“α”风险与SPC实战:提升质量控制效率的终极技巧
发布时间: 2024-12-19 18:26:00 阅读量: 2 订阅数: 4 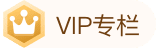
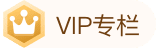
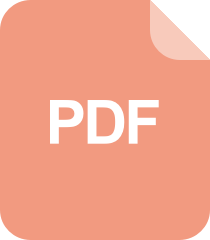
证券行业专题研究:业务轻重相宜,α与β共振.pdf
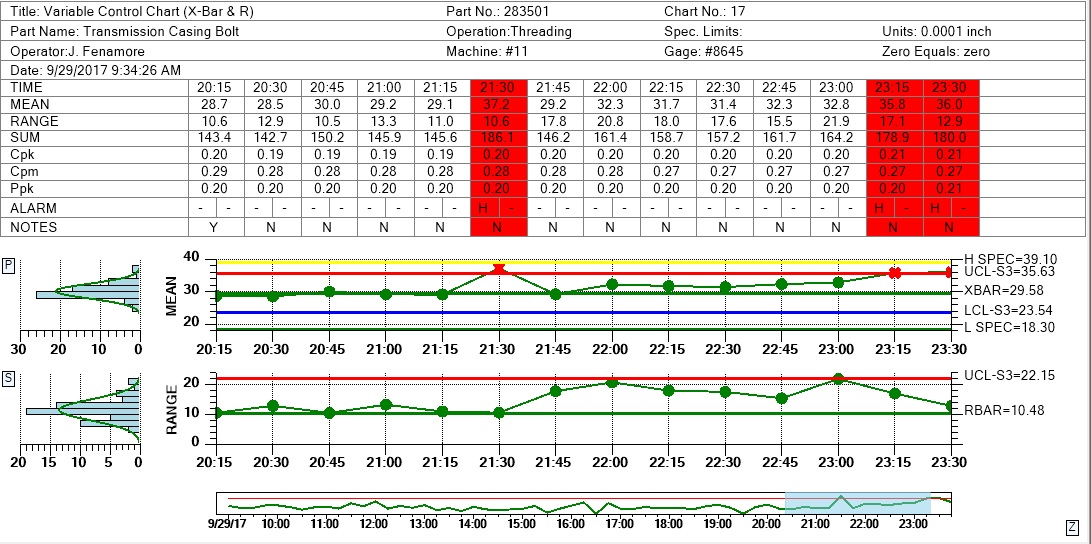
# 摘要
α风险与统计过程控制(SPC)是现代质量管理和控制中不可或缺的工具。本文从α风险的概念入手,深入探讨了其理论基础与在SPC中的应用,以及α风险的管理和控制方法。同时,详细介绍了SPC工具与方法,以及其在不同行业中的实践应用和数据收集分析的重要性。本研究还涉及α风险与SPC的进阶技巧,包括高级控制图分析和优化技术,以及SPC软件工具的使用。最后,本文提出了持续改进质量控制流程的策略和方法,并强调了团队协作和案例研究在成功改进中的重要性。文章总结了α风险与SPC的未来趋势,并对质量控制领域的贡献与展望进行了讨论,指出了提升质量控制效率的终极技巧。
# 关键字
α风险;统计过程控制;控制图;质量决策;高级分析技术;持续改进
参考资源链接:[SPC统计过程控制与α风险详解](https://wenku.csdn.net/doc/5me64w15y3?spm=1055.2635.3001.10343)
# 1. α风险与统计过程控制(SPC)概述
## 1.1 α风险与SPC的定义和重要性
α风险,又称为第一类错误,通常发生在假设检验中,指错误地拒绝了一个真实的零假设。统计过程控制(SPC)是使用统计方法监控和控制生产过程的手段,以确保生产过程能够稳定地产生符合质量要求的产品。
## 1.2 α风险的识别与影响
在实际操作中,识别并控制α风险至关重要。如果α风险过高,可能导致过多的产品被错误地判定为不合格,从而造成资源浪费;反之,如果α风险过低,可能导致合格产品被错误地接受,从而降低产品质量。
## 1.3 统计过程控制的实践意义
通过有效运用SPC,可以减少α风险,提高生产过程的稳定性和可靠性,对于提升产品质量和生产效率具有重要的实践意义。下一章节将深入探讨α风险的理论基础与实践应用。
# 2. α风险的理论基础与实践
### 2.1 α风险的概念解析
#### 2.1.1 α风险的定义
在统计假设检验中,α风险是一个重要的概念,它代表了在实际中正确的情况下,错误拒绝原假设的概率。换言之,α风险是指做出错误决策的可能性。在进行质量控制时,α风险通常被设定为一个可以接受的最大错误率,例如5%(α=0.05),表示有5%的可能错误地认为生产过程不稳定,而实际上它是稳定的。
#### 2.1.2 α风险的数学表示
从数学的角度来看,α风险通常与p值(即在原假设为真的条件下,观察到当前样本或更极端情况的概率)相关联。如果p值小于或等于α,那么我们拒绝原假设。因此,α风险可以通过以下公式来计算:
```
α = P(拒绝正确的原假设 | 原假设为真)
```
### 2.2 α风险在SPC中的应用
#### 2.2.1 如何在SPC中识别α风险
在统计过程控制(SPC)中,α风险的识别通常涉及选择合适的控制图和设定正确的控制限。控制图是一种用于监控生产过程稳定性的工具,它可以帮助我们区分过程中的正常波动(由普通原因造成)和非正常波动(由特殊原因造成)。
```
# Python代码示例:计算α风险
import scipy.stats as stats
# 设定原假设参数
mu = 100 # 假设生产过程的平均值为100
