深入解析Fanuc系统变量:20个高级参数不为人知的应用案例
发布时间: 2025-01-04 06:48:48 阅读量: 14 订阅数: 12 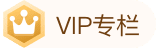
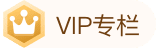

# 摘要
Fanuc系统作为工业自动化领域的先驱,其系统变量对于机床性能的优化和故障诊断具有至关重要的作用。本文系统地介绍并分析了Fanuc系统变量的基础理论,包括不同分类的功能及设置方法。进一步,文章探讨了高级参数在实际应用中的技巧,如提升机床性能、进行故障诊断与预防性维护,以及在智能制造中的创新应用。为了确保参数调整的安全性和有效性,本文还提供了调试与优化的具体步骤,并通过案例分析展示了参数调整的实际成效。最后,文章预测了Fanuc参数技术的发展趋势和面临的技术挑战,旨在为工业自动化领域的参数应用提供全面的参考和指导。
# 关键字
Fanuc系统变量;高级参数;故障诊断;生产效率;智能制造;参数调试与优化
参考资源链接:[FANUC机器人系统变量手册:接口配置与诊断](https://wenku.csdn.net/doc/1rm8zqrciz?spm=1055.2635.3001.10343)
# 1. Fanuc系统变量概述
## 1.1 系统变量简介
在数控机床的世界中,Fanuc系统变量扮演着核心角色,它们是机床运行状态的数字化体现,能够影响到机床的各个方面,从简单的控制到复杂的加工策略。系统变量是一系列预设的内存位置,用于存储机床的实时数据,比如速度、位置、温度等,还能够控制机床的特定功能。
## 1.2 系统变量的类型
系统变量主要分为两类:只读变量和可写变量。只读变量通常用于监控机床状态,比如当前的主轴速度或者机床的温度信息。可写变量则允许操作者或程序通过写入新值来改变机床的行为,例如修改加速度限制或者调整进给速率。
## 1.3 系统变量的重要性
了解并正确使用Fanuc系统变量对于机床的操作者和程序员至关重要。它们能够帮助进行日常的维护、故障排除、性能优化,甚至可以实现对加工过程的微调,以适应特定的加工要求。掌握这些变量的使用,不仅可以提高操作的准确性,还能延长机床的寿命,提高整体的加工效率。
在下一章,我们将深入探讨Fanuc高级参数的基础理论,包括参数的分类、功能以及设置和调整方法,为深入学习和应用打下坚实的基础。
# 2. Fanuc高级参数的基础理论
### 2.1 参数的分类和功能
#### 2.1.1 系统维护与诊断参数
在Fanuc系统中,维护和诊断参数扮演着至关重要的角色。这些参数通常包括系统运行状态、错误代码、维护记录、诊断信息等。它们使得操作者能够及时了解机床的状态,对机床进行必要的维护,同时快速定位和解决机床在运行中出现的故障问题。
下面是一个系统维护与诊断参数的示例表格:
| 参数代码 | 参数名称 | 描述 |
|----------|--------------|--------------------------------------------------------------|
| #3001 | 系统状态 | 显示机床的状态信息,如启动、停止、报警等 |
| #3004 | 错误代码 | 显示最近发生的错误代码和信息,辅助故障诊断 |
| #3201 | 维护记录 | 记录机床需要执行的维护项目以及完成情况 |
| #3210 | 诊断信息 | 提供特定的诊断信息,帮助操作者理解当前机床的工作状态或问题 |
这些参数不仅可以帮助操作者监测机床健康状况,还能够通过数据分析和错误代码的查询,提高维修效率和准确性。
#### 2.1.2 伺服控制与性能优化参数
伺服控制与性能优化参数涉及机床的响应速度、准确性和稳定性。通过这些参数的调整,可以改善伺服电机的跟踪精度,优化加减速特性,从而提高机床的整体动态性能。
一个关键的参数示例是:`#3218 (伺服响应倍率)`。它控制着伺服电机对指令变化的响应速度。增加此参数可以提高响应速度,但过高的设置可能导致系统振荡。
