没有合适的资源?快使用搜索试试~ 我知道了~
复杂薄壁件流体压力成形技术的原理与工艺
工程7(2021)358研究金属成形技术综述复杂薄壁件流体压力成形技术的原理与工艺袁世坚a,ba哈尔滨工业大学高压流体成形技术研究所,哈尔滨150001b大连理工大学高性能精密成形研究所,大连116024阿提奇莱因福奥文章历史记录:收到2020年2020年6月15日修订2020年8月5日接受2020年11月5日网上发售保留字:液压成形热介质压力成形薄壁件应力状态A B S T R A C T针对航空航天、飞机、汽车、高速列车等行业急需的管、板、壳三种典型结构和难变形材料构件,发展了新一代的流体压力成形技术本文综述了管形件低压液压成形、板形件双面压力液压成形、椭球壳无模液压成形和难变形材料双硬化热介质成形的特别注意变形行为,应力状态调整,缺陷预防和典型应用。此外,还讨论了流体压力成形技术未来的发展方向,包括超大型非均匀构件的超低载荷成形、金属间化合物和高熵合金构件的精密成形、智能化工艺与装备、非均匀和强各向异性薄壳的精密有限元模拟等。©2020 The Corner.Elsevier LTD代表中国工程院出版,高等教育出版社有限公司。这是一篇CC BY-NC-ND许可下的开放获取文章(http://creativecommons.org/licenses/by-nc-nd/4.0/)中找到。1. 介绍具有弯曲轮廓的复杂薄壁部件对于用于运输设备的结构非常重要,例如火箭,飞机,汽车和高速列车[1这些部件至关重要,应用广泛,例如,它们占据了80%以上的航天器和50%的飞机和汽车。随着对新一代运输设备的轻质材料、长寿命周期和高可靠性的使用性能的需求不断增加,通过焊接制造的传统多段结构不能令人满意,并且迫切需要用薄壁且通常包含复杂弯曲轮廓的集成部件来替代[4]。要成功地制造这类部件,需要解决以下三大挑战:①管是非常复杂的,包括大尺寸和小特征以及具有显著变化的曲率、不规则闭合横截面、超大总体尺寸(管的长度或板的直径通常大于5 m)和超薄厚度(厚度与直径的比率小于3‰)。这些特性要求原材料的变形远电子邮件地址:syuan@hit.edu.cn这在传统的工艺中是不可能的[5]。②这些部件的优选合金难以成形。高强度铝合金[6,7]、钛合金[8,9]、金属间合金[10]和镍基高温合金[11]的可成形性在室温下较低,而它们的微观结构和机械性能在高温下会显著劣化。③部件要求尺寸精度高,性能好,两者配合使用[12]。整个部件的精度要求在亚毫米(0.1-因此,成形精度必须直接由成形来保证。此外,薄壁部件的特性(例如,极限强度)需要从原材料获得10%的增强这三个挑战必须协同处理,导致巨大的制造困难。目前使用刚性工具的成形技术[13]受到有限空间的限制,这对于大型集成部件是不够的。因此,必须使用折衷的技术方法,由此通过连接较小的成形件来制造部件。在使用这种方法中出现了显著的缺点,包括由具有降低的机械性能的合金组成的长焊缝、形状变形、表面退化、降低的可靠性以及短焊缝。https://doi.org/10.1016/j.eng.2020.08.0142095-8099/©2020 THE CONDITOR.由爱思唯尔有限公司代表中国工程院和高等教育出版社有限公司出版。这是一篇基于CC BY-NC-ND许可证的开放获取文章(http://creativecommons.org/licenses/by-nc-nd/4.0/)。可在ScienceDirect上获得目录列表工程杂志首页:www.elsevier.com/locate/engS. 元工程7(2021)358359生命周期这些导致部件不具备下一代运输设备所需的质量[14]。流体压力成形是一种金属成形技术,利用流体介质对工件进行加载和变形,使简单的一块坯料材料成形为形状复杂的一体化构件。加压流体可以取代一些传统的刚性工具,使硬金属变形并在封闭空间内施加此外,流体介质能够在变形工件的整个区域上施加均匀的压力。流体压力成形的这两个独特优势使其成为一种强大的技术,用于在一次操作中从简单形状的坯料制造集成的复杂形状的部件[15]。在20世纪90年代中期,受减轻汽车结构重量的需求的驱动,开发了管液压成形工艺,也称为内部高压成形,其中使用高达400 MPa的压力[16]。德国和美国的研究机构已经对这种液压成形工艺的变形行为、缺陷机制和核心工艺进行了研究[17,18]。特别是德国公司成功开发了大容量管材液压成形设备,实现了乘用车底盘和车身结构的批量生产[19]。