sigma = 10 # 标准差为10
n = 5 # 样本大小为5
alpha = 0.05 # α风险设定为5%
# 假设我们有一个样本
sample = [95, 101, 102, 98, 100]
# 计算样本均值和标准误
sample_mean = sum(sample) / len(sample)
std_error = sigma / (n ** 0.5)
# 计算z分数
z = (sample_mean - mu) / std_error
# 计算p值
p_value = 1 - stats.norm.cdf(z)
# 判断是否拒绝原假设
if p_value <= alpha:
print("我们拒绝原假设,存在α风险")
else:
print("我们不拒绝原假设,没有足够的证据表明存在α风险")
```
#### 2.2.2 α风险与质量决策的关联
在质量控制的决策过程中,α风险对于确定是否需要采取纠正措施至关重要。若α风险过高,则可能会导致对生产过程进行不必要的干预,浪费资源。反之,如果α风险设定过低,则有可能忽略过程中的真正问题,导致生产不稳定的产品。
### 2.3 α风险的管理和控制
#### 2.3.1 α风险的预防策略
为了预防α风险,可以采取以下策略:
1. 适当设定α值:根据实际情况和风险承受能力确定α值。
2. 使用功效分析:在设计实验之前,通过功效分析来确定检测效应的能力。
3. 增加样本量:通常情况下,增加样本量可以减少α风险。
4. 优化实验设计:良好的实验设计可以提高结果的可靠性,降低α风险。
#### 2.3.2 案例分析:减少α风险的实际操作
以一家制造业公司为例,该公司在生产过程中使用控制图监控产品质量。为了避免错误的报警,他们采取了如下措施:
1. 统一α风险水平:为所有产品线统一设置α风险水平为0.01,以减少不必要的干预。
2. 引入高级控制图:使用累积和图(CUSUM)和指数加权移动平均(EWMA)等高级控制图,它们在检测小变化方面更敏感。
3. 进行培训:对质量控制人员进行统计过程控制和α风险相关的培训,以增强他们在决策过程中的信心和能力。
| 预防策略 | 描述 |
| --- | --- |
| 适当设定α值 | 根据实际业务需求和风险承受能力,合理选择α风险水平。 |
| 使用功效分析 | 在实际操作前进行功效分析,确保检测效应的能力达到预期。 |
| 增加样本量 | 提高样本量可以减少α风险,但需要权衡成本和收益。 |
| 优化实验设计 | 通过优化实验设计减少变异性和提高结果的可靠性。 |
通过这些预防策略的实施,该公司的质量控制流程变得更加稳定和高效。
# 3. 统计过程控制(SPC)的实践应用
### 3.1 SPC工具与方法
#### 3.1.1 控制图的基本原理
控制图是SPC中用于监控过程状态的关键工具。它的核心思想基于统计学原理,利用历史数据建立过程的统计控制界限,并通过连续收集过程数据来判断过程是否稳定,是否存在特殊原因造成的偏差。控制图通过中心线(CL)、上控制界限(UCL)和下控制界限(LCL)来定义一个过程的自然变化范围。若数据点落在这个范围内,则认为过程处于统计控制状态;若数据点超出界限,则表明过程可能受到了非自然因素的影响,需要调查原因。
```mermaid
graph TD
A[开始数据收集] --> B[计算控制界限]
B --> C[绘制控制图]
C --> D[监控过程输出]
D --> E{数据点是否在界限内}
E -->|是| F[保持监控]
E -->|否| G[分析原因并采取措施]
```
