【数控系统效能模拟】:仿真技术在数控系统中的应用,优化生产流程
发布时间: 2024-12-21 01:25:04 阅读量: 6 订阅数: 12 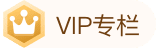
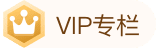
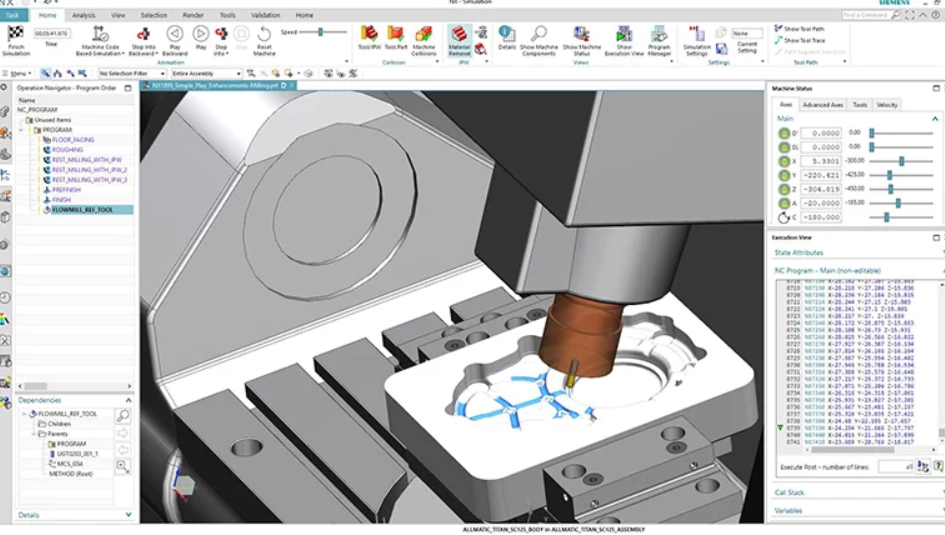
# 摘要
数控系统效能模拟是现代制造技术中至关重要的环节,仿真技术在其中扮演了核心角色。本文首先概述了数控系统效能模拟的基本概念及其在仿真技术应用中的重要性。接着,深入探讨了仿真技术在数控系统中的应用,包括仿真模型的构建、数控编程的验证以及碰撞检测和路径优化等方面,并展示了仿真技术在提升数控系统性能和生产流程优化中的实践案例。随后,文章分析了优化生产流程的仿真策略,重点讨论了生产流程分析、参数测试、优化策略制定和仿真实验设计等关键步骤。在高级应用方面,讨论了多轴数控系统的仿真优化、智能制造与仿真技术的融合,以及仿真技术的发展趋势。最后,通过案例研究,强调了仿真技术在数控系统效能模拟中的实际成效,并展望了未来的研究方向和行业发展趋势。
# 关键字
数控系统;效能模拟;仿真技术;生产流程优化;智能制造;多轴仿真优化
参考资源链接:[新代科技SYNTEC数控系统应用手册](https://wenku.csdn.net/doc/3k9rvpgac2?spm=1055.2635.3001.10343)
# 1. 数控系统效能模拟概述
## 1.1 数控系统效能模拟的重要性
随着制造业向高精度、高效率方向的持续演进,数控(Numerical Control,NC)系统成为现代工业生产不可或缺的核心技术。数控系统效能模拟为提升数控机床的性能和生产流程的优化提供了有力工具。通过效能模拟,可以在实际生产前预知可能出现的问题并进行优化,从而减少材料和时间的浪费,确保生产的连续性和产品的质量。
## 1.2 数控系统效能模拟的定义
数控系统效能模拟是在计算机环境中对数控机床及其加工过程进行的虚拟仿真。它模拟机床的工作状态、加工过程以及可能发生的各种情况,如刀具路径、材料去除率、机床热变形等,从而对数控编程进行验证和优化。通过这种方式,技术人员能够在不耗费物理资源和时间的情况下,评估和提升数控系统的整体性能。
## 1.3 数控系统效能模拟的应用价值
在实际应用中,数控系统效能模拟可以显著提高生产效率,降低生产成本,并减少故障发生的概率。模拟技术还可以帮助工程师在设计阶段进行优化,减少机床的物理测试次数,节省开发时间。此外,随着仿真技术的不断进步,它在提升产品质量、优化生产流程以及支持智能制造等方面发挥着越来越重要的作用。
# 2. 仿真技术在数控系统中的应用
## 2.1 仿真技术的理论基础
### 2.1.1 仿真的定义与分类
仿真是利用计算机模型来模拟现实世界中各种系统的行为或过程。它可以用于预测在各种条件下的系统行为,从而在实际操作前进行风险评估和性能优化。仿真的主要分类可以按不同的标准来划分,如按照模拟过程的性质可分为离散事件仿真和连续仿真。离散事件仿真关注系统中事件发生的时间点和顺序,而连续仿真则关注系统状态随时间的变化。
### 2.1.2 数控系统中仿真的作用
在数控系统中,仿真技术有以下几个关键作用:
- **风险评估:**通过仿真可以预测操作中可能出现的问题,从而避免在实际加工过程中产生昂贵的损失。
- **性能验证:**在生产之前对数控程序进行仿真验证,确保代码的正确性,减少机床空闲时间。
- **操作员培训:**提供一个安全的环境,让操作员在没有实际影响机器和材料的情况下练习和学习。
