圆坯连铸机特点与技术发展:效率提升与节能
需积分: 0 55 浏览量
更新于2024-08-22
收藏 27.79MB PPT 举报
圆坯连铸机是连续铸钢工艺中的关键设备,其特点是结合了现代钢铁生产技术的诸多优势。以下是圆坯连铸机的主要特点:
1. 结晶器设计:结晶器的锥度对铸坯质量有直接影响。对于直径小于200mm的铸坯,一般采用1%的锥度,而对于直径更大的铸坯,如含碳量较低,由于铸坯收缩明显,会选择1.2%的较大锥度。反之,含碳量高的铸坯收缩不明显,则可选用较小锥度,以确保铸坯的均匀冷却。
2. 二冷区:二冷区是冷却铸坯的关键部分,通常采用弱冷方式,即比水量在0.3~0.8升/公斤钢,确保铸坯在矫直前得到适当的冷却,同时避免过快冷却导致的裂纹。矫直温度也被严格控制在1000℃以下。
3. 拉矫机:采用多点矫直技术,能够更精确地控制铸坯的形状和尺寸,减少变形和内部应力,提高铸坯的平直度。
4. 切割机:切割机通常采用火焰切割的方式,对铸坯进行精准切割,以适应后续的深加工和产品需求。
5. 冷床:冷床采用步进式设计,能够连续输送冷却后的铸坯,进一步提高生产效率。
6. 连续铸钢的发展历程:自二十世纪五十年代起,随着德国、苏联、英国等国的相继突破,连铸技术逐渐成为主流,不仅提高了金属收得率和产品质量,还推动了钢包冶金技术、结晶器自动化控制等技术的进步。进入九十年代,连铸技术进入新阶段,包括近终形连铸、高速浇铸等新型工艺不断涌现。
7. 我国连铸技术发展:从早期的试验研究到实际应用,我国在连续铸钢技术方面也取得了显著进步,比如在重钢和唐钢建设的连铸机,显示了我国在这领域的技术实力。
8. 连铸技术的优势:除了节省工序、提高收得率和降低能耗外,连铸还促进了生产过程的机械化和自动化,提高了劳动生产率,并且能够满足多品种、高质量的产品需求。
9. 提高连铸机作业率的技术:为了进一步提升连铸机的效率,业界不断研发新技术,如多炉连烧技术、设备长寿命技术、防漏钢稳定化操作以及减少非浇注时间的维护操作等,这些都为连铸工艺的持续优化做出了贡献。
总结来说,圆坯连铸机是连铸技术的核心设施,它的特点和不断发展的工艺为钢铁工业带来了显著的效益和竞争力。随着科技的进步,未来连铸技术将继续朝着更高精度、更环保和更高效的生产模式发展。
2021-12-03 上传
2024-05-19 上传
2022-04-06 上传
点击了解资源详情
2022-07-02 上传
2023-04-20 上传
点击了解资源详情
点击了解资源详情
点击了解资源详情
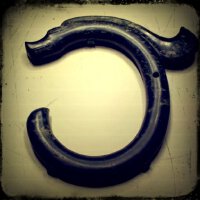
劳劳拉
- 粉丝: 21
- 资源: 2万+
最新资源
- Raspberry Pi OpenCL驱动程序安装与QEMU仿真指南
- Apache RocketMQ Go客户端:全面支持与消息处理功能
- WStage平台:无线传感器网络阶段数据交互技术
- 基于Java SpringBoot和微信小程序的ssm智能仓储系统开发
- CorrectMe项目:自动更正与建议API的开发与应用
- IdeaBiz请求处理程序JAVA:自动化API调用与令牌管理
- 墨西哥面包店研讨会:介绍关键业绩指标(KPI)与评估标准
- 2014年Android音乐播放器源码学习分享
- CleverRecyclerView扩展库:滑动效果与特性增强
- 利用Python和SURF特征识别斑点猫图像
- Wurpr开源PHP MySQL包装器:安全易用且高效
- Scratch少儿编程:Kanon妹系闹钟音效素材包
- 食品分享社交应用的开发教程与功能介绍
- Cookies by lfj.io: 浏览数据智能管理与同步工具
- 掌握SSH框架与SpringMVC Hibernate集成教程
- C语言实现FFT算法及互相关性能优化指南