三菱PLC到松下伺服通信配置全攻略:快速搭建稳定连接
发布时间: 2024-12-18 17:42:54 阅读量: 7 订阅数: 16 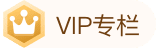
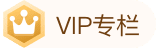
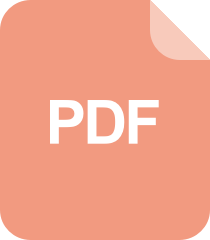
三菱PLC与松下伺服接线图


# 摘要
本文全面介绍了PLC与伺服驱动之间的通信配置方法,重点探讨了三菱PLC和松下伺服驱动的通信接口、协议解析以及参数设置。通过分析硬件连接方案、软件配置和高级连接功能的应用,本文提供了构建稳定通信连接的详细步骤和实践案例。同时,本文也展望了进阶优化方法和远程控制技术在未来的发展趋势,为工业自动化领域中通信技术的应用和维护提供了宝贵的参考和指导。
# 关键字
PLC;伺服驱动;通信配置;三菱;松下;IIoT;通信协议
参考资源链接:[三菱PLC与松下伺服接线图](https://wenku.csdn.net/doc/6412b79ebe7fbd1778d4af0f?spm=1055.2635.3001.10343)
# 1. PLC与伺服通信基础概述
在现代工业自动化领域中,可编程逻辑控制器(PLC)与伺服电机之间的通信是确保精确控制与高效率生产的关键。本章将为您介绍PLC与伺服通信的基本概念、通信架构及其重要性,为深入探讨具体品牌和技术细节打下坚实基础。
## 1.1 通信协议和接口基础
通信协议是通信双方共同遵守的规则和约定,它规定了数据的格式、传输速率以及如何在不同设备间建立连接等问题。PLC与伺服的通信协议通常包括CANopen、Modbus和各制造商的专有协议。接口则是实现物理层连接的硬件组件,常见的包括RS-422、RS-485以及以太网等。
## 1.2 PLC与伺服通信的作用
在自动化控制系统中,PLC作为控制中心,通过与伺服电机的通信,能够实现对运动控制的精确执行。伺服电机则通过反馈系统将执行状态回传给PLC,形成闭环控制系统,这在高精度定位、速度控制及扭矩控制等场景中尤为重要。
## 1.3 构建稳定通信的挑战
在实际应用中,构建PLC与伺服之间的稳定通信面临多重挑战,包括干扰、数据丢失、实时性要求等。实现高质量的通信,需要考虑硬件选择、电缆布线、接口匹配以及协议配置等多方面因素。本系列文章将逐步深入探讨这些挑战,并提供解决策略。
# 2. 三菱PLC通信接口与协议解析
## 2.1 三菱PLC通信接口种类
### 2.1.1 RS-232/422/485接口特点
RS-232、RS-422和RS-485是常用的串行通信接口,它们在电气特性、数据传输速率、传输距离和通信方式上有所不同,适用于不同的工业控制场景。
**RS-232接口**是最早期的串行通信标准,采用单端信号传输,传输距离较短,一般不超过15米。它通常用于PLC与计算机或HMI的人机交互。
**RS-422接口**为差分信号传输,提供更高的传输速率和更长的传输距离,最高可达1200米。它更适合在噪声环境下使用,确保数据的稳定传输。
**RS-485接口**与RS-422类似,也是差分信号,但支持多点通信,即一个主机可以与多个从机进行通信。RS-485广泛应用于PLC与传感器、执行器等设备间的通信。
下面的表格展示了三种接口的对比:
| 特性 | RS-232 | RS-422 | RS-485 |
|------------|--------------|--------------|---------------|
| 传输模式 | 单端 | 差分 | 差分 |
| 最大传输速率 | 20kbps | 10Mbps | 10Mbps |
| 最大传输距离 | 约15米 | 约1200米 | 约1200米 |
| 点对点/多点 | 点对点 | 点对点 | 支持多点 |
| 抗干扰能力 | 较弱 | 较强 | 强 |
| 应用场景 | 短距离、低速 | 高速、中远距离 | 高速、中远距离、多机通信 |
