【提升Calibre DRC效率】:5个优化技巧减少你遇到的问题
发布时间: 2025-01-08 14:18:11 阅读量: 3 订阅数: 8 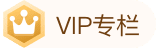
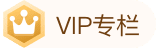
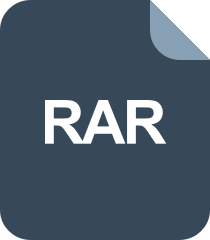
036GraphTheory(图论) matlab代码.rar
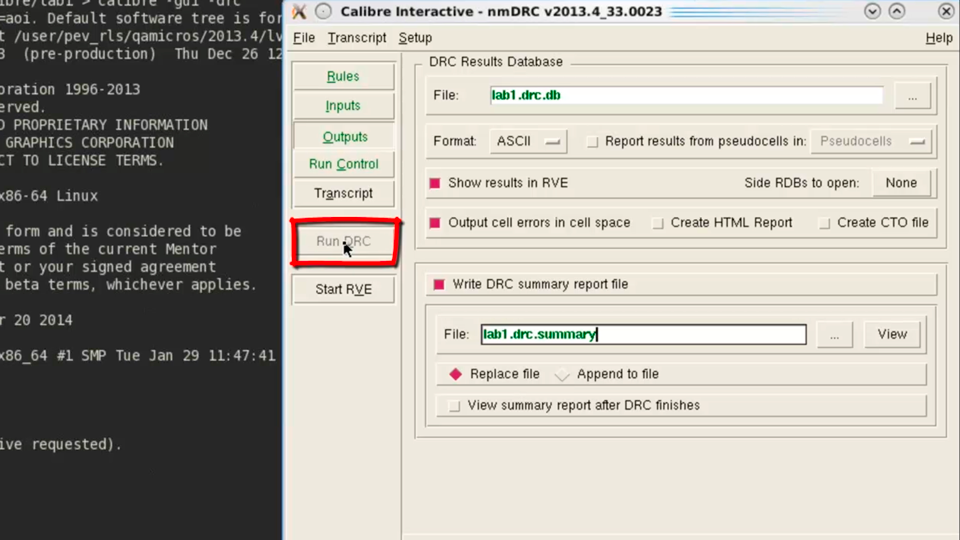
# 摘要
Calibre Design Rule Check (DRC) 是集成电路设计中不可或缺的验证工具,对于确保设计符合制造要求至关重要。本文首先介绍了Calibre DRC的基本概念、作用以及其在IC设计中的地位。接着,详细探讨了DRC规则的组成、分类和工作原理,阐述了规则类型、优先级及冲突解决方法,以及Calibre工具的工作流程和DRC引擎的核心检查算法。文章第三章分析了Calibre DRC的常见问题,包括错误的识别、诊断以及故障排除技巧。第四章则集中于如何优化Calibre DRC,提高检查效率,包括规则集优化、执行环境性能调优及流程自动化。最后,本文通过具体案例分析展示了Calibre DRC优化的实践效果,并对优化效果进行了评估和反馈。整体而言,本文旨在为IC设计工程师提供全面的Calibre DRC操作知识,帮助他们提升设计质量和生产效率。
# 关键字
Calibre DRC;设计规则检查;IC设计;规则优化;性能调优;故障排除
参考资源链接:[解决calibre DRC导入问题:路径、参数与许可证配置指南](https://wenku.csdn.net/doc/4n9525yshq?spm=1055.2635.3001.10343)
# 1. Calibre DRC简介与重要性
## 1.1 Calibre DRC背景与概述
在集成电路(IC)设计领域,版图设计规则检查(Design Rule Check,DRC)是确保设计符合制造工艺要求的关键步骤。Calibre DRC作为业界广泛使用的DRC工具之一,它的重要性不言而喻。Calibre DRC通过一套详尽的规则集检查版图设计,以防止制造过程中可能出现的问题,从而确保产品质量和良率。
## 1.2 Calibre DRC在IC设计流程中的作用
DRC不仅保障了设计在制造过程中不会产生违规现象,而且在设计早期就能发现潜在问题,避免了后期修改带来的高成本和时间损失。Calibre DRC通过准确的检查,帮助设计师在投入昂贵的硅片前,验证设计的可制造性,从而节省大量的成本和时间。
## 1.3 Calibre DRC工具的市场地位
Calibre DRC凭借其强大的功能和出色的准确性,在半导体行业中占据了重要地位。众多知名的IC设计公司和晶圆代工厂依赖于Calibre DRC来确保设计的质量。它的高性能和可靠性使设计工程师能够信心十足地推进他们的设计工作,并为复杂和多样化的IC产品提供支持。
# 2. Calibre DRC的理论基础
## 2.1 DRC的基本概念和作用
### 2.1.1 设计规则检查的定义
在集成电路(IC)设计的流程中,设计规则检查(Design Rule Check,简称DRC)是一种验证步骤,其目的是确保设计满足制造过程中各种物理和几何的限制。DRC通过与预先定义好的设计规则库进行对比,可以检测到诸如线宽、间距、对齐等可能违反制造工艺的错误。DRC对于确保设计能够在晶圆制造厂正确、高效生产至关重要。
DRC通常由自动化的EDA(Electronic Design Automation)工具执行,例如我们这次讨论的主角:Calibre工具。Calibre DRC可以看做是一系列逻辑、几何和统计运算的集合,用于检测设计是否遵循了半导体工艺所设定的一系列复杂规则。DRC是现代IC设计流程中不可或缺的一环,它在设计和制造之间架起了一座桥梁。