```mermaid
graph TD
A[伺服参数调整] --> B[增加响应倍率]
B --> C[提高响应速度]
C --> D[可能引起振荡]
```
上图用Mermaid流程图的方式展示了伺服响应倍率参数调整后对机床性能的影响路径。
#### 2.1.3 加工参数与刀具管理
Fanuc系统中还包含了用于加工过程控制和刀具管理的高级参数。这些参数控制切削速度、进给率、刀具寿命等,对于保证加工质量、延长刀具寿命及减少不必要的刀具更换操作至关重要。
例如,`#700#710`参数组用于设置刀具的寿命管理,其中`#700`控制刀具寿命计数器的初始值,`#710`设置刀具寿命计数器的递增值。
```plaintext
示例代码块:
G10 L10 P700 R1000 ; 设定刀具寿命计数器的初始值为1000
G10 L11 P710 R50 ; 设定刀具寿命计数器每次递增值为50
```
### 2.2 参数的设置和调整方法
#### 2.2.1 参数的读取与写入流程
在进行参数设置和调整之前,操作者需要先通过Fanuc系统的诊断功能读取相关参数。对于需要修改的参数,操作者必须遵循一定的写入流程,确保更改能正确地被执行,避免对机床造成损害。
下面是一个参数读取与写入的流程图示例:
```mermaid
graph LR
A[进入诊断模式] --> B[读取参数]
B --> C[确认参数值]
C --> D[修改参数值]
D --> E[写入修改]
E --> F[系统确认写入]
F --> G[退出诊断模式]
```
#### 2.2.2 参数调整的注意事项
在调整Fanuc高级参数时,需要特别注意一些操作要点。首先,应在机床空闲时进行参数设置,以避免对生产造成影响。其次,每个参数调整后,需要记录当前的值,以便将来需要恢复原始设置。最后,对于关键参数的更改,建议先进行小幅度的调整,并进行测试以确认效果。
#### 2.2.3 常见参数调整案例分析
在实际操作中,对特定参数的调整常伴随案例学习。例如,在某一特定加工任务中,针对切削振动问题,调整`#1412 (进给轴振动抑制增益)`参数能够有效减少振动,提升加工精度。
```plaintext
案例代码块:
G10 L10 P1412 R10 ; 设定进给轴振动抑制增益参数为10
```
通过此案例,可以看出参数调整对于实际生产问题解决的重要性,并提供了一种实际操作的示例。
# 3. Fanuc高级参数的实践应用
## 3.1 提升机床性能的参数应用
### 3.1.1 参数对加速度和速度的控制
在Fanuc数控系统中,通过高级参数对机床的加速度和速度进行精确控制,是提升机床性能的关键。加速度和速度的参数控制涉及到主轴、进给轴等多个运动轴的协调,这不仅影响到加工效率,也与加工精度和表面质量息息相关。
当调整这些参数时,需要充分考虑机床负载、材料类型和加工工艺。例如,参数N0641设置为启动伺服轴的加速度限制值,N0642为减速度限制值。通过合理设置这两个参数值,可以防止因加速度或减速度过大而导致的机床抖动和加工件的精度损失。
```
# 读取加速度限制参数
O0001 (读取加速度参数)
N1 G21 (使用毫米单位)
N2 G0 A#1006 (读取参数N1006的值,代表A轴最大加速度)
N3 G0 B#1007 (读取参数N1007的值,代表B轴最大加速度)
N4 M30
```
在上述示例代码中,我们使用了G0代码来读取特定轴的加速度参数,并在控制台或操作界面中显示出来。需要注意的是,对于不同的机床和系统,这些参数编号可能会有所不同,需要根据实际情况进行调整。
### 3.1.2 精确控制定位的高级参数
定位精度是影响机床性能的另一个重要因素。为了实现精确控制,Fanuc数控系统提供了多个高级参数,用于调整定位控制的细节。例如,参数N0650用于设置定位系统的增益,而N0651用于设定定位误差的补偿值。
```
# 设置定位增益参数
O0002 (调整定位增益)
N1 G0 X#1010 (读取X轴当前位置)
N2 #1010=[#1010+10] (提高X轴定位增益)
