“α”风险界定与SPC分析:新手入门到专家级掌握
发布时间: 2024-12-19 18:13:25 阅读量: 4 订阅数: 4 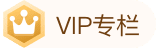
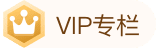
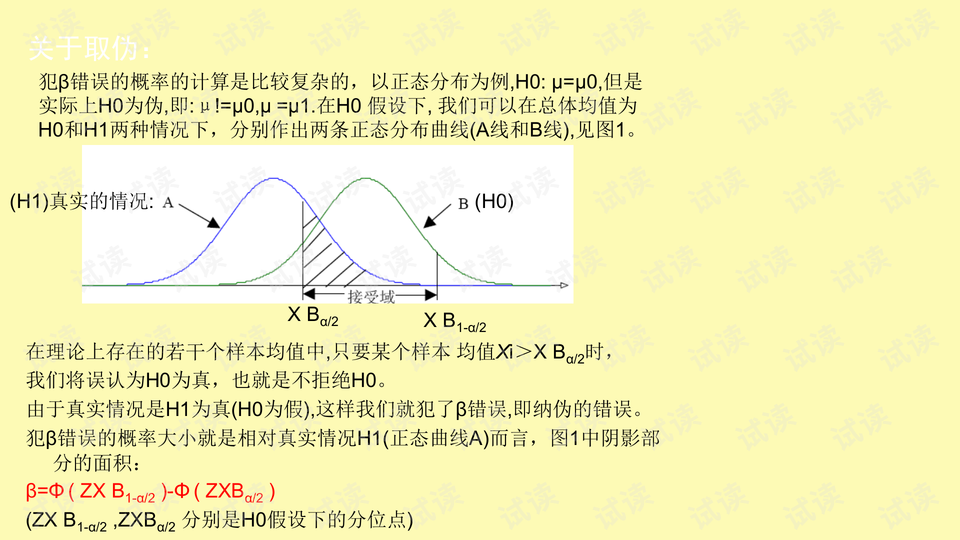
# 摘要
风险界定与统计过程控制(SPC)是确保生产和质量控制中稳定性与一致性的关键工具。本文从α风险的理论基础出发,深入探讨了α风险在统计学中的定义、重要性以及如何在假设检验中应用,并讨论了α错误的控制。随后,文章介绍了SPC的理论框架,包括其核心概念、控制图理论和过程能力分析。在实践应用方面,本文分析了α风险在制造业的实际应用案例,并探讨了SPC在质量控制中的实际运用,提出结合α风险与SPC的策略。最后,探讨了SPC的高级技术如多变量SPC和实时SPC,以及SPC在六西格玛方法论中的融合,并对α风险与SPC的未来趋势进行了展望,特别强调了智能制造、人工智能和大数据技术的潜在应用。
# 关键字
风险界定;统计过程控制;α风险;假设检验;过程能力分析;质量控制;六西格玛
参考资源链接:[SPC统计过程控制与α风险详解](https://wenku.csdn.net/doc/5me64w15y3?spm=1055.2635.3001.10343)
# 1. 风险界定与统计过程控制(SPC)概述
在当今快速发展的商业和技术环境中,产品质量与流程效率成为了企业竞争力的关键所在。为了确保这些关键要素,企业必须采取科学的方法来界定风险并实施有效的质量控制。本章将概述风险界定的重要性以及统计过程控制(SPC)的基本概念。
## 1.1 风险界定的重要性
风险界定是识别和评估潜在风险并决定如何应对的过程。它不仅有助于避免或减轻负面后果,而且还能帮助企业确定风险承受的界限。在质量控制领域,风险界定帮助我们理解哪些变量可能影响产品质量,并指导我们采取何种措施来管理这些变量。
## 1.2 统计过程控制(SPC)简介
统计过程控制(SPC)是一种使用统计方法对生产过程进行监控和控制的技术。它基于对过程输出的持续测量,并利用控制图和其他统计工具来评估过程稳定性。通过SPC,企业能够预测并提前解决质量问题,实现持续的质量改进。
## 1.3 SPC与风险管理的关系
SPC在风险管理中的作用不容忽视。通过监控关键质量指标,SPC能够帮助识别过程中的异常波动,即潜在风险的信号。及时识别并纠正这些波动,可以减少质量缺陷的发生,从而降低由于产品质量问题而导致的风险。因此,SPC不仅是质量控制的重要工具,也是风险管理战略的核心组成部分。
# 2. α风险的理论基础
## 2.1 α风险的定义与重要性
### 2.1.1 α风险在统计学中的角色
α风险,也称为第一类错误,是指在统计假设检验中,当原假设实际上是真的,却被错误地拒绝了的风险。在质量管理和统计分析中,这种错误导致了错误的结论,可能会引发不必要的进一步调查或过程调整。α风险的控制对于维持统计测试的可靠性至关重要。
### 2.1.2 α风险与决策过程的关系
在决策过程中,α风险的存在会直接影响到决策的准确性和效率。例如,在产品测试中,如果α风险设定得过高,那么许多不合格的产品可能会被误判为合格,反之亦然。这表明,α风险需要根据具体情境进行细致的评估和调整,以确保其对决策的影响最小化。
