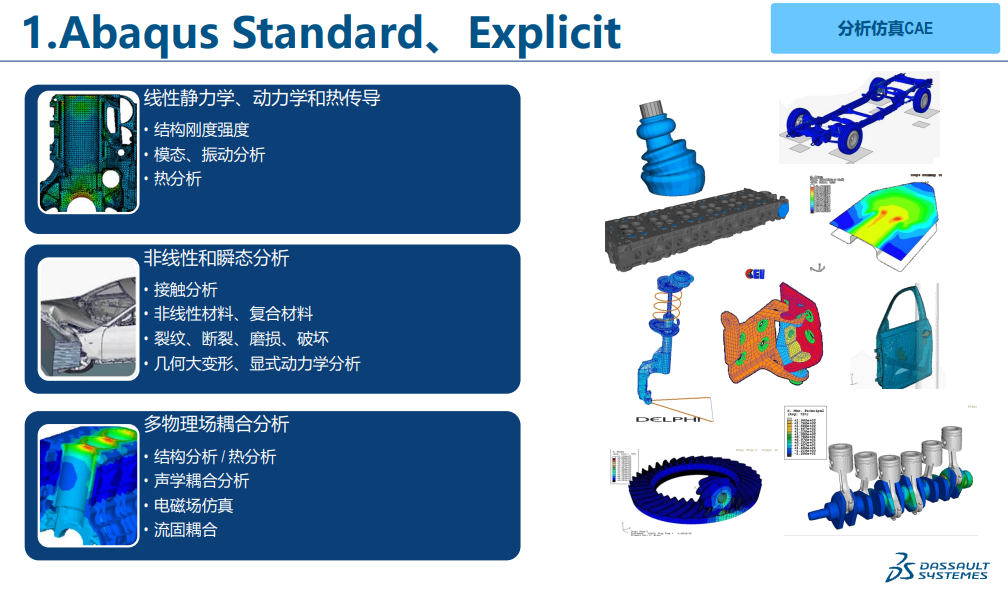
# 摘要
DEFORM-2D作为一款集成CAD与CAE功能的软件,在工业设计与分析中扮演着重要角色。本文介绍了DEFORM-2D的基本功能、CAD与CAE软件的工作原理以及数据交换标准。同时,探讨了DEFORM-2D与相关软件的协同机制,以及在模具设计、金属成形过程和工艺优化方面的应用案例。通过对软件使用和工业应用的深入分析,本文提供了数据管理和错误处理的最佳实践,并对CAD/CAE集成技术的未来趋势和技术创新方向进行了展望,指出了推动协同工作的潜在技术障碍和相应的解决方案。
# 关键字
DEFORM-2D;CAD;CAE;数据集成;协同机制;工艺优化
参考资源链接:[DEFORM-2D初学者操作指南:从创建问题到设置模拟控制](https://wenku.csdn.net/doc/5x99ybaao0?spm=1055.2635.3001.10343)
# 1. DEFORM-2D软件简介与功能概述
在现代制造工业中,精确的仿真分析对于产品开发和工艺优化至关重要。DEFORM-2D软件作为一种强大的计算机辅助工程(CAE)工具,专注于2D塑性成型过程的模拟,已成为工程师进行材料加工分析不可或缺的一部分。它不仅能进行热力耦合分析,还能模拟各种金属加工过程,如锻造、冲压和热处理等。
## 1.1 DEFORM-2D的核心优势
DEFORM-2D的主要优势在于其直观的用户界面和先进的计算算法,这两者共同提供了一个容易操作且高效的仿真环境。软件允许用户自定义材料属性、边界条件和网格细化,以精确模拟复杂的物理过程。它支持多个物理场耦合,例如温度场、应变场和应力场,为实现真实世界过程的精准模拟打下基础。
## 1.2 功能模块简介
软件中的不同功能模块,如模拟、材料数据库、后处理工具等,被设计来协同工作,以简化从模型设定到分析结果评估的整个过程。工程师可以利用这些模块进行前处理设置,执行模拟,并在后处理中对结果进行详细分析,如应力分布、变形历史以及温度变化等。通过这些分析,可以预测材料流动、材料损伤和产品最终质量。
接下来的文章章节将进一步深入探讨CAD与CAE的基本原理,以及DEFORM-2D软件在工业应用中的实际案例和未来的技术发展趋势。
# 2. CAD与CAE软件的基本原理
## 2.1 CAD软件的核心功能和操作流程
### 2.1.1 CAD软件的界面和工具介绍
CAD(Computer-Aided Design)软件作为设计与工程领域的基石,以其强大的绘图、建模、仿真和分析能力,为产品开发的各个环节提供支持。CAD软件的界面通常包括工作区、工具栏、命令窗口、属性编辑器以及状态栏等多个组成部分。在这些区域中,用户可以找到用于执行各种任务的工具和选项。
以主流的CAD软件Autodesk AutoCAD为例,其用户界面通常被分为以下几个部分:
- **快速访问工具栏**:包含常用命令,如新建、打开、保存、撤销、重做等。
- **功能区**:显示了不同功能的面板,包括绘图、修改、图层管理、注释和输出等。
- **绘图区域**:这是设计进行的地方,用户可以通过不同的工具和命令在这一区域绘制图形。
- **命令窗口**:用于输入命令和显示程序输出信息,对于习惯了命令行操作的用户来说尤为重要。
- **状态栏**:显示当前的状态信息,如图层、捕捉、网格等。
- **面板和工具栏**:提供具体工具的访问点,如尺寸标注、绘图和编辑等。