### 2.1.2 以太网通信接口及其特性
以太网(Ethernet)接口是基于IEEE 802.3标准的局域网技术,广泛应用于工业以太网通信。它具有高数据传输速率和良好的扩展性,支持多种协议,如TCP/IP、Profinet、EtherCAT等。
以太网接口允许PLC直接连接到局域网或互联网,实现远程监控、数据交换和设备间的高速通信。在现代工业自动化中,以太网通信已成为主流。
由于以太网允许全双工通信,数据可以在两个方向同时进行传输,极大地提高了通信效率。此外,以太网的扩展性使其可以轻松地集成到现有的IT基础设施中。
## 2.2 三菱PLC常用通信协议
### 2.2.1 CC-Link协议基础
CC-Link是由三菱电机主导开发的一个开放式现场网络技术标准。它广泛应用于工厂自动化和过程自动化领域,提供高速、可靠的网络通信。
CC-Link支持多种数据传输速率,并可以根据通信距离自动调整。它支持令牌传递和轮询两种通信方式,保证了网络通信的稳定性和实时性。
### 2.2.2 MC协议详解
MC(MELSEC Communication Protocol)协议是三菱PLC专有的通信协议,提供了一个标准化的通信框架,使得不同的PLC和外围设备能够互相通信。
MC协议支持多点数据交换和网络数据存储,极大地提高了通信效率。它也支持多种通信网络,如CC-Link、Ethernet/IP等。
### 2.2.3 用户自定义协议的配置方法
用户自定义协议允许开发者根据自己的需求创建个性化的通信协议。三菱PLC通过高级编程软件提供了创建和配置用户自定义协议的接口。
开发者可以通过编程自定义通信格式、数据打包方式和协议规则,以满足特定应用需求。这为复杂和特殊场合的通信提供了灵活性。
## 2.3 三菱PLC通信设置步骤
### 2.3.1 参数设置与地址分配
在开始通信之前,需要在PLC中设置适当的通信参数,包括波特率、数据位、停止位和校验等。地址分配是指定每个通信设备在网络中的唯一地址,这对于区分网络中的设备和正确通信至关重要。
下面的示例代码展示了如何在三菱PLC中设置串行通信参数:
```plc
// 设置串行通信参数(RS-485)
D100: 数据格式控制字,包含波特率、数据位、停止位和校验等
// 设置通信参数
MOV #0100H, D100
// 设置通信站号,用于区分网络上的不同设备
MOV #01H, D101
```
逻辑分析:
- `MOV #0100H, D100`指令用于设置串行通信的参数,其中`#0100H`是一个立即数,表示设定的参数值,比如波特率设为9600bps。
- `MOV #01H, D101`指令用于设置通信站号为1。
参数设置后,开发者需确保每个设备的地址正确分配,避免通信时的数据冲突和混乱。
### 2.3.2 通信测试与故障排除
通信测试是确保通信配置正确无误的关键步骤,它包括检查连接是否正确、确认数据是否准确传递以及诊断可能出现的通信错误。
为了进行通信测试,可以使用调试工具或软件来发送和接收数据,并对通信状态进行监控。
故障排除通常需要检查连接线路、确认设备电源和接口状态、分析错误代码等。
下面的表格提供了一些常见的通信故障及其可能的解决方法:
| 故障现象 | 可能原因 | 解决方法 |
|----------------|----------------------------------|----------------------------------------------|
| 无法通信 | 连接线故障或插头未插紧 | 检查所有连接线和接口 |
| 数据错误 | 参数设置不正确 | 重新检查并设置正确的通信参数 |
| 通信中断 | 电气干扰或设备故障 | 检查线路屏蔽、电源稳定性或更换设备 |
| 网络通信延迟 | 网络带宽不足或设备过多 | 优化网络结构,限制网络设备数量 |
| 设备无法识别 | 设备地址冲突 | 检查并重新分配设备地址 |
| 接收数据异常 | 未正确配置数据格式或帧结构 | 根据通信协议调整数据格式和帧结构设置 |
通过以上步骤,可以确保三菱PLC的通信设置正确并稳定运行。