## 2.2 α风险的统计学基础
### 2.2.1 假设检验与α风险
在进行假设检验时,α风险被设定为检验标准的显著性水平(α)。标准的假设检验流程包括设定原假设(H0)和备择假设(H1),然后选择一个统计测试和相应的显著性水平(通常为0.05或0.01)。测试结果要么拒绝原假设,要么不拒绝原假设,前者可能涉及到α风险的发生。
### 2.2.2 α错误的影响和控制
α错误的影响可大可小,取决于其发生的后果。为了控制α风险,可以通过增加样本量来降低犯α错误的概率,或者调整显著性水平来减小错误决策的可能性。在某些情况下,如果α错误的后果非常严重,可能需要将显著性水平设置得更低,如0.001或0.0005。
## 2.3 α风险的计算方法
### 2.3.1 理论框架与公式推导
α风险的计算涉及到统计分布的理解,如正态分布、t分布、卡方分布等。对于简单的假设检验,如单一样本均值检验,其α风险可以通过查阅相关统计分布表来确定。对于更复杂的模型,可能需要借助统计软件来计算。
### 2.3.2 实际案例中的α风险计算
在实际案例中,α风险的计算通常涉及将样本数据与假设进行比较,并计算出拒绝原假设的概率。例如,在控制图中,如果一个样本点落在了控制限之外,根据控制图的类型,我们可以确定这种情况发生的概率,并据此判断是否发生了α错误。
在制造业的质量控制过程中,控制图是监控和评估过程稳定性和能力的一个重要工具。例如,在使用X-bar(均值)和R(极差)控制图时,如果计算出的点落在控制限之外,我们可能需要计算这个事件发生的概率,以此来判断是否应该将α风险考虑在内。
```mermaid
graph TD
A[开始] --> B[数据收集]
B --> C[计算样本统计量]
C --> D[确定控制限]
D --> E{点是否在控制限外?}
E -->|是| F[计算超出概率]
E -->|否| G[过程处于控制状态]
F --> H[判断α风险]
H --> I[采取相应措施]
I --> J[结束]
```
控制图上的点超出控制限的概率可以通过特定的统计检验来计算,如使用z检验或t检验。在实际操作中,通过使用统计软件,如R或Python,可以快速计算出超出控制限的α风险。
```python
from scipy.stats import norm
# 示例:计算超出控制限的概率(z检验)
alpha = 0.05 # 显著性水平
z = 2.576 # 正态分布的z值(对应于上尾0.005)
p_value = 1 - norm.cdf(z) # 计算概率
print(f"超出控制限的概率: {p_value}")
```
以上代码展示了一个计算超出控制限概率的简单例子。通过计算,我们可以对α风险有一个量化的认识,从而在质量管理和统计测试中作出更加明智的决策。
# 3. 统计过程控制(SPC)的理论框架
在探讨统计过程控制(SPC)的过程中,理解其理论框架对于任何质量控制专业人员来说都是至关重要的。本章将深入探讨SPC的基本概念、控制图理论和过程能力分析,这些内容是SPC实施过程中不可或缺的理论基础。
## 3.1 SPC的基本概念与目的
### 3.1.1 SPC的定义和核心原则
统计过程控制(SPC)是运用统计学原理对生产过程进行监控和控制的一种方法。其核心原则是通过收集生产过程中的数据,分析并识别过程中存在的差异,以实现持续改进产品质量的目的。SPC强调的是对过程的控制,而不是仅仅对最终产品的检验。
SPC利用诸如控制图、直方图、散点图等统计工具,来监控和调整生产过程,使其尽可能地稳定在设定的性能指标范围内。这样不仅能够预防缺陷的发生,还能在问题出现时立即采取纠正措施。