### 2.1.2 DRC在IC设计中的位置和作用
DRC在整个IC设计流程中扮演着重要角色。通常,在设计完成后,只有通过DRC,设计才能继续进入后续的制造准备阶段。这个阶段可能包括后端的版图物理验证、布局与原理图对比(Layout versus Schematic,简称LVS)、提取寄生参数(Parasitic Extraction)等步骤。
DRC的作用不仅限于检测并指出设计问题,它还促进了设计和制造之间更有效的沟通。制造工程师能够通过DRC报告来了解和评估设计的可制造性。此外,DRC结果是设计质量的关键指标之一,直接关系到产品良率和成本效率。
## 2.2 DRC规则的组成和分类
### 2.2.1 常见的DRC规则类型
DRC规则是一系列复杂的技术规格和要求,它们定义了设计在制造过程中的物理与几何参数限制。规则种类繁多,但通常可以分为以下几类:
1. **几何规则**:控制层与层之间的关系,如线宽、间距、孔的尺寸以及层与层之间的对齐。
2. **密度规则**:确保设计在晶圆上的密度分布均匀,避免制造过程中的热点问题。
3. **间距规则**:定义了不同物体之间的最小间距,以避免在制造过程中产生短路等风险。
4. **对齐和覆盖规则**:确保元件和连线正确对齐,覆盖无误。
这些规则通过EDA工具,例如Calibre,实现自动化检查,并且对于保证芯片的质量和生产效率至关重要。
### 2.2.2 规则的优先级与冲突解决
在实际的IC设计中,一个设计可能同时违反多个规则,而这些规则之间可能存在优先级关系。因此,确定DRC规则之间的优先级是解决规则冲突的关键步骤。
规则的优先级通常基于其对设计最终成功制造的影响程度来设定。举例来说,可能会为一些关键的制造过程设置更高的优先级,如光刻过程的规则。此外,DRC工具通常会提供一些冲突解决的策略,例如,当存在规则冲突时,优先处理影响更大、更为关键的设计问题。
Calibre DRC工具允许用户为规则设置优先级,并且在规则冲突的情况下,提供了解决的机制,这确保了设计质量的最优化。使用这些高级功能需要对工具的规则管理系统有深入的理解,这也是本章节讨论的重点内容。
## 2.3 DRC工具的工作原理
### 2.3.1 Calibre工具的工作流程
Calibre DRC工具是业界广泛使用的DRC工具之一,其工作流程可以分为几个主要的步骤:
1. **读取设计数据**:首先,工具会读入用于DRC检查的设计数据库。
2. **应用设计规则**:随后,应用定义好的DRC规则库对设计数据进行检查。
3. **识别和报告错误**:如果发现违反规则的设计,工具将生成错误报告,列出所有检查出的DRC错误。
4. **调试与修正**:设计工程师使用报告定位错误,进行必要的修改,并重新运行DRC进行验证。
Calibre工具还支持一个交互式环境,允许工程师在遇到错误时直接对设计进行修改,并立即查看修改后的影响。这个流程,结合自动化与人工干预,极大地提高了IC设计的效率。
### 2.3.2 DRC引擎与检查算法概述
Calibre DRC引擎是其核心,负责执行DRC检查的算法。这些算法必须足够高效以处理大规模集成电路的复杂设计,同时也要保证结果的准确无误。
DRC引擎使用的一系列算法包括:
1. **几何图形算法**:用于检测和分析版图中的几何图形关系。
2. **层次化搜索**:快速定位设计中的相关部分,以提高效率。
3. **并行处理**:利用多核心处理器,进行任务的并行化处理,以缩短检查时间。
4. **自适应网格划分**:优化数据存储和处理,提高内存使用效率和检查速度。
这些算法的集成和优化使得Calibre DRC能够在保证准确性的前提下,有效地处理现代IC设计的复杂性和不断增长的数据量。
下面的表格展示了不同DRC算法在处理复杂度和速度上的对比情况:
| 算法类型 | 复杂度处理能力 | 检查速
0
0
相关推荐