# 3. 松下伺服驱动通信配置
## 3.1 松下伺服驱动接口选择
### 3.1.1 标准RS-422接口特性
RS-422是松下伺服驱动常用的通信接口之一,它是一种平衡传输的串行通信标准,支持多点连接,具有良好的抗干扰能力和远距离传输特性。RS-422采用差分信号传输方式,可实现最大10Mbps的数据传输速率,在最远1200米的距离上可达到100kbps的传输速率。这使得RS-422接口非常适合于工业现场设备之间的长距离高速数据通信。
在选择RS-422接口时,需要考虑以下几个特性:
- **多点通信**:RS-422允许多个接收器在单一总线上工作,这对于复杂控制系统中的多个设备间通信尤为重要。
- **信号完整性**:由于其差分信号的特点,RS-422能在嘈杂的工业环境中保持较高的信号完整性。
- **长距离传输**:RS-422设计用于长距离传输,使得控制中心与远程设备之间的连接更为方便。
### 3.1.2 高速串行接口(HSI)的优势
松下伺服驱动的高速串行接口(HSI)为用户提供了更为高效的数据交换手段。HSI接口的通信速率远高于标准RS-422接口,可以达到10Mbps或更高。HSI接口通常用于需要极高响应速度的场合,例如高精度定位控制等。
HSI接口的优势主要体现在以下方面:
- **高速数据传输**:HSI能实现更快的数据更新频率,适用于需要高速响应的应用。
- **减少延迟**:在高响应要求的系统中,HSI能有效减少控制延迟,提高系统的整体性能。
- **提高系统稳定性**:其高速性能减少了通信中可能出现的错误,从而增强了系统的稳定性。
### 表格 3.1 - 松下伺服驱动接口特性对比
| 特性 | RS-422接口 | 高速串行接口(HSI) |
| --- | --- | --- |
| 最大数据传输速率 | 10Mbps | 10Mbps+ |
| 支持通信距离 | 最远1200米 | 未明确规定,取决于特定实施细节 |
| 连接设备数量 | 多个接收器 | 取决于具体配置 |
| 抗干扰能力 | 较强 | 较强 |
| 延迟 | 较高 | 较低 |
## 3.2 松下伺服通信协议细节
### 3.2.1 Modbus RTU协议应用
Modbus RTU是工业通信领域广泛采用的一种协议,松下伺服驱动也支持Modbus RTU协议。Modbus RTU协议以二进制编码,具有传输效率高,抗干扰能力强的特点。它以主从方式工作,允许多个从设备连接到同一个通信网络上,由主机控制数据的交换。
在实现Modbus RTU通信时,需要关注以下几点:
- **数据帧格式**:Modbus RTU的数据帧以设备地址、功能码、数据和校验码构成。
- **帧间隔**:为确保通信的可靠性,Modbus RTU协议在每个数据帧之间设置了较长的帧间隔时间。
- **通信延迟**:由于其帧间隔的特点,Modbus RTU不适合对实时性要求极高的场合。
### 3.2.2 松下专有通信协议深入
松下伺服驱动也拥有自己的专有通信协议,该协议提供了更为紧密的控制方式和更丰富指令集。专有协议使用户可以更深层次地对伺服进行控制和状态监控,同时提供了参数设定、实时反馈和故障诊断等功能。
使用松下专有协议时,一些要点包括:
- **指令集**:专有协议拥有特定的指令集,用于实现控制和诊断功能。
- **参数设定**:通过专有协议可以对伺服驱动的各种参数进行详细设定。
- **实时监控**:专有协议支持实时监控伺服的状态和性能指标。
### mermaid 流程图 3.1 - 松下伺服通信协议选择
```mermaid
graph TD
A[开始通信配置]
A -->|选择通信协议| B[Modbus RTU]
A -->|选择通信协议| C[松下专有协议]
B --> D[设置通信参数]
B --> E[编写控制指令]
C --> F[定义专有指令]
C --> G[设置协议特定参数]
D --> H[通信测试]
E --> H
F --> I[通信测试]
G --> I
H --> J[故障诊断与维护]
I --> J
J --> K[通信优化]
```
## 3.3 松下伺服参数设置与调试
### 3.3.1 参数设置指导
松下伺服驱动器的参数设置是实现精确控制的关键步骤。这些参数包括但不限于速度、加减速时间、增益等。参数设置指导对于伺服驱动器的稳定运行至关重要。