N3 #1011=20 (设定X轴误差补偿值为20微米)
N4 M30
```
在该代码段中,我们通过修改N0650参数来提高X轴的定位增益,进而增强定位精度。同时,还设置了N0651参数以进行误差补偿。提高定位增益通常能够使机床快速且准确地达到目标位置,但同时也可能增加系统振荡的风险,因此需要根据实际机床的响应特性来谨慎调整。
## 3.2 故障诊断与预防性维护
### 3.2.1 参数在故障诊断中的作用
在故障诊断过程中,Fanuc数控系统的高级参数发挥着重要作用。通过监控特定的参数,操作人员可以实时了解机床的状态,并迅速定位问题所在。例如,N1361到N1364是用于伺服电动机的监控参数,可以显示电动机是否正常工作。
```
# 监控伺服电动机状态参数
O0003 (监控伺服电动机状态)
N1 G21 (使用毫米单位)
N2 G0 A#1361 (读取A轴伺服电动机的监控参数)
N3 G0 B#1362 (读取B轴伺服电动机的监控参数)
N4 M30
```
该示例代码用于读取A轴和B轴伺服电动机的监控参数。在实际应用中,通过对比参数值和正常工作范围,操作人员可以快速判断电动机是否发生故障,如过热或电流异常等,从而及时采取相应措施。
### 3.2.2 预防性维护的参数案例研究
预防性维护可以有效地延长机床的使用寿命,降低故障率。使用Fanuc系统参数,可以预先设定机床的保养提醒,甚至主动调整某些参数以适应机床磨损程度,提前预防可能的问题。
```
# 设定维护提醒参数
O0004 (设定维护提醒)
N1 #1320=1000 (设定加工时间参数,达到1000小时后提醒维护)
N2 #1321=1000 (设定累计运行时间参数,同样设定为1000小时)
N3 M30
```
在上述示例中,N1320和N1321参数被设定为1000小时,当加工时间或累计运行时间达到这个设定值时,系统会自动提醒用户进行维护。通过设置这样的参数,可以帮助操作人员遵循定期维护的计划,从而提高整个机床系统的可靠性和稳定性。
## 3.3 提高生产效率的参数技巧
### 3.3.1 减少空闲时间的参数设置
在生产过程中,机床的空闲时间是影响效率的重要因素。通过优化Fanuc系统的高级参数,可以减少机床的空闲时间,如快速定位、快速进给和自动换刀等功能的参数设置。
```
# 设置快速定位参数
O0005 (设置快速定位参数)
N1 #1000=1 (启用快速定位功能)
N2 #1001=1500 (设定快速定位的移动速度)
N3 M30
```
在上面的代码中,#1000参数用于控制是否启用快速定位功能,#1001参数用于设定快速定位移动速度。通过适当增加定位速度,可以缩短机床的非加工时间,提升效率。
### 3.3.2 高级参数在自动化生产中的应用
自动化生产是提高生产效率的有效途径。使用Fanuc系统的高级参数,可以优化自动化生产过程,例如,通过参数调整实现自动润滑、自动换刀等高级功能。
```
# 启用自动润滑功能
O0006 (启用自动润滑功能)
N1 #1020=1 (启用自动润滑功能)
N2 #1021=60 (设定润滑周期为60分钟)
N3 M30
```
示例代码展示了如何通过修改参数#1020和#1021来启用自动润滑系统,并设置润滑周期。自动润滑可以减少人工维护的频率,降低生产成本,同时也能延长机床部件的使用寿命。
通过上述章节的分析,我们可以看出,Fanuc高级参数的应用对于提升机床性能、实现故障诊断与预防性维护、以及提高生产效率具有显著效果。在下一章中,我们将继续深入探讨Fanuc高级参数的高级应用技巧,以帮助读者更好地掌握和利用这些参数优化数控机床的性能。
# 4. Fanuc高级参数的高级应用技巧
## 4.1 参数在复杂加工中的应用
### 4.1.1 复杂形状加工的参数调整策略
在面对复杂形状的加工任务时,Fanuc数控系统能够通过高级参数的调整来优化加工性能。此类调整策略涉及对机床动态响应、轨迹规划和切削力的精确控制。例如,使用G代码编程时,可以通过调整加速度参数`$1022`和`$1023`来优化机床的加减速度,以适应不同的加工轮廓。
