S7-1200_1500 PLC的EPOS定位控制秘籍:快速解决伺服通讯难题
发布时间: 2024-12-17 10:33:13 阅读量: 6 订阅数: 2 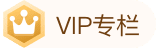
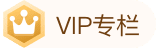

参考资源链接:[S7-1200/1500与S200伺服EPOS控制:FB38051实现基本定位教程](https://wenku.csdn.net/doc/40ii1igzqq?spm=1055.2635.3001.10343)
# 1. EPOS定位控制概述与基础
## 1.1 定位控制简介
EPOS(Electronic Positioning System)定位控制系统是一套高度集成的解决方案,用于精确控制电机的位置和速度。它广泛应用于制造业、自动化生产线和机器人技术中,通过实现精确的位置定位,提升工业控制的准确性和效率。
## 1.2 EPOS系统的组成
EPOS系统由三部分核心组件构成:控制器、执行器和传感器。控制器通常与伺服驱动器集成,执行器指的是电机,而传感器则是用来检测电机的实际位置和速度。EPOS系统通过精确控制电机的位置和速度,达到预期的定位效果。
## 1.3 定位控制的重要性
在现代工业中,定位控制是实现自动化、提高生产效率和产品质量的关键技术之一。通过精确控制机械臂、传送带等设备的移动位置和速度,EPOS定位控制系统能极大减少人为操作的错误,降低生产成本,提高系统的可靠性和灵活性。
本章为后续内容奠定基础,介绍了EPOS定位控制的基本概念、核心组件和其在工业中的应用重要性。在接下来的章节中,我们将详细探讨EPOS系统与S7-1200/1500 PLC的连接配置以及如何进行高级配置和故障排除。
# 2. S7-1200/1500 PLC与伺服驱动的连接
## 2.1 硬件连接指南
### 2.1.1 连接伺服驱动的物理接口选择
在连接伺服驱动时,首先要考虑的是选择合适的物理接口。S7-1200/1500 PLC系列提供了多种通信接口,如以太网、PROFINET、PROFIBUS等。选择合适的接口对于确保通信的稳定性和传输速度至关重要。
- **以太网**:广泛用于现代控制系统,支持多种通信协议,如HTTP, FTP, 或者是用于工业通讯的ISO-on-TCP。其传输速度快,抗干扰能力强,适合长距离通信。
- **PROFINET**:是西门子推出的工业以太网通信标准,支持实时通信和非实时通信,兼容性好,用于自动化生产线的数据交换和设备控制。
- **PROFIBUS**:是一种老一代的现场总线技术,已经被PROFINET部分替代,但仍然在某些工业自动化领域中使用。它支持较长距离的数据通信,传输速度和实时性对于某些应用仍然是可接受的。
在选择接口时,需要根据伺服驱动器的规格说明书,确认其支持哪些通讯接口和协议,以确保PLC与伺服驱动能够顺利连接。
### 2.1.2 电气接线和电缆选择
物理连接的另一个重要方面是电气接线和电缆选择。正确的电缆不仅能够保证信号的准确传输,还能提高系统的抗干扰能力。
- **电源线**:连接伺服驱动的电源时,要选择合适的电源线,以满足驱动器的电流和电压要求。通常,应使用带有屏蔽层的电源线,以减少电磁干扰。
- **信号线**:对于编码器反馈信号等低电平信号,建议使用屏蔽双绞线,以减少外部噪声和串扰的影响。
- **通讯线**:对于PROFINET或以太网连接,使用标准的CAT5e或CAT6以太网线,确保高速和稳定的数据传输。
在安装过程中,所有接线应按照制造商提供的电气接线图进行,且应由有资质的技术人员来完成,以保证系统的安全性和可靠性。
## 2.2 软件配置与参数设置
### 2.2.1 TIA Portal中的配置步骤
TIA Portal (Totally Integrated Automation Portal) 是西门子推出的自动化工程软件,提供了从项目设计、编程、模拟、调试到维护的全面自动化解决方案。S7-1200/1500 PLC的配置和伺服驱动的参数设置都可以在TIA Portal中进行。
1. **创建新项目**:启动TIA Portal,创建一个新项目,并为项目配置CPU型号,匹配实际使用的PLC型号。