日本研究人员率先研究了板材液压成形,并成功生产了汽车面板部件[20]。1998年,作者带领的课题组开始研究介绍了液压成形的基本理论和关键工艺。该研究策略旨在克服制造具有复杂曲面轮廓的集成薄壁部件的挑战。研究成果已被用于显著开发和推广使用流体压力在不同温度(冷到热)下形成具有各种几何复杂性和尺寸(从小到大)的零件以管、板、壳和难变形材料成形为重点,成功地建立了新一代流体压力成形技术,包括管状件低压液压成形、板件双面压力液压成形、椭球壳无模液压成形和难变形材料双硬化热介质压力成形本文从工艺原理、应力状态调整、缺陷预防和典型的实际产品应用等方面论述了该技术的发展现状。2. 工艺系统及应力调整原理2.1. 成型工艺系统原理为了生产不同工业部门所需的各种结构特征和材料,经过30年的研究和开发,已经使用一系列流体压力成形工艺和相关设备开发了具有不同横截面的端部开口结构、具有深腔的半封闭结构、封闭壳体和难以变形材料的部件[21],如图所示。1.一、对于在室温下成形在高温下使用的介质是气体或固体颗粒。根据目标部件的具体结构特征,使用管或板作为坯料[22]。2.2. 应力状态调整原理使构件难以成形的构件的独特特征是大的、薄壁的、封闭的横截面和整体的。将这些功能与复杂的几何形状和难以变形的材料(图1)导致出现缺陷的高趋势,如扭曲,分裂和局部变薄。为了克服这些困难,采用了利用流体介质加载调整变形区应力状态的原理,基本上,通过控制流体介质的加载方案和变形区的形状,可以将应力状态保持在能够避免缺陷的值内[23,24],如图2[24]所示。例如,为了克服分裂,应力状态从双轴拉伸改变为为了抑制扭曲,优选使用相反的应力调节考虑到典型的管、板和壳结构的成形过程,调整应力状态的实际情况的细节在以下部分中描述3. 具有不规则轮廓的管状部件的低压液压成形不规则异型管状部件是用于轻质高性能结构的理想部件液压成形管状坯料使传统的多部件焊接结构能够被更高质量的集成结构所在管坯内部压力和轴向载荷的控制由于小角的校准和变形材料的硬化,通过高达400 MPa的高压产生超大的力。由此产生的应力因此,降低成形压力一直是消除这些缺陷的全球性方法。最终液压成形压力与过渡区的拐角半径成反比根据文献[25]中的经验公式,为了成形相对拐角半径r/t(r为拐角半径,t为管厚)小于3的部件,屈服强度为450 MPa的钢管的成形压力高于150 MPa。然而,由于工件/工具界面摩擦,过渡区拐角处通常发生局部变形和减薄,这可能导致开裂。对于成形小圆角半径的方管截面的情况,可以用带碟形边的方管工件代替传统的圆管工件,以减小成形压力,其中拉应力基本上减小。这些凹面减少了工件/模具的接触。因此,变形过程中的摩擦力和内压下压平材料提供的附加力使模具角部能够在不拉伸工件的情况下被填充,如图所示。 3 [26]。当施加内部压力时,朝向模具壁移动的侧面的变形是压缩的,并且克服了减小的摩擦力。管坯在环向的应力状态由拉伸变为压缩。 如图 2 [24]中,应力状态从双轴拉伸调节到拉-压,使得变形极限增加。此外,与模具表面的接触面积减少,使材料流向拐角区域变得容易,从而显著降低所需的成形压力[26]。实验表明,与直接液压成形圆管相比,使用凹形预成型件所需的极限压力降低了50%-80%,如图所示。 四、另外,厚度均匀性(即,疏伐率的降低)增加了一倍以上。数值模拟是一个强大的工具来预测缺陷,管液压成形,而两个典型的挑战需要首先解决。除了上述完整的应力状态外,S. 元工程7(2021)358360图1.一、部件形状、工艺和应力状态。3D:三维;p:流体压力;p1:板下侧的流体压力;p2:板上侧的流体压力; T:成形温度;rh:环向应力;rz:轴向应力;rt:法向应力;ru:纵向应力;Fz:轴向力;r:流动应力;e:应变;e_:应变速率;K:强度系数;n:应变硬化指数;m:应变速率硬化指数。图二、调整应力状态的原则 deh、dez和det分 别是环向、轴向和法向方向上的应变增量。经Elsevier许可,转载自参考文献[24],©2006。图三.降低成型压力的原理。(a)圆管直接内高压成形的应力分析;(2)内凹圆管的应力分析 Ff是校准阶段管直壁承受的摩擦力,Fp是使用内凹管产生的切向推力。转载自参考文献[26],经《航空材料杂志》许可,©2006。管的宏观机械性能通常是各向异性的,这是由于在通常通过挤压、轧制或拉拔制造管的过程中产生的微结构的织构取向因此,精确确定厚度和屈服强度的各向异性参数,并利用它们建立合理的各向异性本构关系和适用于全应力状态的材料模型,对于变形和缺陷的预测至关重要使用有限元模拟。