### 3.1.2 SPC与质量改进的关系
SPC与质量改进密切相关,是推动质量持续改进的重要手段。通过监控过程变异,SPC有助于识别过程中的非随机变异,即异常波动,这些波动往往是生产过程中出现问题的信号。质量改进的目的是减少或消除这些非随机变异,从而提高过程的一致性和产品的质量。
SPC的实施不仅可以提高产品质量,还可以为企业带来经济上的好处。例如,通过减少浪费和提升效率,降低产品不良率和返工率,最终实现成本节约。
## 3.2 SPC中的控制图理论
### 3.2.1 控制图的类型与选择
控制图是SPC中非常重要的工具,它通过图形化的方式来展示过程数据随时间变化的情况,并帮助识别出数据是否处于控制状态。控制图的类型多种多样,常见的有X-bar & R图、X-bar & S图、p图、np图、c图和u图等。
选择合适的控制图类型对于有效地监控过程至关重要。例如,连续数据通常使用X-bar & R图或X-bar & S图,而属性数据(如不合格品数量)则可能需要使用p图或np图。选择控制图时要考虑数据的类型(连续或离散)、样本大小、过程特性等因素。
### 3.2.2 控制限的设置与解读
控制图上包括了控制限(也称为控制线),通常包括上控制限(UCL)、下控制限(LCL)和中心线(CL)。上控制限和下控制限通常基于过程的历史数据计算得出,用以界定过程的统计控制状态。
当数据点落在控制限内时,可以认为过程处于统计控制状态,即没有出现异常波动。相反,如果数据点超出控制限,或显示出非随机的模式(如连续的点上升或下降),则认为过程存在特殊原因引起的波动,需要进一步分析原因并采取相应的纠正措施。
## 3.3 SPC中的过程能力分析
### 3.3.1 过程能力指数Cp和Cpk
过程能力指数(如Cp和Cpk)是衡量过程满足规格要求能力的统计量。Cp值越高,表示过程越能生产出符合规格要求的产品。Cp指数不考虑过程平均值的位置,仅仅关注过程输出的离散程度;而Cpk是考虑了过程中心位置的过程能力指数,它结合了过程的偏移和散度来评估过程能力。
简单来说,Cp是理想状态下的能力,而Cpk是实际状态下的能力。当Cpk大于1时,表明过程能够稳定地生产出符合规格的产品,反之则说明过程需要调整。
### 3.3.2 过程能力的评估与改进
过程能力评估是SPC实施的重要环节,它有助于识别过程是否能够满足设计规格要求。评估过程能力的步骤通常包括确定规格限、收集和分析数据、计算过程能力指数等。
若过程能力不足,就需要采取相应的改进措施。这可能包括调整生产过程、改变原料或重新设计产品。改进的目标是使过程的平均值尽可能接近目标值,且变异尽可能小,这样可以最大程度地减少缺陷并提高产品质量。
接下来,我们将详细探讨α风险与SPC的实践应用,以及如何将这些理论知识应用于实际案例,以及在现实世界中如何进行风险评估和质量控制。
# 4. α风险与SPC的实践应用
## 4.1 α风险的实际应用案例分析
在探讨α风险的实际应用时,我们通过特定的行业案例来说明α风险在实践中如何被识别、评估和管理。下面,我们以制造业为例,深入了解α风险的行业应用以及实验设计中如何控制α风险。
### 4.1.1 行业应用:制造业中的α风险管理
在制造业,α风险通常与过度校正过程、减少产品质量的波动性或不必要地拒绝一个良品有关。例如,一家汽车零部件制造商可能为了减少缺陷率而过度调整其生产线,这反而可能引入新的错误,增加制造成本和时间。
下面是一个制造业中α风险管理的实例,来展示如何在实际工作中识别和解决α风险问题。
**案例分析:汽车零部件制造过程中的α风险管理**
假设某汽车零部件制造厂在其生产过程中引入了新的质量控制手段,目的是减少不合格产品的数量。厂方采用了严格的尺寸检测标准,但最终检测结果导致了许多本来合格的产品被错误地标记为不合格,从而被拒绝接收或返工。这一过程显著增加了成本,并导致交货延迟。