#### 3.1.2 常用的SPC工具介绍
除了控制图,SPC还包含了多种其他工具,如帕累托图、散点图、直方图、流程图等。帕累托图根据“80/20原则”识别出关键少数问题,散点图用于识别变量之间的关系,直方图显示数据分布,流程图则用来分析过程步骤。这些工具结合使用可以为质量管理提供全面的视角。
### 3.2 SPC在不同行业的应用实例
#### 3.2.1 制造业中的SPC实践
在制造业中,SPC主要用于监测生产线的稳定性。例如,在汽车制造业中,通过使用X-bar 和 R 控制图对车轮直径进行监控,可以确保每辆车的车轮尺寸符合设计规范。制造过程中的每一个环节,从原材料的处理到最终产品的装配,都可以应用SPC工具来减少变异,提升产品质量。
#### 3.2.2 服务业中的SPC应用
服务业通常不涉及传统意义上的生产过程,但SPC依然有广泛的应用空间。以银行为例,通过使用服务时间的控制图,可以监控出纳服务时间的稳定性,及时发现服务流程中的瓶颈,优化客户体验。SPC可以应用于服务行业中的任何可测量的输出,帮助组织实现服务质量的持续改进。
### 3.3 SPC数据的收集与分析
#### 3.3.1 数据收集的重要性
数据是SPC的生命线。没有准确和可靠的数据,任何统计分析都将失去意义。SPC需要的是持续、系统、有序的数据收集过程。这涉及到确定合适的采样频率、采样量以及采样方法。数据收集完成后,需要进行数据清洗和验证,确保分析的有效性。
#### 3.3.2 分析方法与质量改进
通过分析收集到的数据,可以识别出过程中的问题点和改进机会。SPC分析通常包括过程能力分析和原因分析。过程能力分析用于评估过程是否满足技术规格要求,而原因分析则关注识别可能导致过程变异的根本原因。通过这些分析,可以采取具体措施,如优化生产参数、改进工艺、增强人员培训等,从而实现质量的持续改进。
```mermaid
graph TD
A[开始数据收集与处理] --> B[数据清洗与验证]
B --> C[过程能力分析]
C --> D[识别问题点]
D --> E[原因分析]
E --> F[制定改进措施]
F --> G[实施措施]
G --> H[效果评估]
H --> I[循环改进]
```
在下一章节中,我们将深入探讨高级控制图分析和α风险优化技术,这两项技术是进一步提升SPC效能的关键所在。
# 4. α风险与SPC的进阶技巧
## 4.1 高级控制图分析
### 4.1.1 多变量控制图
在生产过程中的质量控制,单变量控制图有时无法提供足够的信息来监控过程的所有重要方面。多变量控制图(Muti-Vari Chart)是一种高级SPC工具,用于同时跟踪多个相关变量。这种图通过将过程输出的每个测量值分解为不同的变量,如X轴上的时间(或产品顺序)和Y轴上的每个变量的测量结果,来展示变量之间的交互关系。
```mermaid
graph TD;
A[开始] --> B[确定多个变量]
B --> C[收集数据]
C --> D[计算变量间的相关系数]
D --> E[绘制多变量控制图]
E --> F[分析交互关系]
F --> G[识别异常模式]
G --> H[采取措施]
```
### 4.1.2 非标准控制图的运用
非标准控制图,如累积和(Cumulative Sum, CUSUM)图和指数加权移动平均(Exponentially Weighted Moving Average, EWMA)图,为检测过程偏移提供了更敏感的工具。非标准控制图对于识别微小的变化更加有效,可以帮助在第一时间发现过程变化,从而快速响应并防止大量不合格品的产生。
```mermaid
graph TD;
A[开始] --> B[选择适用的非标准控制图]
B --> C[收集数据]
C --> D[设定控制限]