目前,为了确定本构方程中的系数,常用的各向异性本构关系需要厚度的r值和屈服强度rs,至少在三个方向上,(r0,r45,r90)和(rs0,rs45,rs90)[27]。对于板材,任意方向上的各向异性参数可以使用从板材中任何选定方向切割的单轴拉伸试样来确定,如图5(a)[28]所示。而对于管材,拉伸试样可以从仅沿其轴向取向的管材中提取,如图所示。 5(b)[28]。为S. 元工程7(2021)358361ðÞzHBBB见图4。 预成形件形状对成形压力的影响。(a)凹形预成型件;(b)成型压力。图五.位于(a)板和(b)管不同方向的单轴拉伸试样示意图。转载自参考文献[28],经《塑性工程杂志》许可,©2018。从环向(90°)取的样本,目前常用的环向拉伸试验会产生摩擦和额外的弯曲变形问题,导致相对较大的测量值-rb¼ dezcos2bdehsin2b 2dezhsinb cosbdezdeh-1分2秒错误[29]。迄今为止,还不能精确地获得管在任何方向上的机械性能为了解决这个问题,已经提出了精确确定管在任意方向上的各向异性参数的理论和方法[30]。成功地开发了一种内压和轴向载荷可控的新型胀形试验方法,该方法已用于建立复杂载荷条件下各向异性薄壁管的精确塑性本构模型[31],f rz;rh;rzh;k.这些模型,如在Eqs。(一)以及(2),能够精确地模拟非对称的扭曲以及具有各向异性特性的管的复杂变形如图 6、对皱纹的数量和轮廓都进行了很好的预测。结果表明,在该过程中产生了三个主要褶皱,中间褶皱倾向于轴向,两侧褶皱折叠。其中,rz和rh分别为轴向和环向应力;rzh为剪应力分量;k为屈服准则的各向异性系数矩阵;b表示与管轴的倾斜角; dez和deh分别为轴向和环向的应变增量; dezh为剪应变增量;rb和rb分别为管沿任意方向的屈服应力和法向各向异性系数。图图7示出了用于乘用车的底盘发动机托架,其通过使用新型凹形预成型件的低压液压成形方法制造[32]。该组件的轴在三维空间中弯曲,具有十多个复杂的不规则横截面。材料的极限抗拉强度为440MPa。采用传统的圆管直接液压成形,需要大约250 MPa的内压,而压力大小显著降低到120f;r;r;kf rcos2b;rsin2b;rsinbcosb;k11使用凹形预成型方法。 2010年,这一创新该工艺已用于该部件的大规模生产。通过图六、各向异性薄壁圆管非对称弯曲现象的模拟(a)实验;(b)有限元法结果。zHS. 元工程7(2021)358362ffiffiffiffiffiffiffiffiffiffiffiffiffiffiffi≤≤ffiffiffi图7.第一次会议。来自中国第一汽车厂的乘用车的液压成形底盘发动机支架截至2019年底,统计数据显示,已生产47万件产品,缺陷指数为0.5%。4. 整体板件的双面压力液压成形具有弯曲轮廓的成形板是火箭、飞机和航空发动机中的主要结构部件。随着对长寿命周期和更高可靠性的需求急剧增加,迫切需要集成组件来取代传统的多部件焊接组件。这些板基部件的独特特征使它们难以形成为一体,概括如下:深腔(腔的深度与直径之比大于0.5)、超细长(厚度)和半封闭轮廓。当厚径比小于某一极限值时,由于抗压屈曲能力降低,极易发生皱曲。参考文献[33,34]表明,对于低碳钢,厚度与直径的临界比约为5‰,而铝合金的低弹性模量导致抗屈曲性较低,如图8所示。因此,其临界厚度与直径比约为7‰。此外,许多成形部件的半封闭结构提供了对变形的高度约束,导致了促进断裂的复杂应力状态。半封闭壳体结构成形过程中的翘曲和开裂并存是常规成形技术难以克服的问题。常规拉深变形区处于正交拉压应力状态,压应力促进起皱,见图8。深腔半封闭构件起皱倾向与厚径比的相关性。D是直径,H是部件的高度。拉伸应力为了解决这个问题,提出了一种双面压力液压成形工艺(图9[35])。液体压力同时施加在板料的上下两侧,通过适当控制液体压力,在变形区产生反向胀形。然后,常规的拉压应力状态被积极地改变为双轴拉伸状态。避免压缩应力使得消除了弯曲倾向另外,通过控制施加在板料上表面的液体压力,可以将拉应力控制在应力空间第一象限的一定范围内,从而避免了劈裂的发生图10示出了使用双面液压成形成功成形的具有五个分支的一体化部件。以前在赤道和四个分支处焊接的结构有断裂的倾向。相比之下,由于集成组件没有焊缝,因此避免了这种趋势,并且符合厚度和尺寸精度规范。为制造大型半封闭构件,开发了一这些发展使得能够在高压下实现和控制相当大的液体体积流量世界上已成功开发的最大液压成形设备如图11所示[36]。