连续铸钢原理探索:结晶器倒锥度的影响与技术发展
需积分: 0 50 浏览量
更新于2024-08-22
收藏 27.79MB PPT 举报
"结晶器的倒锥度在连续铸钢中的应用及连续铸钢技术的发展"
在连续铸钢过程中,结晶器的倒锥度是至关重要的一个设计参数。结晶器是连铸工艺的核心部分,它的作用是使液态钢水转变为具有一定强度的坯壳。倒锥度是指结晶器上口直径大于下口直径,形成一种向下的锥形结构。这种设计的主要目的是减少液态钢水与结晶器壁之间的气隙,从而改善传热条件,促进坯壳的快速凝固和均匀生长。
倒锥度的大小并非固定不变,它主要取决于所浇注钢种的液态收缩率。不同的钢种在高温下收缩的程度不同,因此,结晶器的倒锥度需要根据具体钢种来调整。对于板坯连铸,由于其对宽面冷却要求较高,目的是防止板坯因局部热应力不均而出现鼓肚变形或表面纵裂,所以结晶器通常会有一定的倒锥度,通常范围在0.5%~1.0%每米。
连续铸钢技术自20世纪50年代在欧美国家兴起以来,经历了从初期的探索到成熟应用的发展历程。1933年德国人Junghans建造了第一台连铸机,随后在苏联、英国和德国都有重大突破,连铸技术逐渐在全球范围内推广。70年代至80年代,连铸技术得到了快速发展,包括结晶器自动调宽、液面控制、漏钢预报等先进的工艺控制技术得到应用。进入90年代,连铸技术继续革新,如近终形连铸、高速浇铸和高清洁性产品的连铸等成为发展方向。
在中国,连续铸钢技术从1957年开始试验研究,到1958年重钢建成双流连铸机,再到1964年重钢的弧形板坯连铸机,中国也在这一领域取得了显著进步。连铸技术的优势在于节省工序、提高金属收得率、降低能耗、提升机械化和自动化水平以及保证产品质量。为了进一步提高连铸机的作业效率,多炉连烧、设备长寿命、稳定化防漏钢操作和缩短非浇注时间的维护操作等技术也在不断优化和实施。
结晶器的倒锥度是连续铸钢工艺中的关键要素,直接影响到铸坯的质量和生产效率。而连铸技术的持续发展和创新,不仅体现在硬件设备的进步,也体现在控制技术的完善和生产工艺的优化,这为钢铁行业的高效、高质量生产提供了坚实基础。
2021-09-04 上传
2020-01-27 上传
点击了解资源详情
2021-05-12 上传
点击了解资源详情
点击了解资源详情
点击了解资源详情
点击了解资源详情
点击了解资源详情
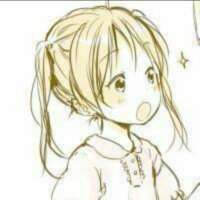
xxxibb
- 粉丝: 19
- 资源: 2万+
最新资源
- 黑板风格计算机毕业答辩PPT模板下载
- CodeSandbox实现ListView快速创建指南
- Node.js脚本实现WXR文件到Postgres数据库帖子导入
- 清新简约创意三角毕业论文答辩PPT模板
- DISCORD-JS-CRUD:提升 Discord 机器人开发体验
- Node.js v4.3.2版本Linux ARM64平台运行时环境发布
- SQLight:C++11编写的轻量级MySQL客户端
- 计算机专业毕业论文答辩PPT模板
- Wireshark网络抓包工具的使用与数据包解析
- Wild Match Map: JavaScript中实现通配符映射与事件绑定
- 毕业答辩利器:蝶恋花毕业设计PPT模板
- Node.js深度解析:高性能Web服务器与实时应用构建
- 掌握深度图技术:游戏开发中的绚丽应用案例
- Dart语言的HTTP扩展包功能详解
- MoonMaker: 投资组合加固神器,助力$GME投资者登月
- 计算机毕业设计答辩PPT模板下载