2. **添加设备**:将S7-1200/1500 PLC和伺服驱动添加到项目设备树中。对于伺服驱动,可能需要下载相应的GSD文件并导入到TIA Portal中。
3. **配置硬件**:根据实际硬件连接,进行硬件配置。将相应的输入输出模块、通讯模块等拖放到相应的槽位上,并分配地址。
4. **通讯网络配置**:设置PLC与伺服驱动之间的通讯网络。根据选择的通讯接口和协议,进行相应的参数设置,如IP地址配置。
5. **下载配置到PLC**:完成所有配置后,将整个项目编译并下载到PLC中。
### 2.2.2 通信参数的匹配与调整
在TIA Portal中,通讯参数的匹配和调整是确保伺服驱动正确响应的关键步骤。以下是一些关键的通信参数和配置要点:
- **节点地址**:每个通讯设备在网络中需要有一个唯一的地址,这个地址不应与网络上的其他设备地址冲突。
- **波特率**:对于串行通信,如PROFIBUS,设置适当的波特率至关重要。波特率决定了每秒传输的位数。
- **优先级**:在实时系统中,通信请求的优先级设置可以决定数据包的传输顺序,确保关键信息优先处理。
- **超时设置**:合理的超时设置可以避免系统在通信异常时长时间等待响应,保证系统的稳定性和响应速度。
- **缓冲区大小**:对于需要高速传输大量数据的应用,增加缓冲区大小可以改善通信效率。
在进行这些参数配置时,需要参考设备的技术手册,确保所有参数都符合设备的要求。完成配置后,应当进行充分的测试,验证通讯是否稳定可靠。
## 2.3 PLC程序中的基本通讯
### 2.3.1 使用S7指令集进行基本通信
S7-1200/1500 PLC通过其指令集提供了与伺服驱动进行通信的方式。其中,使用 `TSEND` 和 `TRCV` 指令可以实现数据的发送和接收。
以下是一个简单的通信示例:
```plaintext
// 发送数据到伺服驱动
TSEND
ID:=W#16#0001, // 连接标识
LEN:=10, // 发送数据长度
TADDR:=W#16#0004, // 通信对象的逻辑地址
TID:=T#10MS; // 发送超时时间
// 接收伺服驱动回传的数据
TRCV
ID:=W#16#0001, // 连接标识
LEN:=10, // 接收数据长度
TADDR:=W#16#0004, // 通信对象的逻辑地址
R_ID:=MW100, // 接收数据的存储起始地址
TID:=T#10MS; // 接收超时时间
```
在使用这些指令时,需要仔细处理错误代码,如 `ENO`、`ERR` 和 `STATUS` 等,以便在通信失败时能够执行相应的错误处理程序。
### 2.3.2 诊断通信故障的方法和技巧
诊断通信故障是自动化系统维护中的一个关键技能。以下是一些诊断和解决问题的方法和技巧:
- **检查连接**:确保所有的物理连接都正确无误,无松动或损坏。
- **监控诊断缓冲区**:TIA Portal提供了一个诊断缓冲区,可以监控通信状态和错误信息。通过查看这些信息,可以快速定位问题所在。
- **使用指示灯**:利用设备上的状态指示灯(如PROFIBUS或以太网接口的状态灯)来判断连接是否正常。
- **逐步排除法**:当系统规模较大时,可以通过逐步关闭部分连接或设备,来缩小故障范围。
- **软件工具**:使用西门子提供的诊断工具,如SIMOCOMU,可以模拟伺服驱动进行测试。
对于诊断过程中的每一步,都应当记录详细的日志,以供后续分析和问题解决参考。
以上内容介绍了在TIA Portal环境下,如何进行S7-1200/1500 PLC与伺服驱动的连接,包括硬件连接指南、软件配置与参数设置以及PLC程序中的基本通讯。这些信息对于实现可靠和高效的伺服控制至关重要。
# 3. EPOS定位控制的高级配置
### 3.1 运动控制参数的优化
#### 位置环与速度环参数调节
在EPOS定位控制系统中,位置环与速度环参数的优化对于获得平滑且精确的运动至关重要。位置环负责控制电机达到指定的位置,而速度环则控制电机达到目标速度。参数调节通常需要考虑到系统的动态响应和稳定性的平衡。
调节位置环增益时,较高的增益可以提供更快的响应,但也可能引入振荡。反之,较低的增益会提高系统的稳定度,却降低了响应速度。速度环增益也遵循类似的原理。因此,工程师需要通过反复试验,找到适合特定应用的最佳参数。