它比德国Schloss公司以前制造的最大设备还要大。其承压液体容积为5m3,承载力为150MN,分别是Schloss设备规格的5倍和1.5倍。使用这种更大容量的设备,使用与最终部件厚度相似的薄板,使用单一操作形成燃料箱的集成圆顶[36]。取代了传统的由多个焊接段组成的部件,消除了约30 m的焊缝,有效地提高了可靠性。生产周期缩短了2/3。5. 大尺寸椭球壳体的无模液压成形椭球壳应力均匀,美观,这使得它们在建筑、液体储罐、微波通信塔和其他结构中具有吸引力。使用传统的模具成形工艺来制造椭圆形壳体通常需要几套工具。缺乏工件可成形性要求产品由焊接在一起的几个部件制成,这导致形状变形和不准确。为了克服这些问题,提出了椭圆形壳体的无模液压成形方法,该方法采用单曲率多面体壳体外接椭球壳体,然后利用流体压力将其鼓泡成形[37]第37段。然而,只有椭球壳的轴长比k在1的范围内变化Kp2能够直接已形成[38]它已经证明,虽然使用无模液压成形,轴长比(长轴和短轴之间的长度)为k>p2的扁椭圆形壳体不能由于压缩应力导致的扭曲而形成,如图12(a)所示为了避免浪费,每个采用了由两部分组成的多面体壳体扇区[39],如图所示。 12(b)[40]。在赤道地区,用具有轴长的壳代替了理想扇区(k>p2)比值小于p2(扇区II),而其余区域使用扇区I(k>p2)。在此基础上,得到了总轴长比大于p2的双母线组合壳体,能够维持赤道区双向拉伸,如图所示。 12(b)[40]。因此,S. 元工程7(2021)358363图9.第九条。板料双面液压成形原理及应力状态(a)形成原理,(b)应力状态[35]。g是片材上侧上的流体压力与片材下侧上的流体压力之间的比率见图10。 五个分支的集成组件。见图11。超大容量液压成型设备及一体化圆顶组件。经日本塑性技术学会许可,转载自参考文献[36],©2018。消除液压成形扁椭圆形壳体。建立了整个壳体的体积变化与轴长比之间的定量关系精确控制椭球面曲率半径通过控制注入的液体体积来实现[40]。图13显示了使用无模液压成形工艺成功成形的工业规模椭圆形壳体[41]。长轴和短轴的长度为4.5和3.0m,对应于1.5的轴比厚度为3 mm。6. 难变形材料零件的双硬化热介质压力成形高强度铝合金(2000系列、7000系列和这些难以变形的合金通常用于具有小特征的复杂形状的大型部件。使用当前的冷成形工艺(包括液压成形)的成功的工件变形基本上通过操纵应变硬化特性来实现,而在高温超塑性成形中使用应变速率硬化特性来实现显著的变形。依赖在这种单一的硬化性能上,严重限制了在局部变薄出现之前可以获得的变形程度;此外,可获得的成形形状复杂性因此受到显著限制[44]。众所周知,当在0.3Tm-0.5 T m(T m是材料的熔化温度)的中间温度范围内和大于0.1 s-1的应变速率下变形时,合金表现出应变硬化和应变速率硬化通过提高工件温度和采用适当的变形速率,可以同时激活机制(双重硬化)[48,49]。基于这一前提,开发了一种新的热介质压力成形工艺,使用组合应变和应变率硬化[50]。三种工艺的微观机理和应力-应变关系如图所示。十四岁基于基本物理内部变量[51],包括热介质压力成形的位错力学、晶粒尺寸和粘塑性本构关系,开发了复杂应力状态下双重硬化的分解方法。该方法能够定量表征耦合双硬化,并实现精确的工艺模拟[52]。通过一系列双轴加载实验,针对不同合金建立了通过调节热介质压力成形的压力和温度来协调的工艺窗口,如图15所示。这种工艺窗口可用于优化工艺参数和加载路径,以实现集成的精密成形S. 元工程7(2021)358364图12个。椭球体无模液压成形中单母线和双母线扇形壳的应力状态。复制自Ref。[40]经Elsevier许可,©2016。图十三. 轴长比为1.5的工业级椭球壳。难变形合金[53]。这种新型的双硬化热介质压力成形方法有可能克服仅利用工件的单一硬化特性的工艺的内在限制图16[47]示出了通过利用双重硬化机制形成的铝合金和钛合金的复杂形状的薄壁部件。对于铝合金部件,成功地形成了局部小特征,例如凸形徽标、三维(3D)复合拐角和复杂形状的横截面(矩形、圆形和花瓣形),并且厚度均匀获得花瓣形横截面的分布。对于钛合金部件,两个直径的比值(D2/D1;D1和D2为管状部件的端部直径)为2.15.尺寸精度在标称值的0.18 mm范围内。抗拉强度比原材料提高14.5%。7. 发展方向和前景在未来航空航天器、飞机、新能源汽车和高速列车等设备实现更轻、更高可靠性和更长寿命的持续目标的推动下,流体压力成形技术需要进一步发展。(1) 组合材料超大尺寸构件超低压整体成形。