通过分析,厂方发现原检测标准设置过严,导致了过多的α错误(假阳性),即错误地将合格品判定为不合格品。此时,制造业面临的挑战是如何重新评估质量控制标准,以找到平衡点,既能保障产品质量,又能减少不必要的α错误。
经过调整检测标准,并使用统计分析来监控生产过程后,该厂成功地将α风险维持在一个较低且可接受的水平。这不仅提高了整体的生产效率,而且保证了质量控制的合理性和有效性。
### 4.1.2 实验设计与α风险的控制
实验设计是控制α风险的重要环节。良好的实验设计能够在测试开始之前就预先定义好决策规则,从而减少α风险。
**实验设计流程:**
1. **定义实验目标**:明确实验想要回答的问题,以及实验的具体目标。
2. **选择合适的样本**:确保样本具有代表性,可以有效代表整个生产过程或产品批次。
3. **控制变量**:在实验中严格控制干扰变量,确保实验结果的准确性和可靠性。
4. **统计分析与决策**:使用统计方法来分析实验数据,为决策提供依据。
5. **结果验证**:实验结束后,需要验证结果是否具有统计显著性,同时考虑α风险的影响。
在控制α风险时,一个关键的统计工具是假设检验。通过设定原假设和备择假设,可以计算出p值来评估数据是否支持原假设。在制造业中,决策者可以设定一个显著性水平(如α = 0.05),以确定接受或拒绝原假设的依据。
## 4.2 SPC在质量控制中的实践
统计过程控制(SPC)是一种用于监控和控制生产过程的统计工具,其核心在于使用控制图来识别过程中的特殊变异,即非随机的、异常的变化,从而保证生产过程的稳定性和产品质量的一致性。
### 4.2.1 数据收集与分析方法
在SPC实践中,数据收集是至关重要的一步,它直接关系到控制图的有效性。数据收集应按照以下原则进行:
- **及时性**:数据收集应当在生产过程中实时或接近实时进行,以便于快速发现过程异常。
- **准确性**:确保数据的准确无误,避免人为或设备误差。
- **代表性**:收集的数据应能代表整个生产过程的变异情况。
**数据收集与分析方法步骤:**
1. **定义数据收集点**:根据过程流和关键质量属性确定数据收集的频率和位置。
2. **选择合适的数据类型**:决定是收集属性数据(如合格/不合格)还是变量数据(如尺寸、重量等)。
3. **使用SPC软件或工具**:利用统计软件进行数据分析,例如Minitab、JMP、SPSS等。
4. **绘制控制图**:根据收集到的数据绘制控制图,如X̄-R图(均值-极差图)或X̄-S图(均值-标准差图)。
### 4.2.2 控制图的绘制与监控
控制图是SPC中的核心工具,它通过统计方法显示过程的变化,帮助我们区分是偶然变异还是非偶然变异。
**控制图绘制步骤:**
1. **确定过程控制限**:计算平均值、标准差,并基于这些统计量设定控制限。
2. **绘制中心线**:通常为平均值。
3. **绘制控制限**:上下控制限为平均值加减三倍标准差。
4. **分析控制图**:定期查看控制图,分析点的分布,识别特殊原因引起的变异。
下面是一个控制图的示例代码块,以Python的`matplotlib`和`numpy`库为例:
```python
import numpy as np
import matplotlib.pyplot as plt
import statsmodels.api as sm
# 模拟一组随机数据
np.random.seed(0)
n = 50
data = np.random.normal(0, 1, n)