对于复杂轮廓的加工,高级参数如`$1412`(进给率倍率)和`$1413`(主轴转速倍率)的调整显得尤为重要。这些参数可以被设置为不同的值,以适应轮廓的不同部分,从而实现更加精细的加工。
```
G01 X100 Y100 Z10 F150 S1000
; 通过调整 $1412 和 $1413 来适应复杂轮廓
G03 X150 Y150 I25 J25
```
在上述代码段中,F指令和S指令后面的参数`$1412`和`$1413`可以通过数控系统在加工前预设,以达到精细调整加工过程的目的。
### 4.1.2 多轴联动加工的关键参数设置
对于多轴联动的复杂加工,高级参数的设置更为关键,尤其是在航空和汽车工业领域。关键参数如`$3105`(最大轴联动速度)和`$3106`(轴同步误差补偿)的调整可以显著影响加工的精确度和效率。
在多轴联动的设置中,参数`$2001`(轨迹误差控制)和`$2002`(进给率控制)需要根据加工要求进行详细配置。这些参数影响着机床在多轴加工中的动态响应,是实现复杂形状精确控制的基础。
## 4.2 参数在智能制造中的创新应用
### 4.2.1 智能制造对参数的新要求
随着工业4.0和智能制造的推进,Fanuc数控系统的参数应用也有了新的要求。智能制造环境下,需要参数具备更高的灵活性和智能化特性,如自适应控制参数`$1860`(进给率控制模式)和`$1861`(速度控制模式)。这些参数能够帮助数控系统在实时监测加工状态后自动进行调整。
高级参数的设置不仅局限于机械性能的优化,更延伸至加工过程的预测性维护。利用高级参数,如`$1862`(刀具寿命管理参数)和`$1863`(刀具磨损补偿参数),数控系统可以监控刀具状态,并在刀具磨损到临界值时发出预警或自动补偿。
### 4.2.2 实现设备互联的参数解决方案
设备互联是智能制造的重要组成部分。在设备互联的背景下,Fanuc数控系统可以通过设置参数如`$1218`(以太网控制)和`$1219`(远程操作控制)来实现与其他制造设备和系统的通信。
参数设置的表格如下所示:
| 参数编号 | 功能描述 | 可能的值范围 | 推荐设置值 |
|---------|----------------------------|--------------|------------|
| $1218 | 以太网控制 | 0~1 | 1 |
| $1219 | 远程操作控制 | 0~1 | 1 |
| ... | ... | ... | ... |
通过参数的适当配置,数控机床可以集成至工厂的物联网(IoT)网络中,实现设备之间的信息共享和协同工作。
## 4.3 参数在极端条件下的调整技巧
### 4.3.1 高温环境下的参数优化
在高温环境下加工时,机床的热膨胀和热变形会对加工精度产生影响。通过调整参数如`$1420`(温度补偿参数)和`$1421`(温度补偿模式),可以使机床的控制系统自动补偿因温度变化引起的加工误差。
为了实现这些参数的优化,通常需要先进行机床的热误差检测。根据热误差数据,数控系统可以计算出需要补偿的参数值,以保证加工精度。
### 4.3.2 高精度加工环境的参数配置
对于高精度加工,参数的配置需要特别细致,以达到微米级别的加工精度。参数如`$1424`(微米进给率调整)和`$1425`(微米主轴转速调整)在这种情况下非常关键。
参数`$1424`和`$1425`的调整需要结合精密测量工具和高精度加工的工艺要求来实施。通常,这需要在机床上进行多次试加工和测量,以确定最佳的参数设置。
在此过程中,机床操作者需要对CNC系统有深刻的理解,包括参数的具体作用、相互间的依赖关系以及对加工质量的影响。通过仔细调整这些参数,可以提高加工件的尺寸精度和表面光洁度。
在实际操作中,应先设定一个基础值,然后依据加工结果进行逐步微调。例如,如果加工件的尺寸略大于设计尺寸,可适当减少`$1424`的值,反之则增加。