参数设置的步骤通常包括:
1. **确定系统需求**:根据应用需求确定伺服驱动器的参数设置。
2. **输入参数**:通过操作面板、编程软件或通信指令设置伺服参数。
3. **验证参数**:对设置的参数进行验证,确保无误。
4. **调整优化**:根据实际运行情况对参数进行微调,优化性能。
### 3.3.2 运行监控与故障诊断
松下伺服驱动器提供了运行监控和故障诊断功能,便于用户实时监控伺服的工作状态,及时发现并处理故障。运行监控可以显示诸如速度、位置、电流等关键数据,而故障诊断则提供故障代码和相应的解决建议。
使用运行监控和故障诊断功能时,应当注意:
- **数据读取**:定期读取监控数据,分析伺服运行状况。
- **故障代码解析**:对伺服器的故障代码进行准确解读,迅速采取措施。
- **日志记录**:保持对故障事件的记录,便于后期分析和问题追踪。
### 代码块 3.1 - 参数设置与监控代码示例
```c
// 通过通信协议设置伺服参数(伪代码)
void setServoParameters(int speed, int accelerationTime, float gain) {
// 发送参数设置指令到伺服驱动器
通信指令writeToServo("SET_SPEED", speed);
通信指令writeToServo("SET_ACCEL_TIME", accelerationTime);
通信指令writeToServo("SET_GAIN", gain);
}
// 读取伺服状态信息
void readServoStatus() {
// 发送读取状态指令到伺服驱动器
String status = 通信指令readFromServo("READ_STATUS");
// 解析状态信息
String[] statusInfo = 解析通信数据(status);
// 输出状态信息
输出状态信息(statusInfo);
}
```
在上述代码块中,函数 `setServoParameters` 负责向伺服驱动器发送参数设置指令,函数 `readServoStatus` 则用于读取伺服驱动器的当前状态。在实际应用中,这两个函数需要结合具体的通信协议来实现。通信指令的编写需要参照松下伺服驱动器的通信手册,以确保格式的正确性。
通过本章节的介绍,我们深入理解了松下伺服驱动器的接口选择、通信协议细节以及参数设置与调试的重要性。了解这些内容,对于实现松下伺服驱动器与PLC等控制系统的有效集成至关重要。接下来,在第四章中,我们将探讨如何构建三菱PLC与松下伺服之间的稳定连接。
# 4. 构建三菱PLC与松下伺服稳定连接
要实现三菱PLC与松下伺服的稳定连接,需要从硬件与软件两个方面进行仔细配置。本章节将详细介绍如何通过硬件连接方案、软件配置与通信测试以及高级连接功能应用,来建立一个可靠、高效的控制系统。
## 4.1 硬件连接方案
硬件连接是整个系统稳定运行的基础。正确选择电缆、进行接线,并采取必要的电气隔离与信号保护措施是确保通信稳定的关键步骤。
### 4.1.1 电缆选择与接线图示
电缆的选择直接影响到信号的传输质量。对于三菱PLC与松下伺服的连接,通常使用屏蔽双绞线电缆。电缆应根据传输距离选择适当的规格,以避免信号衰减。
在电缆选择后,按照接线图示进行接线是确保连接正确的基础。接线图示需要详细标注每个接点的信号类型和电缆的颜色编码,以避免操作人员混淆。通常,三菱PLC的输出端口连接松下伺服的输入端口,确保对应关系正确无误。
### 4.1.2 电气隔离与信号保护
电气隔离通常采用光耦合器等元件来实现,这样可以防止电气干扰和避免设备间电位差所造成的损害。信号保护则需要使用适当类型的避雷器、浪涌保护器等元件来避免由于外部电磁干扰或电源波动导致的信号失真。
在设计电气隔离和信号保护方案时,还应考虑到系统的实际工作环境。例如,如果系统部署在电磁干扰较大的场所,那么可能需要采用更加复杂和高级的保护措施。