# 计算均值和标准差
mean = np.mean(data)
std_dev = np.std(data)
# 创建控制图
plt.figure(figsize=(10, 4))
plt.plot(data, 'o-', label='Sample Values')
plt.axhline(mean, color='r', linewidth=2, label='Central Line')
plt.axhline(mean + 3 * std_dev, color='g', linestyle='--', label='Upper Control Limit (UCL)')
plt.axhline(mean - 3 * std_dev, color='g', linestyle='--', label='Lower Control Limit (LCL)')
plt.title('SPC Control Chart Example')
plt.legend(loc='best')
plt.show()
```
**参数说明:**
- `mean`: 数据的平均值,用作控制图中心线。
- `std_dev`: 数据的标准差,用于确定控制限。
- `UCL` 和 `LCL`: 分别是控制图的上控制限和下控制限。
**逻辑分析:**
此代码块首先生成了一组模拟的生产过程数据,计算其均值和标准差,随后绘制了一个简单的控制图,其中包括样本值、中心线以及控制限。通过观察控制图,可以直观地判断生产过程中是否存在异常情况。
## 4.3 结合α风险与SPC的策略制定
结合α风险与SPC的实践应用,可以进一步优化质量控制流程。此部分将聚焦于风险评估与控制计划的制定,以及如何通过SPC实现质量改进和过程优化。
### 4.3.1 风险评估与控制计划
风险评估是识别、评价和优先处理风险的过程。在质量控制领域,风险评估需要综合考虑各种因素,包括过程能力、设备可靠性以及人员操作等。
**风险评估流程:**
1. **确定风险源**:识别可能影响产品质量的所有潜在风险因素。
2. **风险分析**:分析每个风险发生的可能性及其可能造成的影响。
3. **风险评价**:根据风险的严重性进行排序,并确定风险等级。
4. **制定风险控制计划**:基于风险评估结果,制定相应的控制措施和预防策略。
### 4.3.2 质量改进与SPC优化
质量改进是一个持续的过程,SPC技术在此过程中扮演着关键角色。通过实时监控和控制图分析,SPC可以帮助识别过程变异,为质量改进提供指导。
**质量改进与SPC优化策略:**
1. **实时监控与反馈**:通过实时SPC工具持续监控生产过程,快速响应过程变异。
2. **过程能力分析**:定期进行过程能力分析,确定过程是否能够稳定地生产满足质量要求的产品。
3. **持续改进活动**:使用SPC工具识别改进机会,如六西格玛DMAIC(定义、测量、分析、改进、控制)周期。
4. **培训与教育**:对员工进行SPC和质量意识培训,确保他们理解控制图的重要性并能正确应用。
本章节对α风险与SPC的实践应用进行了深入探讨,从实际应用案例分析到SPC在质量控制中的实践应用,最后到如何结合二者制定策略。通过这些内容,读者可以对α风险在真实工作环境中的识别和管理,以及SPC在质量控制中的具体应用有全面而深入的理解。接下来的章节将继续深入,探讨SPC的高级技术与方法,以及α风险与SPC的未来趋势与发展。