## 2.2 数控系统仿真模型的构建
### 2.2.1 数控机床模型的建立
数控机床模型的建立是进行有效仿真的前提。一个精确的机床模型需要包含机床的所有关键组件,如刀具、工作台、控制系统等。通过三维建模软件,如AutoCAD或SolidWorks,可以创建机床的几何模型。然后,需要集成数控系统的动态特性,包括轴的运动、加速度、速度等参数。
```mermaid
graph LR
A[开始建模] --> B[定义机床组件]
B --> C[三维建模]
C --> D[集成动态特性]
D --> E[进行仿真验证]
```
### 2.2.2 加工过程的模拟与仿真
在仿真模型中,加工过程的模拟需要遵循实际加工中刀具与工件之间的相互作用。仿真的关键在于动态仿真,它模拟了切削过程中的物理力和热效应。这需要利用切削力模型、热传导模型等来预测加工状态,并且调整参数来优化加工条件。
## 2.3 仿真技术与数控编程
### 2.3.1 数控编程的仿真验证
数控编程的仿真验证是一个不可缺少的步骤,它包括对刀具路径、加工策略、以及夹具和工件位置的检查。使用仿真软件,比如MasterCAM或FANUC RoboGuide,可以执行数控代码,并展示可能的碰撞和错误,确保在实际加工前优化程序。
```mermaid
graph LR
A[开始仿真验证] --> B[加载数控程序]
B --> C[选择仿真模型]
C --> D[运行仿真]
D --> E[分析结果]
E --> F[修改代码或模型]
F --> G[重新仿真直至验证成功]
```
### 2.3.2 碰撞检测与路径优化
碰撞检测是确保设备安全和避免生产损失的关键步骤。仿真技术可以检测在加工过程中可能出现的刀具与工件或机床组件的碰撞。通过仿真,可以在碰撞发生之前调整刀具路径,实现加工路径的最优规划,减少加工时间和材料浪费。
## 2.4 仿真在数控系统中的实践应用案例
### 2.4.1 实例分析:使用仿真技术改进数控系统
实际案例分析可以展示仿真技术是如何应用在数控系统中以实现效率和安全的提升。以下是一个分析示例:
**案例背景:**在使用数控铣床进行复杂部件的加工时,操作员发现机床运行不稳,存在刀具断裂的风险。
**仿真应用:**引入仿真技术进行加工过程模拟,通过动态仿真检测到在特定区域刀具负荷过重,存在碰撞风险。
**优化措施:**调整切削参数,优化刀具路径,增加切削液的使用,从而减少了刀具负荷并避免了碰撞。
**效果评估:**通过模拟和实际加工比较,发现在优化后不但避免了刀具断裂的问题,而且整体加工时间缩短了10%,废品率下降了15%。
### 2.4.2 成功案例:仿真技术在生产流程优化中的应用
在制造业中,仿真技术被广泛应用于生产流程的优化。以下是一个生产流程优化的成功案例:
**案例背景:**一条汽车零件生产线的加工周期过长,导致生产效率低下。
**仿真应用:**利用
0
0
相关推荐
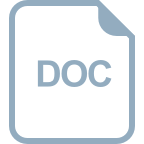
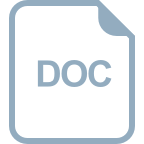
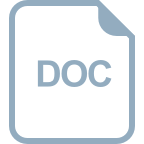
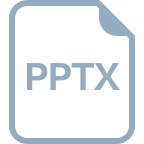
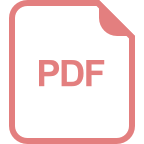
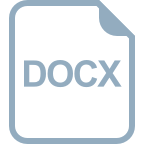
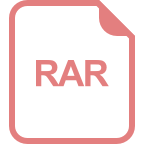
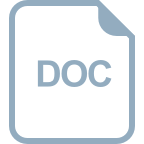
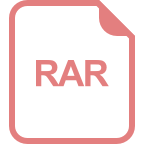