## 4.2 软件配置与通信测试
硬件连接完成后,接下来需要进行软件配置和通信测试。通过编写适当的通信初始化程序,可以确保数据在PLC与伺服之间正确、高效地传输。
### 4.2.1 通信初始化程序编写
在编写通信初始化程序时,首先需要配置PLC与伺服的通信参数,如波特率、数据位、停止位和奇偶校验等。此外,还需要设置正确的地址分配和通信模式,以适应不同的控制需求。
通信初始化程序的编写需要根据具体的协议和接口进行调整。以下是一个简化的示例代码,展示如何在三菱PLC中使用MC协议进行初始化配置:
```plc
// 假设使用GX Works编程软件
// 初始化程序代码块
PROGRAM MAIN
// 设置通信模式和参数
SETTING COMM_PARAM;
// 设置通信端口
SETTING COMM_PORT;
// 启动通信
START COMMUNICATION;
END_PROGRAM
```
### 4.2.2 连接稳定性测试与优化
通信连接建立之后,需要进行连接稳定性测试。测试可以通过发送特定的数据包,并监控数据是否能够准确无误地传输和接收完成。如果出现错误,需要根据错误信息进行相应的故障排除。
测试过程中,记录每次通信的成功率和错误类型是十分重要的,这些数据将用于进一步优化通信连接。例如,如果通信中断频繁发生,可能需要检查电气隔离和信号保护方案是否正确执行。
在测试阶段,还可以使用一些额外的软件工具来进行诊断和分析。这些工具能够提供更加详细的诊断报告,从而帮助工程师快速定位问题所在。
## 4.3 高级连接功能应用
为了进一步提高系统的灵活性和可靠性,可以采用一些高级连接功能。例如,实现双线备份通信模式和实时数据交换与同步控制。
### 4.3.1 双线备份通信模式
双线备份通信模式可以提高系统的通信冗余度,即使一条通信线路发生故障,另一条线路仍然可以保持通信的正常运行。这种模式在高要求的工业环境中尤其重要。
在实现双线备份时,需要确保PLC与伺服的软件支持同时进行多路通信,并且能够在主通信线路故障时,自动切换到备份线路。这样可以最大限度地减少停机时间。
### 4.3.2 实时数据交换与同步控制
在复杂的控制场景中,需要PLC与伺服驱动器之间实现实时数据交换和同步控制。这意味着系统中的设备需要按照一定的时序关系进行精确的操作。
通过编程,可以实现对伺服运动的实时监控,并根据PLC接收到的数据快速作出响应。同步控制要求PLC具备高精度的时间管理功能,以便确保所有设备能够协同工作。
实现这些高级功能通常需要对PLC和伺服的软件进行深度定制,因此在实施前需要对设备的软件功能和限制有充分的了解。
通过以上四个章节的内容,我们已经介绍了如何从基础到高级实现三菱PLC与松下伺服的稳定连接。下一章节将通过具体的实践案例,展示如何快速搭建实际应用连接。
# 5. 快速搭建实际应用连接
本章节将通过一系列具体的实践案例来展示如何快速搭建三菱PLC与松下伺服之间的稳定连接。我们将从不同应用领域选取案例,每个案例都包含系统需求分析、通信配置、维护策略等方面的内容。通过这些实践案例,读者可以直观地理解理论与实际应用之间的联系,并掌握搭建稳定通信连接的具体步骤。
## 案例一:定位控制系统的通信配置
定位控制系统是工业自动化中常见的应用之一,它要求伺服电机能够精确地按照PLC发出的指令进行位置控制。本案例将介绍如何为一个定位控制系统配置通信,以及实现PLC与伺服之间的高效数据交换。
### 系统需求分析
在进行通信配置之前,首先需要对系统需求进行分析。定位控制系统通常要求高精度和高响应速度。因此,在选择PLC和伺服时,应考虑到它们是否能够满足这些性能要求。例如,选择支持高速计数器的PLC,以及具备快速定位功能的伺服驱动器。
此外,通信过程中可能会涉及到复杂的控制命令和丰富的状态反馈信息。因此,系统的通信协议需要能够高效地处理大量数据,同时保证数据的准确性和实时性。
### PLC与伺服连接细节
一旦需求分析完成,就可以着手进行PLC与伺服之间的连接配置了。以下是具体的步骤:
1. **接口选择**:确认PLC支持的通信接口(如RS-422)与伺服驱动器的接口匹配。确保所选的接口能够满足控制系统的距离要求和速度要求。