# 5. SPC高级技术与方法
## 5.1 多变量统计过程控制(MSPC)
### 5.1.1 MSPC的概念与应用
多变量统计过程控制(MSPC)是统计过程控制(SPC)的一个高级分支,它针对涉及多个相互关联过程变量的情况。在实际生产环境中,单一的质量特性往往受到多个过程变量的影响,例如,在汽车制造中,车辆的重量、尺寸和燃油效率可能同时受到多个生产过程参数的影响。MSPC通过同时考虑多个过程变量,更全面地监控和控制生产过程,从而提高产品质量和生产效率。
MSPC的关键技术包括多元统计方法,例如主成分分析(PCA)和偏最小二乘回归(PLSR)。这些方法能够降低高维数据的复杂性,帮助工程师识别关键的过程变量,并监测这些变量对产品质量的综合影响。MSPC通常使用控制图来展示多个变量的统计信息,如T2控制图和贡献图,以便于识别生产过程中的异常情况。
### 5.1.2 MSPC在复杂过程中的优势
MSPC在处理复杂生产过程中的优势在于其能够整合多个相关变量的信息,这对于识别系统性问题和采取全局优化措施至关重要。以下是MSPC在复杂过程中的几个关键优势:
1. **全局监控**: MSPC提供了一个全局的视角来监控整个生产过程,而不仅仅是单个的质量特性或变量。
2. **早期预警**: 通过对多个过程变量的综合分析,MSPC能够在问题发生初期就提供预警,从而减少损失。
3. **效率提升**: 通过减少监控和控制的复杂性,MSPC有助于提高操作人员的效率和生产过程的稳定性。
4. **成本节约**: 由于能够更精确地定位问题源头,MSPC有助于节约成本,降低返工和废品率。
5. **质量改进**: MSPC的应用有助于持续改进质量控制过程,满足质量管理和顾客需求的提升。
接下来,我们将通过一个案例来深入理解MSPC的实际应用,并展示如何构建有效的MSPC监控系统。
### 案例研究:多变量统计过程控制在电子制造中的应用
在电子制造行业中,产品质量受到多种因素的影响,例如温度、湿度、压力和原材料的质量。为了确保产品质量,一家电路板制造商决定采用MSPC来监控其生产过程。以下是实施MSPC的步骤:
1. **数据收集**: 首先,收集电路板生产过程中的关键过程参数,如温度、压力和生产时间等。
2. **数据预处理**: 对收集的数据进行标准化处理,并采用多元统计分析方法识别关键过程变量。
3. **模型建立**: 构建PCA模型,将高维数据降维为少数几个主成分。
4. **监控系统构建**: 利用T2统计量建立控制图,将PCA得分绘制成控制图,以便实时监控生产过程。
5. **异常识别与响应**: 通过控制图识别出的异常点来判断是否有生产过程失控的风险,并采取相应的调整措施。
通过MSPC的应用,该制造商能够更精确地控制生产过程,显著减少了电路板的缺陷率,并提高了客户满意度。
## 5.2 实时SPC与自动化监控
### 5.2.1 实时SPC的实现与效益
实时统计过程控制(实时SPC)是一种能够在生产过程中实时收集、分析数据并做出决策的技术。这种技术特别适用于要求快速响应的制造业和流程工业,实时SPC可以提供即时的反馈,帮助操作人员和生产工程师快速识别和解决过程中的问题。
实时SPC的实现主要依赖于三个核心组件:数据采集系统、实时分析工具和控制策略。数据采集系统负责收集各种生产参数和质量特性数据。实时分析工具则对这些数据进行分析,并通过控制图等可视化方式实时展现过程状态。控制策略是基于分析结果对生产过程进行调整和优化的行动计划。
实现实时SPC的效益包括:
- **即时性**: 实时监控生产过程,快速响应过程变差。
- **预测性**: 结合预测模型,能够预测可能出现的问题并提前采取措施。
- **灵活性**: 针对不同的生产需求和条件灵活调整控制策略。