随着重型火箭、大型飞机和新一代高速列车的发展,迫切需要超大尺寸(高达10 m)的薄壁构件然而,由于目前的原板坯料的尺寸限制,必须使用具有多个焊缝的拼焊板,这给具有不均匀机械性能的工件带来了问题。这种非均匀坯料的变形非常复杂,在焊缝附近更容易发生此外,本发明还提供了一种方法,见图14。三个温度范围内的微观机制和应力应变关系。GBS:晶界滑动;l:临界剪切应力;a:材料系数;b:BurgerS. 元工程7(2021)358365图15. 双硬化热介质压力成形工艺窗口。图16.热介质压力成形复杂形状零件。(a)铝合金部件;(b)钛合金部件[47]。超大工件需要极高的成形载荷。例如,对于直径为5m的半封闭结构,所需的成形载荷可高达400MN。能够提供这种高负载的设备的成本非常高。未来的研究方向是发明超低压液压成形技术(载荷降低80%以上)和开发用于成形超大尺寸部件的设备。(2) 金属间化合物和高熵合金部件的精密成形。 钛铝、镍铝和高熵合金等金属间化合物是替代传统镍基高温合金的理想轻质耐热材料。然而,这些合金的延展性极低(在室温下几乎为零),同时原材料的有限尺寸也是一个明显的限制。考虑到这些材料复杂的化学成分和相变特性,有必要确定变形条件(温度、应变和应变速率)的影响,以使流体压力成形技术在实现实用零件制造的同时,能够开发出具有新特征的流体压力成形技术。(3) 液压成形智能化工艺及设备。迄今为止,计算机数字控制已用于流体压力成形的工艺和设备控制。精确数字化的闭环控制使得在成形过程中能够按照预先设计的路径来控制诸如压力、位移和夹紧力的工艺参数。然而,由于工艺的不一致性,如工件性能变化和刀具磨损,有时会形成不符合规范的部件。通过建立基于变形行为和工艺参数之间的潜在相关性的综合智能模型,能够在线自判断成形过程中缺陷的发生,这便于设备同时调整工艺参数。这种智能成型框架可以大大降低生产缺陷部件的可能性。(4) 非均匀强各向异性薄壳的变形理论与精确模拟。在流体压力成形期间,初始坯料通常在最终成形操作之前的一个或两个操作中预成形。这可能导致坯件局部变薄或变厚以及局部硬化,因此,坯件的机械/物理性能是不均匀的。从预成形到最终成形的整个变形过程是一个循环加载和卸载的多步骤过程,现有的理论和模型无法描述这些材料的变形行为。为了能够准确地预测过程和产品,需要全新的屈服方程、流动方程、本构模型和实验测试方法。确认本研究得到了国家杰出青年科学基金(50525516)和国家自然科学基金(U1637209、51175111、50375036和59975021)的资助。提交人对资助表示感谢作者感谢课题组的几位同仁,即哈尔滨工业大学高压流体成形技术研究所的刘刚教授、徐永超教授、刘伟教授、王晓松博士、韩聪博士、崔晓磊博士、苗启斌博士,以及哈尔滨工业大学高压流体成形技术研究所的何柱斌教授、王晓松博士、韩聪博士、崔晓磊博士、苗启斌博士。Yanli Lin,Dr.范晓波先生及范博士。大连理工大学高性能精密成形研究所郑凯伦博士此外,还要衷心感谢特雷弗·A教授。院长对有用的意见和帮助校对。S. 元工程7(2021)358366引用[1] [10]杨文,杨文. 能量吸收用薄壁结构的设计:由于轴向和斜向冲击力而提高耐撞性。薄壁结构2013;71:7-17.[2] Alkhatib SE,Tarlochan F,Hashem A,Sassi S.斜向冲击下薄壁波纹锥管的破坏行为。薄壁结构2018;122:510-28.[3] 王L,Strangwood M,Balint D,Lin J,Dean TA. AA2024在热成形条件下的成形性和失效机理。Mater Sci Eng A2011;528(6):2648-56.[4] 放大图片Kleiner M,Geiger M,Klaus A.通过金属成形制造轻质部件。CIRPAnn2003;52(2):521-42。[5] 郑克 ,李德杰,王丽,林 军。复杂 形状轻质 铝合金 壁板成形 技术综 述。IntJLightweight Mater Manuf 2018;1(2):55-80.[6] Shao Z,Li N,Lin J,Dean T.用新型双轴试验系统和新材料模型评价热冲压条件下金属板料的成形性。Int J Mech Sci 2017;120:149-58.[7] Palumbo G,Tricarico L.圆形铝合金试件温拉深过程的数值模拟与实验研究。JMaterProcess Technol 2007;184(1-3):115-23.