通过上述的分析与案例,可以看出Fanuc高级参数在复杂加工、智能制造以及极端加工条件下的应用技巧。这些参数不仅影响加工过程的效率和精度,更是连接数控机床与先进制造技术的桥梁。随着数控技术的不断发展,这些参数的应用也会继续拓展,助力于制造业的不断创新和升级。
# 5. Fanuc高级参数的调试与优化
在本章节中,我们将深入探讨Fanuc高级参数调试与优化的实践流程。该过程不仅涉及对机床性能的精调,还包括预防性维护和生产效率提升策略。调试与优化过程要求操作者具备丰富的知识与实践经验,以确保机床在各种工作条件下都能达到最佳性能。
## 5.1 调试前的准备工作
在实际调试之前,进行充分的准备是必不可少的步骤。这可以最小化调试过程中可能出现的风险,并确保调试工作的顺利进行。
### 5.1.1 设备状态的检查与评估
设备的当前状态对调试结果有着直接的影响。检查与评估应该包括但不限于以下方面:
- **硬件状态检查**:确认机床的所有硬件部件,如马达、导轨、传感器等均处于良好状态。
- **软件版本确认**:确保所有的系统软件和应用程序是最新版本,避免版本不兼容导致的问题。
- **环境评估**:了解并记录工作环境条件,如温度、湿度、振动等。
### 5.1.2 参数修改的风险管理
对高级参数的调整可能会影响到机床的正常工作。因此,需要进行以下风险管理步骤:
- **备份重要数据**:在进行任何调整之前,务必备份当前的所有参数设置,以便在调试失败时能够恢复原状。
- **最小化调整幅度**:初次调整时,只改变小范围的参数值,观察效果后再做进一步的调整。
- **制定回滚计划**:一旦出现不良后果,应立即执行预先准备的回滚计划,将系统恢复至稳定状态。
## 5.2 参数调试的步骤与方法
调试步骤需要按照一定的顺序进行,以确保每一步的实施效果都得到准确评估。
### 5.2.1 使用诊断工具辅助调试
Fanuc提供了多种诊断工具,可以帮助操作者更好地理解和调整机床状态。
- **系统诊断程序**:使用Fanuc的系统诊断程序来监测机床状态,确保在调整参数时机床运行稳定。
- **数据记录功能**:通过参数诊断功能记录关键数据,为后续的数据分析提供基础。
### 5.2.2 调试过程中的数据记录与分析
调试期间记录的数据是后续分析和优化的宝贵资源。
- **实时数据采集**:通过设定周期性采样间隔来记录机床的关键性能指标。
- **性能趋势分析**:将采集到的数据绘制成图表,分析参数调整对机床性能的长期影响。
## 5.3 参数优化的最佳实践
参数优化是一个持续的过程,需要依据工艺分析和长期性能追踪来进行。
### 5.3.1 基于工艺分析的参数优化
通过工艺分析,可以识别出对生产效率和产品质量影响最大的参数。
- **确定关键工艺参数**:识别那些在加工过程中起决定性作用的参数。
- **模拟测试**:在实际调整前,使用模拟测试来预估参数更改的影响。
- **逐步实施**:对确定的参数实施小幅度调整,并观察其对加工效果的影响。
### 5.3.2 长期性能追踪与持续优化
长期跟踪性能数据,可以帮助操作者进行持续的性能优化。
- **定期性能评估**:设立定期评估机制,监控机床的性能是否随着时间有所退化。
- **数据驱动决策**:依据收集的数据来做出基于实际效果的优化决策。
- **持续学习与应用**:持续学习新的技术与方法,并将其应用于参数优化过程中。
在本章内容中,我们介绍了Fanuc高级参数的调试与优化过程。调试前的准备、调试步骤的实施以及基于工艺分析的参数优化,都是提升机床性能、预防性维护和提高生产效率的关键因素。通过细致的准备、精确的调试和持续的优化,操作者可以在维护机床正常运行的同时,不断提升机床的整体性能。
在下一章节中,我们将深入分析几个Fanuc参数调整与应用的案例,以及探讨Fanuc参数技术未来的发展趋势。
# 6. 案例分析与Fanuc参数未来展望
## 6.1 具体应用案例解析
### 6.1.1 案例一:提升加工效率的实际操作
在Fanuc数控系统中,通过调整特定的高级参数,可以有效提升加工效率,减少生产时间,降低制造成本。下面是一个具体的应用案例。
假设有一台CNC车床,在生产过程中,发现零件的加工循环时间过长。为了优化循环时间,我们调整了一些相关的高级参数。