- **持续改进**: 提供持续改进的依据,实现质量控制的闭环管理。
### 5.2.2 自动化工具在SPC中的应用案例
为了更好地理解实时SPC的实施和效益,我们来看一个自动化工具在SPC应用中的案例。某大型化工企业为了提高其生产过程的质量控制水平,决定引入实时SPC系统。
该化工企业面临的挑战包括高能耗、生产过程不稳定以及质量波动。为了应对这些挑战,企业采用了以下步骤实施实时SPC:
1. **自动化数据采集**: 引入先进的传感器和数据采集系统,实时收集反应器内的温度、压力和化学成分数据。
2. **实时监控平台**: 构建实时监控平台,使用实时SPC分析软件,如Control Chart和Fishbone Diagram等。
3. **控制策略优化**: 利用实时数据和分析结果,优化控制策略,如自动调整反应器的控制参数。
4. **持续改进循环**: 建立持续改进机制,通过实时反馈调整生产过程,实现质量的持续提升。
通过实施实时SPC,该企业实现了过程稳定性,减少了能耗,并提高了产品的质量一致性,从而在竞争中取得了优势。
## 5.3 SPC的持续改进与六西格玛
### 5.3.1 六西格玛方法论与SPC的融合
六西格玛(Six Sigma)是一种旨在减少产品或服务缺陷和提高效率的管理哲学和一套方法论。它的核心理念是通过减少缺陷率来优化流程,从而达到每百万机会中最多3.4个缺陷的目标。SPC作为一种强大的工具,与六西格玛方法论高度契合,其数据驱动和过程控制的特点为六西格玛项目的实施提供了坚实的技术基础。
将SPC与六西格玛融合的方法包括:
- **数据收集和分析**: 利用SPC的方法收集数据并进行详细的统计分析,以识别和量化过程变差。
- **流程优化**: 通过六西格玛的DMAIC(定义、测量、分析、改进、控制)框架,使用SPC工具来找出改善流程的方法,并实现稳定和优化。
- **控制图的持续使用**: 在改进阶段后,持续使用控制图监控过程,确保流程改进的成果得以保持。
### 5.3.2 案例研究:SPC在六西格玛项目中的角色
在一次六西格玛项目中,一家汽车零部件制造商希望减少其生产过程中零件缺陷的发生。以下是该项目中SPC的应用案例:
1. **定义阶段**: 明确了要减少的缺陷类型,并定义了项目范围和目标。
2. **测量阶段**: 利用SPC工具收集了生产过程中的关键质量特性数据,如尺寸和表面光洁度。
3. **分析阶段**: 对收集的数据进行分析,识别出影响缺陷的关键过程变量,使用控制图和其他统计工具如散点图等进行进一步的探索。
4. **改进阶段**: 依据分析结果,设计了实验来测试改进措施的效果。通过调整过程参数,显著降低了缺陷率。
5. **控制阶段**: 改进后的流程通过了稳定性测试,并且在控制图上表现出控制状态。建立了过程监控计划,确保持续控制过程并维持成果。
通过与六西格玛方法论的融合,SPC不仅帮助团队减少了过程中的缺陷,而且实现了流程的稳定性和可预测性,从而降低了成本并提高了客户满意度。
以上章节展示了SPC高级技术与方法,包括多变量统计过程控制(MSPC)、实时SPC与自动化监控以及SPC的持续改进与六西格玛的融合。每个部分都通过案例分析来加深对方法应用的理解,为实现更高级别的过程控制提供了实践指南。通过深入的分析和实际应用,SPC技术能够显著提升质量管理的效能,推动企业向更高的质量目标迈进。