### 2.1.2 CAD建模的基本步骤和技巧
CAD建模是一个将创意和技术细节结合的过程。以下是进行CAD建模的基本步骤:
1. **需求分析**:理解设计需求,明确建模的目的和标准。
2. **草图绘制**:利用CAD软件提供的绘图工具创建2D草图,勾画出设计的基本轮廓。
3. **尺寸标注和约束**:给草图添加必要的尺寸和几何约束,确保模型的准确性和可修改性。
4. **3D建模**:通过拉伸、旋转、扫描或放样等方法,将2D草图转化为3D模型。
5. **细节处理**:添加细节特征,如倒角、圆角、孔和纹理等。
6. **装配设计**:如果有多个零件,需要进行装配设计,确保零件之间的相互关系和配合。
7. **分析与优化**:进行结构强度、动态分析等,优化设计并减少潜在问题。
8. **出图**:生成用于制造和生产的工程图纸,包括正视图、侧视图、剖视图等。
在操作过程中,用户应该注意以下技巧:
- **使用参数化设计**:参数化设计允许用户通过修改尺寸来快速改变模型形状,提高设计效率。
- **图层管理**:合理使用图层可以帮助管理复杂模型的多个组件,便于维护和修改。
- **模块化设计**:将复杂模型分解为可复用的模块或子组件,便于管理和调整。
- **利用历史记录**:在需要的情况下,可以回溯或修改之前的建模步骤。
- **模型验证**:在设计的每个阶段都应进行模型验证,确保设计符合预期目标和功能需求。
通过上述步骤和技巧的运用,CAD用户可以有效地完成从概念到详细设计的转化过程,为后续的CAE分析和制造环节奠定坚实基础。
## 2.2 CAE软件的分析类型与工作流程
### 2.2.1 CAE软件的常见分析类型
CAE(Computer-Aided Engineering)软件能够对产品或工程结构进行有限元分析(FEA)、计算流体动力学(CFD)、多体动力学(MBD)、热力学分析、疲劳分析等。这些分析类型是评估设计性能、优化设计和减少实验成本的重要手段。
以下是CAE软件常见的分析类型及其应用场景:
- **有限元分析(FEA)**:用于评估产品在受到各种力(如压力、冲击、振动)作用下的应力、应变和位移等。FEA广泛应用于结构完整性评估。
- **计算流体动力学(CFD)**:分析流体流动及其与固体的相互作用,例如在气动、热交换和流体控制中的应用。
- **多体动力学(MBD)**:模拟机械系统中各个组件的运动和力的传递,适用于复杂的机电系统。
- **热力学分析**:评估热流动、热传递以及温度分布对产品性能的影响,如在发动机设计和电子散热中的应用。
- **疲劳分析**:评估产品在长期循环载荷下出现疲劳破坏的风险,用于预测产品的使用寿命。
### 2.2.2 CAE分析流程和关键环节
CAE分析流程通常包括以下几个关键环节:
1. **问题定义**:确定分析的目的、范围和条件。
2. **几何模型准备**:利用CAD软件提供的模型导入CAE工具,或者直接在CAE软件中创建模型。
3. **材料定义和属性分配**:为模型指定合适的材料属性,如弹性模量、屈服强度、热传导系数等。
4. **网格划分**:将模型划分为有限元网格,为后续的计算和分析做准备。
5. **边界条件和载荷施加**:定义模型的约束、支撑、受力和其他相关载荷。
6. **求解**:运行分析求解器,对模型进行数值计算。
7. **结果处理**:分析计算结果,并以图表、云图、动画等形式展示。
8. **设计优化**:根据分析结果对设计方案进行必
0
0
相关推荐