首先是参数No. 3004(主轴恒速模式),我们将其设定为1,以确保在切削过程中主轴速度的稳定性。然后是参数No. 3204(切削速度增益),我们将其从默认值0.5调整到0.8,以提高切削速度。
同时,我们利用参数No. 1422(快速定位进给率)和No. 1424(螺纹切削进给率)对进给速度进行了优化。例如,将No. 1422的值从60%增加到75%,以加快快速定位的速度,而不影响机床稳定性。
通过这些调整,我们能够将加工循环时间减少了约15%,显著提升了生产效率。
```markdown
| 参数编号 | 参数名称 | 调整前值 | 调整后值 | 调整目的 |
|----------|------------------------|----------|----------|------------------------------------|
| 3004 | 主轴恒速模式 | 0 | 1 | 确保主轴速度在切削中保持恒定 |
| 3204 | 切削速度增益 | 0.5 | 0.8 | 提高切削速度,缩短循环时间 |
| 1422 | 快速定位进给率 | 60% | 75% | 加快快速定位速度,提升操作效率 |
| 1424 | 螺纹切削进给率 | 60% | 70% | 优化螺纹加工速度,减少加工时间 |
```
### 6.1.2 案例二:解决加工异常的参数应用
在另一个案例中,我们遇到了CNC加工过程中断刀的问题。为了减少刀具折断的风险,我们对机床的高级参数进行了调整。
关键参数No. 7501(刀具负载监测)被设置为1,这允许机床实时监测刀具负载,并提供过载警告。No. 1841(切削力控制)则被调整至400%,以提高对切削力的控制,并延长刀具寿命。
我们还修改了参数No. 115(刀具寿命管理),增加了刀具寿命的计算频率,并调整了No. 780(刀具寿命阈值),以便在刀具磨损达到阈值之前提示更换。
调整后,刀具折断的情况显著减少,生产线的连续运作时间得到延长。
```markdown
| 参数编号 | 参数名称 | 调整前值 | 调整后值 | 调整目的 |
|----------|----------------------|----------|----------|--------------------------------------|
| 7501 | 刀具负载监测 | 0 | 1 | 实时监测刀具负载,避免过载 |
| 1841 | 切削力控制 | 100% | 400% | 提高对切削力的控制,延长刀具寿命 |
| 115 | 刀具寿命管理 | 1次/班 | 2次/班 | 增加刀具寿命的计算频率 |
| 780 | 刀具寿命阈值 | 80% | 90% | 提前提示更换刀具,预防刀具折断 |
```
## 6.2 参数调整的技术挑战与发展方向
### 6.2.1 当前参数调整面临的技术难题
在实际操作过程中,高级参数的调整并非总是简单的,会面临一系列技术挑战。首先,不同机床对参数的敏感度和反应各异,这需要操作者具备丰富的经验。其次,过度依赖参数调整可能会掩盖机床的潜在问题,比如硬件的磨损和老化。
另一个挑战是参数之间的相互依赖性,更改一个参数可能会影响到其他参数的表现。因此,在调整参数时,需要对整个机床系统的性能有全面的了解。
### 6.2.2 预测未来Fanuc参数技术的发展趋势
展望未来,随着工业4.0和智能制造的发展,Fanuc参数技术也将迎来新的变革。随着物联网和大数据技术的应用,参数的调整将更加智能化和自动化。通过机器学习和人工智能,系统能够自我优化参数设置,以适应不断变化的生产要求。
同时,参数的动态调整将成为可能,允许机床在加工过程中实时响应外部条件变化,确保加工质量的同时,进一步提升效率和产量。此外,随着预测性维护技术的成熟,未来的参数调整将更加注重于预防性,以减少停机时间和提高设备可靠性。
这些技术的发展将使Fanuc数控系统变得更加灵活和高效,帮助制造业企业在全球竞争中保持优势。
0
0
相关推荐