# 6. α风险与SPC的未来趋势与发展
## 6.1 α风险的新兴理论与挑战
### 6.1.1 新数据环境下α风险的适应性
随着大数据和机器学习技术的发展,数据环境日益复杂化。在这样的背景下,传统的α风险理论需要进行相应的调整和创新以适应新的数据环境。例如,对于大规模数据集,α风险的控制需要考虑数据的高维性以及潜在的相关性问题。高维数据意味着变量之间可能存在复杂的非线性关系,这将对α风险的评估和管理带来挑战。此时,传统的α风险计算方法可能不够高效,研究者和实践者需要开发新的算法,比如采用正则化方法来减少模型的复杂度,或者应用非参数统计方法来处理数据的非正态性。
### 6.1.2 跨领域中α风险的应用前景
在各个专业领域,α风险理论的应用前景是广阔的。例如,在金融领域,α风险与市场风险、信用风险的评估密切相关;在生物医学研究中,α风险影响着临床试验的可靠性和科学结论的有效性;在信息技术领域,特别是在人工智能算法中,α风险的控制对于提升算法的鲁棒性和公平性至关重要。随着α风险理论的不断进化,跨学科的结合将为风险管理带来更全面的视角和更高效的解决方案。
## 6.2 SPC技术的创新与发展方向
### 6.2.1 SPC技术在智能制造中的应用
智能制造是制造业转型升级的重要方向,而SPC技术在其中扮演着至关重要的角色。随着物联网、机器人技术以及云计算的集成应用,制造过程中的实时数据采集和处理变得更加可行。SPC技术可以实现对生产过程的实时监控,通过数据分析及时发现生产中的异常并进行调整,以减少缺陷和提高产品的质量一致性。在未来,随着数字孪生技术的发展,SPC技术将能够构建更加精确的生产模型,进一步提高生产效率和产品质量。
### 6.2.2 人工智能与大数据在SPC中的作用
人工智能(AI)与大数据的结合为SPC技术的发展带来了革命性的变化。AI技术,特别是机器学习和深度学习模型,能够处理和分析海量的生产数据,识别出生产过程中难以察觉的模式和异常。大数据分析使SPC能够从更大维度和更深层次挖掘数据价值,从而实现对生产过程的精准控制和优化。例如,通过使用AI预测模型,SPC可以基于历史数据预测未来可能出现的问题,并在问题发生之前采取预防措施。
## 6.3 风险管理与SPC的整合
### 6.3.1 综合风险管理框架的构建
在整合风险管理与SPC的过程中,构建一个综合的风险管理框架是至关重要的。这个框架需要将风险管理的各个环节——识别、评估、监控和应对,与SPC的各个步骤——数据收集、过程监控、异常检测和质量改进——有机地结合起来。框架应提供标准化的流程和工具,以确保风险管理与SPC的有效结合。通过这种方式,可以将风险管理的概念和方法应用到产品的全生命周期中,从而提高企业对内外部变化的响应速度和灵活性。
### 6.3.2 未来风险管理的展望与策略
未来风险管理将更加重视对复杂系统和动态环境的适应性,以及跨领域的协作和集成。企业需要制定灵活的风险应对策略,以应对不断变化的市场和技术挑战。此外,对于风险的定量分析将变得更加重要,尤其是在面对新型风险和未知风险时。为了实现这些目标,企业应投资于数据分析能力,加强员工的风险管理培训,并通过技术和流程的创新,加强企业自身的风险适应力和竞争力。
0
0
相关推荐
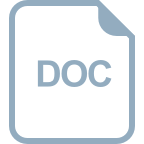
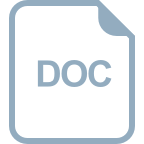
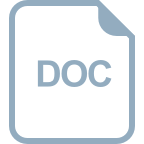
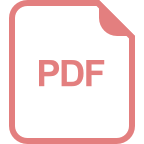
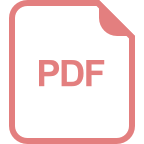
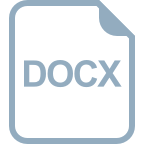
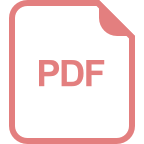