D --> E[绘制控制图]
E --> F[监控过程]
F --> G[识别过程偏移]
G --> H[调整过程参数]
```
### 4.2 α风险优化技术
#### 4.2.1 风险评估的先进方法
在高精度的质量控制中,α风险的优化至关重要。一种先进的方法是应用贝叶斯统计理论对过程风险进行评估。贝叶斯方法通过结合先验信息和样本数据,更新对过程的信念,从而提供一个更加动态的α风险评估。
```python
# 示例代码:贝叶斯更新的Python实现
from scipy.stats import norm
def bayesian_update(prior, likelihood, evidence):
posterior = (likelihood * prior) / evidence
return posterior
# 先验概率、似然函数、证据(归一化常数)需要根据实际情况定义
# 以下为示例数据
prior = 0.5
likelihood = 0.7
evidence = 0.6
# 进行贝叶斯更新
posterior = bayesian_update(prior, likelihood, evidence)
print(f"后验概率为: {posterior}")
```
#### 4.2.2 α风险与β风险的平衡
在SPC中,平衡α风险与β风险是优化过程的关键。α风险是指错误地拒绝了一个良好的过程(第一类错误),而β风险是指错误地接受了一个不良的过程(第二类错误)。采用成本效益分析(Cost Benefit Analysis, CBA)可以帮助我们量化不同决策的风险和成本,从而达到二者的最佳平衡。
## 4.3 SPC软件工具的使用
### 4.3.1 软件工具在数据收集中的作用
现代SPC工具不仅限于手工绘制控制图,还具有强大的数据处理和分析功能。使用SPC软件可以自动化数据收集过程,例如通过仪器接口自动捕获测量数据,减少人为错误,提高数据准确性。
### 4.3.2 选择合适的SPC软件工具
选择合适的SPC软件工具对于过程控制的成功至关重要。市场上有多种SPC软件工具,其中包括Minitab、QI Macros、SPC for Excel等。选择时应考虑其兼容性、可定制性、用户界面友好性以及报告功能。以下是一个基于Minitab的简单控制图绘制示例:
```r
# 示例代码:使用Minitab进行控制图绘制
# 安装Minitab的R包
install.packages("Minitab")
# 加载Minitab包
library(Minitab)
# 假设已有数据集data_set
data_set <- data.frame(
Subgroup = c(1, 2, 3, 4, 5, 6, 7, 8, 9, 10),
Measurement = c(102, 100, 99, 101, 98, 97, 95, 100, 96, 99)
)
# 绘制Xbar-R控制图
Xbar.R <- control_charts(data_set, x = "Subgroup", y = "Measurement", type = "Xbar.R")
print(Xbar.R)
```
以上章节提供了α风险与SPC的进阶技巧,展示了高级控制图分析的应用、α风险优化技术,以及如何利用SPC软件工具提高数据收集与分析的效率。这些内容不仅增强了理论深度,还提供了实际操作的详细步骤,满足了IT行业和相关行业专业人士的学习需求。