通常在TIA Portal软件中,我们可以使用PID调节工具来辅助完成这些参数的优化。首先,通过自动调整(如Ziegler-Nichols方法)得到一组初始参数,然后根据系统的实际响应进行微调。
#### 运动曲线的配置
EPOS定位控制系统的运动曲线配置允许工程师设计出各种运动轨迹,如梯形、S型曲线等,以满足不同的运动需求。曲线的配置不仅影响运动的平滑度,还能影响到机器的加速度和减速度。
例如,梯形曲线适合于对速度变化要求不高的简单运动。而S曲线,由于其加速度曲线更加平滑,能有效地减少机械冲击和振动,适合对运动质量有较高要求的应用场景。
在TIA Portal中,可以通过图形化界面调整这些运动参数,也可以通过编程直接设定相关参数。选择合适的运动曲线,再配合正确的参数设定,可以显著提升整个定位控制系统的性能。
### 3.2 同步与多轴控制
#### 同步轴的配置方法
多轴同步运动在复杂的机械控制中非常常见,比如机械臂或传送带的协调运动。在EPOS控制系统中,实现同步轴配置的关键在于正确的时序和速度控制。
同步轴的配置通常涉及到主轴和从属轴的设置。主轴负责产生基准信号,而从属轴则根据主轴信号进行同步运动。在TIA Portal中,可以通过“同步组”来定义这些轴之间的关系,并设置延迟时间以补偿机械误差和电气延迟。
#### 多轴协调运动的实现
在实现多轴协调运动时,编程变得更为复杂。为了保证运动的准确性,必须确保所有轴的运动曲线在任意时刻都是协调的。EPOS系统提供了丰富的API来支持复杂的运动控制,如宏编程和脚本编写,允许工程师设计复杂的控制逻辑。
在编写程序时,应当考虑各轴之间的依赖关系以及可能出现的冲突。通过合理地安排运动序列和时间点,可以实现多个轴之间高精度的协调运动。代码示例如下:
```plc
// 假设定义了两个轴,Axis1为主轴,Axis2为从属轴。
// 同步启动两个轴的运动
Axis1.MoveAbsolute(500, 1000); // 移动到位置500,速度1000
Axis2.SynchronizeWith(Axis1); // 与主轴Axis1同步
Axis2.MoveAbsolute(1000, 1000); // 同时移动到位置1000,速度1000
```
### 3.3 定位控制的高级功能实现
#### 编码器反馈校准
精确的定位控制依赖于高精度的位置反馈。编码器作为反馈装置,其精度直接影响整个系统的定位精度。因此,对编码器进行校准是一个重要的步骤。
编码器校准的过程通常包括静态校准和动态校准。静态校准是在系统静止状态下进行的,检查零点偏移和分度误差。动态校准则涉及到系统运动过程中的误差评估。
在TIA Portal中,可以通过内置的工具来执行这些校准过程。一旦校准完成,编码器的反馈就能更精确地反映实际的运动状态,从而提高整体系统的定位精度。
#### 机械误差补偿与标定
机械误差的补偿通常是通过软件算法实现的,其目的是为了消除机械结构上的误差,如间隙、丝杆的非线性误差等。在某些情况下,误差可以通过预先标定得到补偿表,然后在运动控制中实时应用。
在实际操作中,标定过程可能需要反复进行,直到系统的定位误差降到一个可接受的范围内。在TIA Portal中,工程师可以利用内置的功能块来实现误差补偿,实现代码示例如下:
```plc
// 使用内置的功能块进行误差补偿
ErrorCompensation.Enable(); // 启用误差补偿
ErrorCompensation.SetCompensationTable(CompensationTable); // 设置补偿表
```
在上述代码中,`CompensationTable` 是一个预先生成的补偿数据表,包含了针对系统误差的校准值。通过这种方式,可以在电机运动时实时调整位置指令,从而达到更加精确的位置控制。
通过本章节的介绍,我们深入了解了EPOS定位控制系统的高级配置方法,包括优化运动控制参数、实现多轴同步与协调运动,以及高级功能如编码器反馈校准和机械误差补偿的实现。这些配置和技术的应用对于提升控制系统的性能至关重要,是实现精确、高效和复杂运动控制的关键步骤。在下一章节中,我们将探讨EPOS定位控制系统的故障排除与维护方法,确保系统长期稳定运行。
