数控机床性能调优实战:案例分析与优化技巧
发布时间: 2024-11-29 22:13:34 阅读量: 65 订阅数: 23 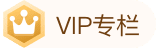
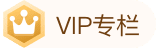
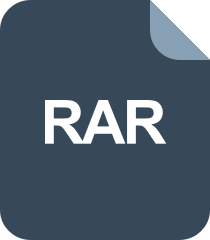
036GraphTheory(图论) matlab代码.rar
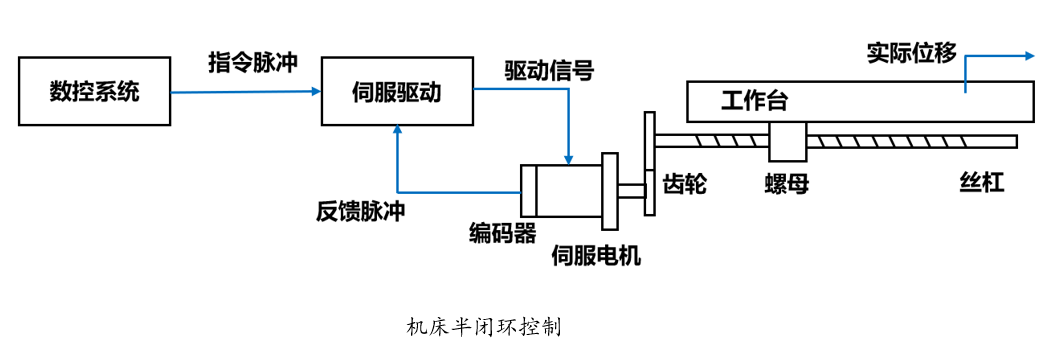
参考资源链接:[宝元数控系统操作与编程手册](https://wenku.csdn.net/doc/52g0s1dmof?spm=1055.2635.3001.10343)
# 1. 数控机床性能调优概述
在现代制造业中,数控机床是推动生产自动化与高精度制造的关键力量。随着产品定制化和市场需求多样化的发展,对数控机床性能的要求也在不断提升。性能调优作为提高数控机床工作效率、延长使用寿命的重要手段,是制造业技术人员必须掌握的核心技能。本章将概述数控机床性能调优的基本概念、目的和重要性,为后续章节详细介绍具体的调优方法和案例分析打下基础。我们将探讨性能调优的必要性,以及它在提升加工精度、加工效率和机床稳定性方面的重要作用。此外,本章还将简要介绍影响数控机床性能的几大关键因素,为读者在后续章节中进行更深入的学习和实践提供理论基础。
# 2. 数控机床的理论基础
## 2.1 数控机床的工作原理
数控机床的工作原理是将数字信息转换为机械运动和加工动作的过程。在数控机床的整个生命周期内,了解其工作原理对于保证机床的稳定运行和加工质量至关重要。
### 2.1.1 CNC系统的结构和功能
CNC(Computer Numerical Control)系统是数控机床的核心部分,它由硬件和软件两大部分组成。硬件包括输入/输出设备、存储器、CPU、伺服驱动器、位置检测器等;软件则是数控机床运行的指令集,包括数控代码解释、插补算法、速度控制等程序。
**CNC系统的核心功能有:**
- **程序执行:** CNC系统读取用户通过G代码、M代码等编写的程序,并将其转换为机床动作。
- **运动控制:** 系统通过伺服电机驱动机床各轴按照预定路径移动。
- **实时监控:** CNC系统实时监测机床状态,包括位置、速度和温度等。
- **故障诊断:** 在检测到异常时,CNC系统能快速定位问题并采取相应措施。
### 2.1.2 常见数控机床类型及特点
数控机床按照加工方式和结构可以分为多种类型,每种类型有其特定的应用领域和特点。
**如:**
- **数控铣床:** 能够进行铣、钻、攻丝等多面加工,适用于复杂形状零件的加工。
- **数控车床:** 主要用于旋转类零件的车削加工。
- **加工中心:** 结合了铣床和车床的功能,可以进行更复杂的加工任务。
### 2.2 性能评估指标
为了全面评估数控机床的性能,需要从多个维度进行考量,其中精度、效率和稳定性是三大核心评估指标。
#### 2.2.1 精度与误差分析
精度是衡量数控机床加工质量的重要指标。机床的精度受多种因素影响,包括温度、振动、刀具磨损等。
**精度的分类包括:**
- **静态精度:** 指机床在静止状态下各坐标轴的定位精度。
- **动态精度:** 指机床在高速运行和加工时的定位精度和重复定位精度。
**误差分析通常包含:**
- **系统误差:** 来自机床结构、装配和检测系统本身的误差。
- **随机误差:** 包括环境变化、材料性能波动等造成的随机误差。
#### 2.2.2 加工效率和稳定性
加工效率直接关系到生产成本和交货期,而加工稳定性是保证连续加工和产品质量一致性的基础。
**加工效率的提升方法包括:**
- **提高切削速度:** 减少非切削时间,如加速和减速过程。
- **优化刀具路径:** 减少不必要的运动,提高路径效率。
- **刀具寿命管理:** 合理选择和更换刀具以保证生产效率。
**加工稳定性的保障措施包括:**
- **良好的机床维护:** 定期检查和更换易损件,如导轨、滚珠丝杆、轴承等。
- **合理的工艺参数设定:** 如切削深度、进给速度和转速的合理选择。
### 2.3 性能调优的理论支撑
性能调优的理论基础主要涉及材料去除率理论和动态特性对加工性能的影响。
#### 2.3.1 材料去除率理论
材料去除率(MRR)是指单位时间内从工件上移除的材料体积。在不损伤机床和刀具的前提下,尽可能提高MRR是提升加工效率的关键。
**影响MRR的因素包括:**
- **切削参数:** 切削深度、进给速度、转速等。
- **刀具材料和几何参数:** 刀具材料的硬度、韧性和刃口形状。
**提高MRR的策略通常包括:**
- **优化刀具选择:** 选择适合材料和加工任务的刀具。
- **切削参数调整:** 根据材料性质和机床能力调整切削参数。
#### 2.3.2 动态特性对加工性能的影响
机床的动态特性描述了在受到力的作用时,机床各部分的响应特性。动态特性包括机床的刚性、阻尼、抗振性等。
**动态特性的不良影响包括:**
- **加工表面质量下降:** 由于振动引起的振纹。
- **刀具寿命缩短:** 振动增加刀具负担。
**提高动态性能的方法有:**
- **提高机床结构刚性:** 如通过改进机床结构设计,使用高刚性材料等。
- **优化阻尼特性:** 如通过添加阻尼器或采用阻尼材料。
- **控制加工参数:** 通过软件调整,优化切削参数以减少振动。
### 小结
通过深入探讨数控机床的工作原理和性能评估指标,我们可以更好地理解其理论基础。在后续章节中,我们将探讨如何将这些理论应用到实际的数控机床调优实践中,并通过具体案例来进一步阐明这些概念。
# 3. 数控机床的调优实践
在深入了解了数控机床的基本工作原理、性能评估指标以及相关理论支撑之后,本章将探讨具体的数控机床调优实践。首先从硬件
0
0
相关推荐