2. **通信协议**:选择合适的通信协议。对于定位控制系统,Modbus RTU或CC-Link等协议常被用于实现PLC与伺服之间的通信。确保协议的配置与伺服驱动器和PLC的通信协议设置一致。
3. **参数配置**:在PLC和伺服驱动器上配置必要的参数,如地址分配、波特率、数据位等。确保通信双方参数匹配,以实现正确和高效的数据交换。
4. **通信测试**:进行初步的通信测试,检查PLC与伺服之间是否能够正确交换信息。观察数据传输的响应时间和准确性,以评估通信配置的有效性。
5. **实时监控与调整**:在系统上线后,实时监控PLC与伺服之间的通信状态,并根据实际情况进行必要的调整。优化参数配置,以达到最佳的控制效果。
## 案例二:自动化生产线通信配置
自动化生产线是现代制造业中的重要组成部分,它通常包含多个工作站点,每个站点可能需要独立控制多个伺服电机。本案例将探讨如何实现PLC与多个伺服驱动器之间的集成通信配置。
### 生产线通信方案对比
在配置通信之前,需要对不同的通信方案进行对比。例如,可以对比使用单一通信网络覆盖整个生产线和使用多个独立网络分别控制每个站点的优缺点。通常情况下,为了简化布线和提高系统的可靠性,会选择将多个伺服集成到一个统一的通信网络中。
### PLC与多个伺服驱动的通信集成
为了实现多个伺服驱动器与PLC之间的集成通信,可以采取以下步骤:
1. **通信网络设计**:设计一个高效的通信网络,能够支持多个节点的接入。网络拓扑结构要尽可能减少延迟,提高通信的稳定性和扩展性。
2. **节点配置**:在PLC上配置每个伺服驱动器的通信参数,包括地址、通信速率、数据格式等。需要确保每个伺服驱动器的地址是唯一的,避免地址冲突。
3. **数据交换机制**:在PLC程序中设计数据交换机制,实现与各个伺服驱动器的实时数据交换。这包括数据的发送、接收、解析和错误处理等逻辑。
4. **同步控制策略**:考虑到生产线上的伺服驱动器需要同步运行,需要实现一种同步控制策略,确保各伺服电机的动作协调一致。
5. **故障诊断与处理**:集成通信配置后,应实施故障诊断机制,以便快速定位和处理通信故障。这可能包括对通信数据的定时监控和异常告警。
## 案例三:故障诊断与维护策略
在任何工业控制系统中,故障诊断和维护都是保证系统稳定运行的关键环节。本案例将介绍针对PLC与伺服通信过程中可能出现的常见故障,并给出相应的解决方案和维护计划。
### 常见通信故障及解决方案
常见的通信故障包括连接不稳定、数据错误、响应延迟等。诊断这些故障时,可以通过以下方法进行:
1. **物理检查**:首先检查所有的物理连接是否正确和牢固,包括电缆、接插件等。
2. **参数核对**:确认PLC和伺服的通信参数设置是否一致。不一致的参数设置往往是通信故障的常见原因。
3. **通信监控**:使用通信监控软件实时观察通信数据流,寻找数据包丢失或错误的迹象。
4. **软件诊断工具**:利用PLC或伺服驱动器提供的软件诊断工具,进行深入的故障诊断。
5. **固件升级**:在确认硬件无问题的情况下,可以尝试升级PLC或伺服驱动器的固件,以解决已知的软件问题。
### 维护计划与预防性保养策略
为了减少故障的发生,必须制定一套全面的维护计划和预防性保养策略。这包括定期的系统检查、软件更新、以及对关键部件的替换等措施。
1. **定期检查**:周期性地检查PLC和伺服的运行状态,包括检查日志信息、诊断错误、检查通信状态等。
2. **预防性保养**:为延长系统的使用寿命,应定期更换易磨损的部件,如电缆、连接器等。
3. **备份与恢复**:定期备份PLC程序和伺服参数设置,以便在出现故障时能够迅速恢复系统的正常运行状态。
4. **员工培训**:对操作和维护人员进行培训,提高他们对系统故障的识别和处理能力。
通过上述案例分析,我们可以看到将理论知识应用到实践中时,需要综合考虑系统的具体需求、环境条件以及可能遇到的问题。通过细致的规划和周密的配置,可以实现PLC与伺服之间稳定高效的通信连接,为工业自动化应用提供可靠的支撑。