# 4. EPOS定位控制的故障排除与维护
## 4.1 故障诊断流程
### 4.1.1 系统自检与故障代码分析
为了保证EPOS定位控制系统的稳定运行,掌握故障诊断流程是至关重要的。首先,系统自检是故障排除的第一步。在EPOS控制系统的自检过程中,通常会涉及对硬件和软件的检查。硬件检查包括确认伺服驱动器、电机和控制器的连接是否正确无误,而软件检查则包括检查程序的正确性和参数设置的合理性。
当系统出现异常,故障代码会通过EPOS控制器的HMI(人机界面)或者远程接口显示出来。这些代码为操作人员提供了故障发生位置和原因的初步信息。例如,错误代码 "20041" 表示电机超过限制位置,这可能是由于位置传感器故障或外部限位开关故障导致。
要分析故障代码,通常需要参考EPOS控制系统的手册,了解每一个故障代码的具体含义,并且可能需要查看系统日志来分析故障发生时的详细情况。对于每一条故障代码,要根据其指向的具体原因,按照排除法进行逐一检查和处理。
```
// 示例:系统自检日志信息
Log("System self-check initiated.");
// ... 系统自检代码
if (CheckMotorConnection() == false) {
ReportError("Motor connection error: 10001");
}
// ... 其他自检逻辑
```
在这个示例代码中,`Log` 函数用于记录自检过程中的信息,`CheckMotorConnection` 函数用来检查电机连接是否正常。如果检查失败,则会调用 `ReportError` 函数来记录和报告错误代码。
### 4.1.2 实时监控与报警响应
实时监控是故障预防的重要手段。EPOS控制系统能够实时监控电机的状态,包括位置、速度、加速度、扭矩等参数。通过实时数据,可以及时发现问题的苗头,例如电机运行不稳、速度波动大等现象,这些都是潜在故障的信号。
EPOS控制器通常提供多种报警响应机制。例如,可以通过电子邮件发送报警信息给维护工程师,或者通过远程接口触发外部的报警系统。此外,EPOS控制器还允许用户自定义报警逻辑,例如当电流超过设定的阈值时触发报警。
```
// 示例:实时监控与报警响应逻辑
while (true) {
MonitorStatus();
if (IsAlarmTriggered()) {
SendAlarmNotification();
}
Sleep(1000); // 每秒检查一次
}
bool IsAlarmTriggered() {
// 检查电流、速度等参数,返回是否触发报警
float current = ReadCurrent();
float speed = ReadSpeed();
// 假设设定的报警阈值
const float currentLimit = 50.0; // 电流限制
const float speedLimit = 1000.0; // 速度限制
return current > currentLimit || speed > speedLimit;
}
```
在这个监控逻辑示例中,`MonitorStatus` 函数用来实时获取系统状态,`IsAlarmTriggered` 函数用来检查是否触发了报警。如果触发了报警,`SendAlarmNotification` 函数会负责发送报警通知。
## 4.2 常见问题的解决方案
### 4.2.1 通信失败的处理
通信失败是EPOS定位控制系统中最常见的问题之一。通信失败可能由多种原因引起,比如电缆故障、接口损坏、通信参数设置不正确、电磁干扰等。针对这些常见原因,处理通信失败的方法也有所不同。
首先需要检查物理连接,比如确认所有电缆连接是否稳固,通信接口是否完好无损。如果物理连接没有问题,接下来应检查通信参数设置是否匹配,包括波特率、数据位、停止位等参数。此外,如果使用的是以太网通信,还应检查网络设置是否正确。
```
// 示例:检查通信参数是否匹配的代码
if (CheckPortSettings() == false) {
ReportError("Port settings mismatched.");
}
if (CheckEthernetSettings() == false) {
ReportError("Ethernet settings mismatched.");
}
```
在这段代码中,`CheckPortSettings` 函数用来检查串口设置是否匹配,而 `CheckEthernetSettings` 函数用于检查以太网设置。如果不匹配,则会报告相应的错误代码。