[8] 白Q,林J,迪安TA,巴林特DS,高T,张Z。稳态热成形条件下Ti-6Al-4V主要软化机制的模拟。Mater Sci Eng A 2013;559:352-8.[9] Mosleh AO,Mikhaylovskaya AV,Kotov AD,Kwame JS. Ti- 6%Al-4%V钛合金超塑成形优化方法的实验、建模和模拟。 J Manuf Processes 2019;45:262-72.[10] Kim YW,Kim SL.伽玛合金材料-工艺-应用技术的进展:成功、困境与未来。JOM2018;70(4):553-60。[11] [10]杨文军,李文军. 镍基高温合金720Li的拉伸性能:温度和应变速率效应。MetallMater Trans A 2008;39:2340-50.[12] 沃勒特森湾使用液压成形的工艺链的精度。材料工艺技术杂志2000;103(3):424-33.[13] LimY,VenugopalR,乌尔索伊AG.过程控制钣金冲压。London:Springer;2014.[14] 王刚,赵毅,郝毅.高强航空铝合金搅拌摩擦焊及其在火箭贮箱制造中的应用。JMater SciTechnol 2018;34(1):73-91.[15] 穆 阿 迈 尔 湾 液 压 成 形 用 于 先 进 制 造 。 C a m b r i d g e : Woodhead PublishingLimited; 2008.[16] 杜曼F,哈特尔C。内高压成形-一种制造轻质零件的方法。J Mater Process Technol1996;60(1-4):669-76.[17] [10]杨文,王文,王文.用液体和其他柔性介质进行管和板的金属成形。CIRPAnn1999;48(2):497-513.[18] Ahmetoglu M ,Altan T. 管材液压成形:现状与未来趋势 。材料工艺技术杂志2000;98(1):25[19] 哈特尔角内高压成形的基本原理与工业应用研究进展。材料工艺技术杂志2005;167(2-3):383-92.[20] 作者:Jiangsu T.日本的金属板料液压成形。CIRP Ann1987;36(1):191-4。[21] 袁山【现代液压成形技术】。北京:国防工业出版社,2016. 中文.[22] [10] Bell C,Corney J,Zuelli N,Savings D.介绍了液压成形技术的现状、应用、研究领域、历史和未来。Int J Mater Form 2019;13:789-828.[23] 刘伟,陈艳,徐艳,袁松。复杂曲面零件多向板料液压成形。J Netshape Form Eng2016;8:1-6. 中文.[24] 袁世杰,韩春,王晓生.矩形截面汽车结构件的液压成形。 国际机床制 造 杂志2006;46(11):1201-6.[25] 刘刚,袁松,滕斌.管材液压成形过渡角部减薄分析。J Mater Process Technol2006;177:688-91.[26] 袁S,刘刚,韩春. [管材液压成形预成形减压机理分析]。航空材料杂志2006;26(4):46-50. 中文.[27] Khalfallah A,Oliveira MC,Alves JL,Zribi T,Belhadjsalah H,Menezes LF.用 于 液 压 成 形 的 各 向 异 性 管 状 材 料 的 力 学 表 征 和 本 构 参 数 识 别 。 Int J MechSci2015;104:91-103.[28] 袁S ,何志,胡伟.非理想材料本构关系的研究现状及发展方向。 J Plast Eng2018;25(4):1-10. 中文.[29] BarsoumI,Al Ali KF. 确定管道切向真应力-应变特性的程序。Int J Press VesselPip 2015;128:59-68.[30] 袁世军,何忠斌,张凯,林永林,发明人;哈尔滨工业大学,受让人。测定管任意方向的法向各向异性系数和屈服应力的方法。中国专利CN 110763567. 2020年2月7日。[31] Zhang K,He Z,Zheng K,Yuan S.拉-拉和拉-压应力状态下各向异性本构模型的实验验证。Int J Mech Sci 2020;178:105618.[32] 谢伟,袁S.有缝管扭转轴液压成形的壁厚及变形特性。机械工程杂志2016;52(22):78-83. 中文.[33] Narayanasamy R,Loganathan C.不同厚度无间隙原子钢板经锥形模和直模拉拔时的塑性极限研究。