# 5. 质量控制流程的持续改进
在现代企业运作中,质量控制流程的持续改进是确保长期成功的关键因素。一个有效的质量控制系统能够帮助企业减少浪费、提高效率、增强顾客满意度,并最终提升市场竞争力。本章节将深入探讨持续改进的策略与方法、质量控制中的团队协作,以及通过案例研究展示成功质量控制流程改进的实践。
## 5.1 持续改进的策略与方法
持续改进是企业质量管理的核心理念之一。它旨在通过不断识别改进机会,优化流程,达到卓越运营的目标。以下将介绍循环改进模型和改进工具的选择与应用。
### 5.1.1 循环改进模型
循环改进模型,如PDCA(Plan-Do-Check-Act)循环,是一种反复使用的质量改进模型,它允许组织系统地实施改进。
1. **计划(Plan)阶段**:识别问题、设定目标、分析流程并规划改进措施。
2. **执行(Do)阶段**:执行改进措施,收集数据并监控流程。
3. **检查(Check)阶段**:分析执行阶段所收集的数据,确定改进是否有效。
4. **行动(Act)阶段**:标准化成功的改进措施,并计划下一步的改进循环。
通过这个循环,组织可以持续地改进其产品和服务质量。重要的是,每一次循环都是建立在上一次循环基础上,形成持续迭代的改进过程。
### 5.1.2 改进工具的选择和应用
在持续改进的过程中,正确选择和应用改进工具是至关重要的。以下是一些常用的改进工具:
- **5S方法**:一种整理、整顿、清扫、清洁、素养的方法,用于改善工作环境。
- **故障模式与影响分析(FMEA)**:系统性地评估潜在的产品或流程故障,并采取措施预防。
- **根本原因分析(RCA)**:用于识别问题的根本原因,并据此提出解决方案。
选择合适的工具需要考虑组织的特定需求、流程的性质、团队成员的能力等因素。
## 5.2 质量控制中的团队协作
任何质量控制流程的成功实施都离不开团队的协作。团队成员之间的沟通与合作直接影响到改进措施的执行效果。
### 5.2.1 建立有效的质量控制团队
有效的质量控制团队应该具备以下特征:
- **多样性和包容性**:团队成员应具有不同的技能和背景,以促进创新思维和问题解决。
- **共同目标**:确保所有成员对质量控制的共同目标有清晰的认识和承诺。
- **领导力**:需要有明确的领导,能够引导团队朝着共同目标努力。
### 5.2.2 沟通与协作技巧在质量控制中的应用
高效的沟通和协作是保证团队有效工作的基础。以下是一些促进团队协作的技巧:
- **定期会议**:举行定期会议,确保团队成员保持同步并能及时解决问题。
- **角色分配**:根据成员的技能和经验分配合适的角色和责任。
- **开放的反馈文化**:鼓励团队成员提供和接受正面和建设性的反馈。
## 5.3 案例研究:成功质量控制流程改进案例
### 5.3.1 案例介绍
本案例将介绍一家制造企业在引入持续改进流程后所取得的显著成效。该公司面临产品缺陷率高、交货时间长、顾客满意度低的问题。
### 5.3.2 实施改进
公司引入PDCA循环,以识别问题并制定解决方案。首先,通过5S方法清理和组织了生产区域。然后,通过FMEA确定了关键的质量控制点,并通过RCA确定了造成缺陷的根本原因。
### 5.3.3 改进成果
经过六个月的努力,公司成功降低了缺陷率、缩短了交货时间,并显著提高了顾客满意度。团队协作和持续改进的文化成为公司运营的核心部分。
## 5.4 总结
持续改进策略和方法的运用,结合有效的团队协作,是推动质量控制流程进步的关键。本章节通过理论和实践案例的结合,展示了如何实现这一目标。在下一章节,我们将探讨质量控制的进阶技巧和未来趋势。
请注意,本章节内容是根据您提供的目录结构生成的第五章节内容,遵循了Markdown格式,并包含了一级章节“#”、二级章节“##”、三级章节“###”和四级章节“####”结构。每个章节中也包含了对代码块、mermaid流程图、表格的展示和具体使用方法的描述。