# 6. 进阶优化与未来发展展望
随着工业自动化的发展,PLC与伺服驱动的通信不再仅仅满足于稳定连接,还需要考虑性能优化、远程控制以及未来技术的发展趋势。本章将深入探讨这些方面的内容,以期为读者带来更全面的理解。
## 6.1 通信性能的深入优化
通信性能是整个自动化系统效率的关键,因此,对其深入优化具有重要意义。
### 6.1.1 提高通信速率的方法
提高通信速率通常涉及硬件的升级、软件算法的优化以及通信协议的选择:
- **硬件升级**:在可能的情况下,更新为支持更高传输速率的接口硬件,如使用高速以太网卡。
- **软件优化**:针对特定的应用场景优化通信协议的实现代码,减少不必要的数据包和通信延迟。
- **协议选择**:使用专为高速传输设计的通信协议,如CC-Link IE,其传输速率可以达到1Gbps。
### 6.1.2 降低通信延迟的技术
为了降低通信延迟,需要在系统架构和程序设计上做出调整:
- **系统架构**:采用分布式控制架构,将计算和决策尽可能靠近执行部件,以减少数据传输的距离。
- **程序设计**:优化任务调度和中断处理机制,避免因为CPU负载过重导致的通信延迟。
## 6.2 远程控制与工业物联网(IIoT)
随着工业物联网的发展,PLC与伺服驱动的远程控制成为可能,并为工业自动化带来了新的机遇。
### 6.2.1 PLC与伺服在IIoT中的角色
PLC与伺服驱动作为工业物联网中的重要节点,它们的作用和影响如下:
- **数据采集**:PLC和伺服驱动可作为数据采集终端,实时收集生产过程中的各种数据。
- **智能控制**:基于收集的数据,系统可以进行智能分析和决策,实现更精细的控制。
- **远程监控**:借助云平台和IIoT技术,设备状态和性能可以远程监控,便于维护和故障诊断。
### 6.2.2 面向未来的通信技术趋势
未来,工业通信技术将向着更高性能、更安全和更智能的方向发展:
- **高性能网络**:5G、光纤通信技术将使得数据传输速度更快、容量更大。
- **网络安全**:随着工业系统与互联网的融合,网络安全将成为设计和实施的关键因素。
- **人工智能集成**:AI技术将更多地应用于数据处理、预测维护和智能控制中。
## 6.3 持续学习资源与社区支持
为了适应技术的快速发展,持续学习是必不可少的。本节将为读者推荐一些资源和社区,以供学习和交流。
### 6.3.1 在线资源与学习平台
- **官方文档与支持**:各自动化设备制造商通常提供详细的技术文档和示例项目。
- **在线课程**:众多在线教育平台提供自动化和工业控制相关课程。
- **技术白皮书**:一些技术组织和研究机构会发布有关工业通信技术的白皮书。
### 6.3.2 技术社区与开发者的交流
- **开源项目**:参与或学习开源项目可以极大地提高技术实践能力。
- **专业论坛**:如Reddit中的r/PLC和r/industrialautomation等板块,是分享经验和解决问题的好地方。
- **开发者会议和研讨会**:参与相关的会议和研讨会,不仅可以学习最新的技术,还可以拓展人脉。
在本章中,我们探讨了通信性能的优化方法、远程控制和工业物联网的应用以及持续学习的重要性。通过本章的学习,读者应能够获得对未来工业通信技术趋势的深刻理解,并对持续学习和发展职业道路有一个清晰的规划。在接下来的章节中,我们将深入探讨具体的实践案例,以实际的应用场景为蓝本,帮助读者更好地理解和应用这些理论知识。
0
0
相关推荐
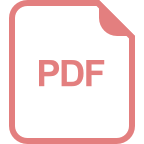
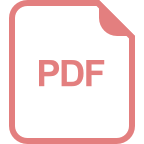
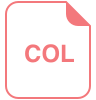
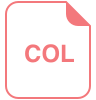
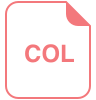
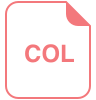
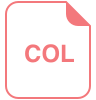
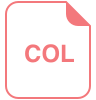