Mater Des2008;29(7):1401-11。[34] 陈云[2219铝合金曲面壳体液压成形起皱行为及变形均匀性] [学位论文]。哈尔滨:哈尔滨工业大学; 2017年。 中文.[35] 袁 S , 范 X. 超 大 尺 寸 集 成 件 精 密 成 形 工 艺 的 发 展 与 展 望 。 Int J ExtremManuf2019;1:022002。[36] 袁山我国超大型塑性加工设备的发展。Bull Japan Soc Technol Plast2018;1:14-5.[37] 曾毅,袁S,王芳,王志荣.椭球壳体整体液压胀形成形研究。J Mater ProcessTechnol 1997;72(1):28-31.[38] 张伟伟,滕宝兵,袁树杰. 无约束椭球壳液压成形过程中的变形与应力研究。Int JAdvManuf Technol 2015;76:1555-62.[39] 袁世军,张伟伟,滕宝军.两轴长比组合椭球壳液压成形研究。J Mater ProcessTechnol2015;219:124-32.[40] 袁SJ,张WW.双母线法分析椭圆壳体液压成形过程中的形状变化。 Int J Mech Sci2016;107:180-7.[41] 张WW,袁SJ. 基于响应面法的组合椭球壳液压成形预成形设计。Int J AdvManuf Technol2015;81:1977-86.[42] Zheng K,Dong Y,Zheng JH,Foster A,Lin J,Dong H,et al. The effect ofhot formquench(HFQ ®)conditions on precipitation and mechanical propertiesofaluminum alloys. Mater Sci Eng A 2019;761:138017.[43] 李毅,施志,林杰,杨扬,赛拉德,赛义德。AA2050非对称蠕变时效行为的有限元模拟及其在蠕变时效成形中的应用。 Int JMech Sci 2018;140:228-40.[44] Sartkulvanich P,Li D,Crist E,Yu KO.超塑成形对Ti-6Al-4V细晶板和标准板屈服强度性能降低的影响Mater Sci Forum2016;838-839:171-6.[45] ZhengK,Dong Y,Zheng D,Lin J,Dean TA. 采用不同高温成形工艺对可热处理铝 合 金 的 变 形 和 成 形 后 强 度 进 行 了 试 验 研 究 。 J Mater ProcessTechnol2019;268:87-96.[46] 刘刚,王凯,何波,黄明,袁松。TA15钛合金热拉伸变形过程中的饱和流变应力机制。 Mater Des2015;86:146-51.[47] ZhengK,Zheng JH,He Z,Liu G,Politis DJ,Wang L. 轻质材料管状构件热介质压力成形的基本原理、工艺及设备。Int J Lightweight Mater Manuf 2020;3(1):1-19.[48] 陈胜,王立,王林,王林,陈伟,陈伟,林俊,等.铝镁合金复杂零件热成形和冷模淬火的 数 值 研 究 . 北 京 : 机 械 工 程 出 版 社 , 2 0 0 3 . Mater Sci Forum 2013;765:368-72.[49] Zheng K,Zhu L,Lin J,Dean TA,Li N.对AA6082板材在不同高温成形工艺下的拉伸性能进行了试验研究。J Mater Process Technol 2019;273:116225.[50] 刘刚,王杰,党克,唐志。Ti-3Al- 2.5V钛管在方形横截面模具中的高压气动成形。材料2014;7(8):5992-6009.[51] Mohamed MS,Foster AD,Lin J,Balint DS,Dean TA.变形调查和失败特征在热冲压AA6082:实验和建模。Int J Mach Tools Manuf2012;53(1):27-38.[52] 吴勇,王丹,刘志,刘刚. Ti_2AlNb合金统一的内状态变量材料模型及其在热气体成形中的应用Int J Mech Sci2019;164:105126.[53] 吴勇,刘刚,王凯,刘正,袁顺。Ti- 3Al-2.5V管状件非均温热气体成形的变形与组织。 Int J Adv Manuf Technol 2017;88:2143-52.