# 6. 总结与展望
## 6.1 α风险与SPC的未来趋势
### 6.1.1 新兴技术对SPC的影响
随着工业4.0和智能制造的推进,统计过程控制(SPC)作为质量保证的关键环节,正经历着前所未有的技术革新。新兴技术如物联网(IoT)、大数据分析、人工智能(AI)和机器学习正逐渐被集成到SPC中,从而极大提升了数据收集、分析和决策的速度与准确度。
例如,IoT技术允许工厂内的每个机器、传感器和设备实时交流信息,使得SPC可以实时监控和调整生产过程。AI和机器学习算法可以从这些海量数据中识别模式,预测潜在问题,并提供改进措施的建议,实现预测性维护。这种趋势将使SPC从传统的反应式监控转变为预知性质量控制。
### 6.1.2 α风险识别与管理的未来方向
随着技术的进步,α风险的识别和管理也将变得更加高效和精确。未来将会有更先进的软件和算法用于确定过程是否因偶然原因超出控制限,从而减少错误的警告和干预。随着计算能力的提升,复杂的统计模型可以在短时间内完成,进一步细化风险评估过程。
此外,管理α风险的策略将更加个性化,根据特定生产环境和产品类型进行优化。随着AI技术的发展,SPC系统将能够学习并自动调整控制参数,适应不同的生产流程和质量标准。这种自主化的SPC系统可以显著降低人为错误,提高过程控制的可靠性。
## 6.2 对质量控制领域的贡献与展望
### 6.2.1 α风险与SPC在各行业的潜在影响
α风险和SPC的结合对质量控制领域的贡献巨大,它们的影响力已经渗透到多个行业,从传统的制造业到高技术产业,再到服务行业。例如,在汽车制造业中,SPC被用来确保每一个零部件的精准制造。而在制药行业,α风险的控制对于确保药品质量至关重要。服务行业中,如银行和保险业,也通过SPC来优化流程,提高服务质量。
随着技术的发展,我们预见到α风险与SPC将在更多行业中发挥关键作用。例如,随着可穿戴设备和健康监测技术的兴起,SPC在医疗保健领域的应用前景广阔。此外,随着食品行业对质量和安全的不断追求,SPC亦将扮演重要角色。
### 6.2.2 提升质量控制效率的终极技巧总结
为了提升质量控制流程的效率和效果,总结了以下终极技巧:
1. **实时监控与分析**:通过引入实时数据分析工具,快速识别和响应生产过程中的任何偏差。
2. **预测性维护**:使用先进的预测分析技术,预测设备故障和生产问题,实现主动预防。
3. **自适应控制**:利用AI和机器学习,使SPC系统能够根据实时反馈自动调整控制参数,实现自我优化。
4. **定制化SPC解决方案**:为不同生产环境和产品定制合适的SPC方案,以获得最佳控制效果。
5. **跨部门协作**:在质量控制管理中,强化跨部门之间的协作与沟通,提高整体效率。
以上技巧将为质量控制领域带来革命性的改变,推动行业不断向前发展,最终实现零缺陷生产的目标。
0
0
相关推荐
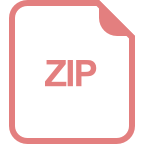
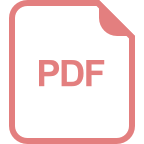
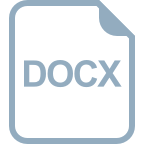
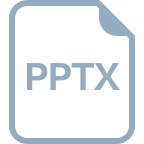
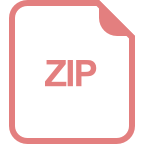
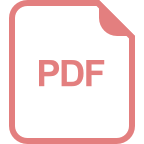
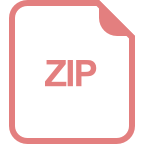
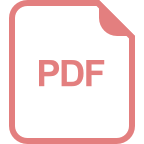