### 4.2.2 定位不准与失步的调整
定位不准或失步可能是由多个因素引起的,如编码器读数错误、负载不稳或驱动器问题。对于定位不准,需要首先校准编码器,确保其反馈信号准确无误。加载测试也是必要的,以确保系统在不同的工作负载下均能保持准确的定位。
如果发现失步现象,应检查系统的速度环和位置环参数是否合理设置。速度环负责控制电机的加速和减速,而位置环负责确保电机到达预期位置。如果参数设置不当,可能会导致电机响应迟缓或者速度变化太快,从而产生失步。
```
// 示例:调整速度环和位置环参数
void AdjustControlParameters() {
float velocityGain = CalculateVelocityGain();
float positionGain = CalculatePositionGain();
SetVelocityControlGain(velocityGain);
SetPositionControlGain(positionGain);
}
// 假设的增益计算函数
float CalculateVelocityGain() {
// 根据实际系统特性计算速度环增益
}
float CalculatePositionGain() {
// 根据实际系统特性计算位置环增益
}
```
在上述代码中,`AdjustControlParameters` 函数用来调整控制参数,其中 `CalculateVelocityGain` 和 `CalculatePositionGain` 函数用于计算相应环路的增益值。通过这种方式可以对控制参数进行微调,以达到最佳的控制效果。
## 4.3 维护与性能优化
### 4.3.1 定期检查与预防性维护
为了确保EPOS定位控制系统的长期稳定运行,定期检查与预防性维护是必不可少的。这包括检查所有连接件是否牢固,检查电缆和接线是否存在磨损或腐蚀,以及检查风扇和冷却系统的运行状态。此外,也要定期检查伺服驱动器和电机的参数,以确保其性能没有退化。
维护人员还需要定期校准编码器,确保反馈信号的准确性。如果编码器长期使用后读数出现偏差,会导致定位精度下降。校准编码器通常是通过一系列预先设定的参考点来完成的,确保电机转动时反馈值与实际位置一致。
```
// 示例:编码器校准过程
void CalibrateEncoder() {
// 移动到预设的校准位置
MoveToCalibrationPosition();
// 获取实际编码器读数
long encoderValue = ReadEncoder();
// 计算并设置新的编码器参数
long calibrationValue = CalculateCalibrationValue(encoderValue);
SetEncoderCalibrationValue(calibrationValue);
}
```
在这个校准过程示例中,`MoveToCalibrationPosition` 函数用来将电机移动到校准位置,`ReadEncoder` 用于读取编码器的当前值,`CalculateCalibrationValue` 用来计算校准值,而 `SetEncoderCalibrationValue` 函数则用于更新编码器的校准参数。
### 4.3.2 软件更新与性能调优策略
随着技术的发展,定期对EPOS控制系统的软件进行更新是必要的。软件更新可能包括控制器的固件更新和驱动程序的更新,以获得最新的功能和性能改进。另外,某些情况下软件更新可以修复已知的漏洞和bug,提高系统的稳定性。
性能调优策略同样重要。针对控制系统的性能瓶颈,可以通过调整控制参数来优化。例如,适当增加速度环的比例增益可以提高系统的响应速度,但过度增加可能会导致系统不稳定。因此,需要找到最佳的平衡点。
```
// 示例:调整控制参数以优化性能
void OptimizePerformance() {
float tuningValue = CalculateTuningValue();
AdjustControlParameter(tuningValue);
}
```
在这段代码中,`CalculateTuningValue` 函数用于计算适合当前系统的调整值,而 `AdjustControlParameter` 函数则用于应用这个调整值。该策略应根据实际应用情况来调整,以获得最优的系统性能。