下载后可阅读完整内容,剩余1页未读,立即下载
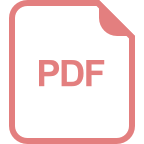
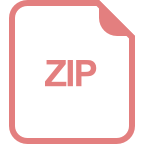
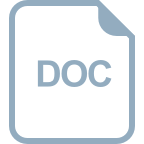
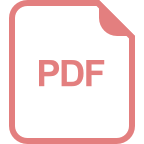
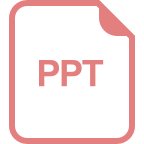
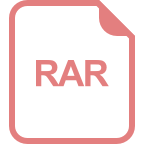
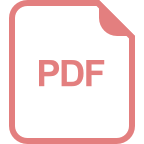
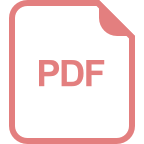
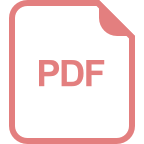
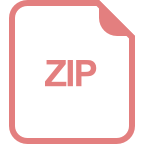
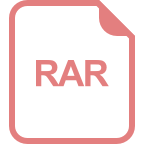
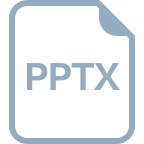
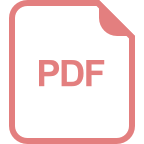
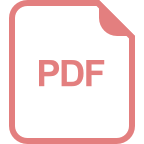
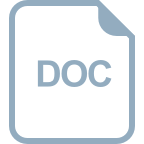
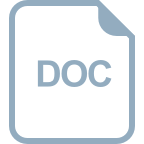

cpongm
- 粉丝: 5
- 资源: 2万+
上传资源 快速赚钱
我的内容管理 展开
我的资源 快来上传第一个资源
我的收益
登录查看自己的收益我的积分 登录查看自己的积分
我的C币 登录后查看C币余额
我的收藏
我的下载
下载帮助

最新资源
- StarModAPI: StarMade 模组开发的Java API工具包
- PHP疫情上报管理系统开发与数据库实现详解
- 中秋节特献:明月祝福Flash动画素材
- Java GUI界面RPi-kee_Pilot:RPi-kee专用控制工具
- 电脑端APK信息提取工具APK Messenger功能介绍
- 探索矩阵连乘算法在C++中的应用
- Airflow教程:入门到工作流程创建
- MIP在Matlab中实现黑白图像处理的开源解决方案
- 图像切割感知分组框架:Matlab中的PG-framework实现
- 计算机科学中的经典算法与应用场景解析
- MiniZinc 编译器:高效解决离散优化问题
- MATLAB工具用于测量静态接触角的开源代码解析
- Python网络服务器项目合作指南
- 使用Matlab实现基础水族馆鱼类跟踪的代码解析
- vagga:基于Rust的用户空间容器化开发工具
- PPAP: 多语言支持的PHP邮政地址解析器项目
资源上传下载、课程学习等过程中有任何疑问或建议,欢迎提出宝贵意见哦~我们会及时处理!
点击此处反馈


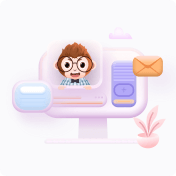
安全验证
文档复制为VIP权益,开通VIP直接复制