# 5. EPOS定位控制实践应用案例分析
## 5.1 单轴定位控制应用
在工业自动化领域,单轴定位控制是基础也是关键环节,它直接影响到生产效率和精度。以下内容将通过案例深入分析单轴定位控制在实际应用中的表现。
### 5.1.1 精确点位的控制示例
精确点位控制是单轴定位控制的典型应用场景之一,主要应用于需要重复定位的机械运动中。例如,机械臂需要精准抓取特定位置的工件,或者装配线上的螺丝机需要准确打螺丝等。此类控制通常要求极高的精度和重复定位能力。
在实现精确点位控制时,控制参数的设置非常关键。以EPOS4 2.5轴模块为例,其控制精度可以达到0.01微米。为了实现这样的精度,必须对伺服电机进行精细配置。首先,需要设置电机参数,如极数和编码器类型。其次,需要通过EPOS内置的位置控制器进行PID参数调整,以优化定位精度和动态响应速度。
以下是使用EPOS4实现精确点位控制的示例代码:
```plaintext
// 初始化代码略
// 配置EPOS4参数
EPOS4 POSITIONING(0x60FF, 0x0000, 0x0005, 0x0003);
const int jointNumber = 1; // 单轴控制
const int ptpMode = 1; // PTP运动模式
const int homingSpeed = 50; // 寻参速度(每秒50个计数单位)
const int maxSpeed = 500; // 最大速度(每秒500个计数单位)
const int accProfile = 10; // 加速曲线斜率
// 设置参数
POSITIONING.setConfiguration(jointNumber, ptpMode, homingSpeed, maxSpeed, accProfile);
// 执行点位运动
POSITIONING.moveAbsolute(targetPosition);
```
在上述代码中,我们初始化了一个EPOS4控制器,并设置了运动控制参数。`moveAbsolute`函数将电机移动到指定的`targetPosition`位置。为了达到更好的控制效果,开发者需要根据实际机械系统的反馈,微调PID参数,以获得最佳的定位性能。
### 5.1.2 定位控制系统的稳定性测试
稳定性测试是验证单轴定位控制性能的重要环节。通过一系列重复测试,可以确保在长时间运行过程中控制系统的稳定性和可靠性。这一步骤对于确认生产系统长期运行无故障具有决定性意义。
在进行稳定性测试时,通常会设定一个测试循环,让单轴控制器执行一定次数的往复运动,并记录每次运动的定位时间、位置误差等数据。通过分析这些数据,可以评估定位控制系统的整体性能。
示例测试脚本如下:
```plaintext
// 循环测试1000次
for (int i = 0; i < 1000; i++) {
// 移动到初始位置
POSITIONING.moveAbsolute(0);
// 等待到达初始位置
while (POSITIONING.isMoving());
// 移动到目标位置
POSITIONING.moveAbsolute(targetPosition);
// 等待到达目标位置
while (POSITIONING.isMoving());
// 读取并记录位置误差等参数
// ...
}
```
通过多次执行上述脚本,并进行数据记录,可以发现系统在长时间运行后的性能变化,从而判断是否需要进一步优化控制参数,或对硬件进行维护。
## 5.2 复杂运动控制应用
在许多生产环境中,单轴定位控制并不能满足所有要求,多轴联动控制,以及同步运动与复杂曲线的实现变得越来越重要。
### 5.2.1 多轴联动控制案例
多轴联动控制是工业自动化中的高级应用,例如在机器人焊接、电子组件的贴装、医疗设备的精密操作中都有广泛的应用。多轴联动可以实现复杂的空间运动,提供更高的生产灵活性和效率。
为了实现多轴联动控制,首先需要同步各轴的参数,包括速度、加速度以及运动曲线。EPOS提供了对多轴同步控制的支持,可通过TIA Portal等软件进行配置。在实际应用中,开发者需要确保所有轴的时钟同步,以及在软件中精确控制每个轴的运动。
以下是一个多轴联动控制的简例代码:
```plaintext
// 假设有三个轴同时运动
EPOS4 X_AXIS(0x60FF, 0x0001, 0x0005, 0x0003);
EPOS4 Y_AXIS(0x60FF, 0x0002, 0x0005, 0x0003);
EPOS4 Z_AXIS(0x60FF, 0x0003, 0x0005, 0x0003);
// 同步移动到特定位置
X_AXIS.moveAbsolute(xPosition);
Y_AXIS.moveAbsolute(yPosition);
Z_AXIS.moveAbsolute(zPosition);
```
上述代码示例中,我们假设有三个轴分别由三个EPOS4控制器控制,它们同时移动到预设的位置。在复杂的多轴应用中,开发者还必须考虑到运动轨迹的优化,避免发生碰撞或干涉。
### 5.2.2 同步运动与复杂曲线的实现
在某些高级应用中,机械臂或者平台需要执行非常复杂的运动轨迹。同步运动需要精确控制多个轴的协调,而复杂曲线则要求控制器能够处理非线性的路径。
例如,在飞机制造的蒙皮打磨工作中,需要机器人沿着飞机外壳的曲面进行打磨。为了实现这种非线性轨迹,控制系统必须能够支持插补运动,如圆弧插补或样条插补。
EPOS控制器提供了圆弧和样条插补功能,开发者可以通过发送一系列指令来定义复杂的运动轨迹。以下是一个简单的圆弧插补示例:
```plaintext
// 定义圆弧起始点和终点
Position起点 = {x: xStart, y: yStart, z: zStart};
Position终点 = {x: xEnd, y: yEnd, z: zEnd};
// 设置插补参数并执行圆弧插补
EPOS4 INTERPOLATION(0x60FF, 0x0004, 0x0005, 0x0003);
INTERPOLATION.moveArc起点, 终点);
```
在上述示例中,`moveArc`函数实现了从起始点到终点的圆弧插补运动。开发者可以通过TIA Portal配置更多的插补参数,以适应不同的运动需求。
## 5.3 系统集成与工业自动化
随着工业4.0和智能制造的发展,EPOS定位控制越来越多地被集成到复杂的工业自动化系统中,例如生产执行系统(MES)和企业资源计划系统(ERP)。
### 5.3.1 与MES/ERP系统的集成案例
将EPOS定位控制集成到MES或ERP系统中,能够实现更高层次的生产管理。例如,通过MES系统,可以实时监控生产线上的每个运动控制单元,收集生产数据,分析生产效率,甚至进行生产调度和优化。
一个典型的集成案例是电子组装生产线。在该应用中,EPOS定位控制器被用来控制贴片机和点胶机的运动。这些运动控制单元需要与MES系统交换数据,如位置信息、故障日志和生产状态。MES系统利用这些数据优化生产流程,实现零停机时间。
为了实现该集成,开发者需要配置EPOS单元与MES系统之间的通信接口,比如使用OPC UA或Modbus协议。以下是实现MES集成的基本步骤:
1. 在EPOS单元上设置通信参数。
2. 在MES系统中配置通信模块,并建立与EPOS控制器的连接。
3. 在MES系统中定义数据交换的规则和格式。
4. 在生产过程中,实时监控和收集数据,通过MES系统进行处理和分析。
### 5.3.2 自动化流水线中的EPOS控制应用
在自动化流水线中,EPOS定位控制单元不仅可以实现单轴或多轴运动控制,还可以执行复杂的协调运动。这样的运动控制能够大幅提高流水线的灵活性和生产效率。
以汽车制造厂的装配线为例,EPOS控制器可以用于汽车座椅的精确安装。每个座椅都需要从不同角度和位置插入车体内部。这个过程涉及到多个EPOS定位控制器协调动作,实现精准定位和插入。
EPOS控制器通过编程实现精确的运动序列,每个动作都有严格的时序和位置要求。控制程序需要经过精心设计,以确保在高速生产过程中仍能保持高精度。这通常涉及到复杂的错误处理逻辑,以应对可能出现的异常情况,保证生产的连续性。
在自动化流水线中集成EPOS控制器的过程包括:
1. 与设备制造商协商,获取机械图纸和运动要求。
2. 设计运动控制程序,实现精确的运动序列。
3. 在TIA Portal中配置控制器和驱动器,进行现场调试。
4. 根据生产需求调整和优化运动控制程序。
5. 在实际生产过程中实时监控和调整以保证生产效率。
通过上述各章节的案例分析,我们可以看到EPOS定位控制在实际应用中展现出的强大功能和灵活性。这些案例体现了如何将EPOS定位控制技术应用于不同的工业场景,解决了许多自动化控制的难题,也推动了工业自动化的进步。
# 6. 未来趋势与技术革新
在前几章中,我们讨论了EPOS定位控制的配置、故障排除以及它的实际应用案例。随着技术的持续进步,EPOS控制技术也在不断发展,本章将探讨这些技术革新的前沿动态及其对未来工业生产的影响。
## 6.1 工业4.0背景下的EPOS定位控制
### 6.1.1 智能制造与EPOS控制的关系
随着工业4.0的浪潮席卷全球,制造业正在经历前所未有的变革。智能制造系统依赖于高度自动化和互连的生产流程,而精确和可靠的定位控制是实现这一目标的关键。EPOS系统作为这类控制的关键组成部分,通过实时处理传感器数据、机器反馈信息,以及与企业资源规划(ERP)系统的集成,能够实现智能工厂的高效运作。
### 6.1.2 5G/物联网与EPOS控制的结合
5G和物联网(IoT)技术的迅速发展,为EPOS定位控制带来了新的可能性。5G的高速率和低延迟通信特性,使得机器间的实时数据交换变得更为高效和可靠,这对于同步多轴运动控制至关重要。物联网的普及让更多的设备接入网络,EPOS控制的设备可以通过IoT平台进行远程监控和管理,实时的设备状态反馈与自动化的决策支持,使生产过程更加智能化和灵活。
## 6.2 新一代伺服驱动技术展望
### 6.2.1 高性能伺服驱动的发展方向
新一代伺服驱动技术正朝着更高性能、更低能耗和更智能的方向发展。性能的提升体现在更快的响应速度和更精确的控制精度上,这对于实现高速高精的定位控制至关重要。低能耗的实现通过改进驱动器的效率和采用更高效的电机技术来达成,这不仅降低了工业生产的运行成本,也有助于实现更环保的生产过程。
### 6.2.2 能源效率与环境适应性的提升
伺服驱动技术的另一个发展趋势是能源效率和环境适应性的提升。通过采用更先进的能量回馈技术,伺服驱动器可以减少能源消耗,并将多余的电能回馈至电网。此外,新一代的伺服驱动器在设计上更加注重对环境因素的适应性,如能在高温、高湿或有腐蚀性气体的环境中稳定工作,进一步拓展了EPOS系统的应用范围。
## 6.3 开源与定制化解决方案
### 6.3.1 开源硬件和软件在EPOS控制中的应用
开源硬件和软件在EPOS控制系统中的应用为用户提供更大的自由度和灵活性。开源硬件如Raspberry Pi可以作为EPOS系统的控制核心,结合Linux或RTOS等开源操作系统,用户可以自主开发和优化控制软件,满足特定应用的需求。同时,开源社区提供的丰富资源和工具也降低了开发成本,并加快了项目的实施速度。
### 6.3.2 定制化解决方案的实施与案例
定制化解决方案能针对特定的行业应用提供优化的EPOS控制策略。例如,在高精度制造业,可能需要对定位控制算法进行定制化调整,以满足零件加工的微米级精度要求。在包装行业,控制系统可能需要特别优化以适应不同材料的特性。这些定制化的解决方案通常是与设备供应商紧密合作完成的,案例分析可以帮助我们理解这些解决方案的实施过程以及它们在实际应用中的成效。
通过本章的讨论,我们可以看到EPOS定位控制技术正朝着更加智能化、集成化和定制化的方向发展。这不仅为生产效率和产品质量的提升带来了新的机遇,也为IT和自动化行业从业者提出了新的挑战和学习方向。在不断变化的技术环境中,保持对行业趋势的敏锐洞察力并积极适应技术革新,将使我们更好地迎接未来的挑战。
0
0
相关推荐
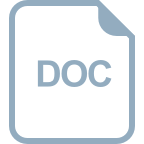
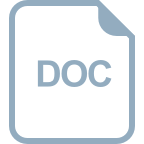
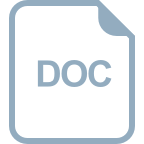
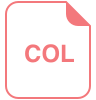
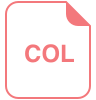
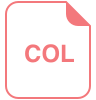
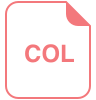
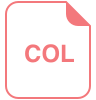
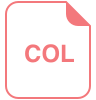