Practical Tips for Optimizing PWM Output Precision in Keil 5
发布时间: 2024-09-15 13:46:41 阅读量: 32 订阅数: 23 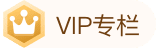
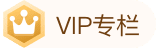
# 1. Overview of PWM Output Precision Optimization in Keil5
PWM (Pulse Width Modulation) is a modulation technique widely used in motor control, LED dimming, and audio signal generation. Keil5, as a popular embedded development environment, offers rich PWM output functionalities. However, in practical applications, PWM output precision is often affected by various factors, thereby affecting system performance and reliability. Therefore, optimizing PWM output precision is crucial.
This chapter will outline the importance of PWM output precision optimization, analyze the main factors affecting PWM output precision, and propose corresponding optimization strategies. By optimizing PWM output precision, system control precision can be improved, power consumption reduced, and system robustness enhanced.
# 2. Analysis of Factors Influencing PWM Output Precision
### 2.1 Impact of PWM Clock Frequency
PWM clock frequency is a key factor in PWM output precision. The higher the PWM clock frequency, the higher the PWM output precision. This is because a higher PWM clock frequency results in more precise PWM pulse widths.
For instance, if the PWM clock frequency is 100kHz, the minimum width of a PWM pulse would be 10μs. If the frequency is 1MHz, the minimum width would be 1μs.
### 2.2 Impact of PWM Resolution
PWM resolution is another key factor in PWM output precision. PWM resolution refers to the minimum variable width of PWM output pulses. The higher the PWM resolution, the higher the PWM output precision.
For example, if the PWM resolution is 8 bits, the minimum variable width of PWM output pulses would be 256 clock cycles. If the resolution is 16 bits, the minimum variable width would be 65,536 clock cycles.
### 2.3 Impact of PWM Interrupt Service Routines
PWM interrupt service routines are an important factor in PWM output precision. PWM interrupt service routines are responsible for updating PWM registers to generate PWM pulses. If the execution time of PWM interrupt service routines is too long, it could lead to inaccurate PWM pulse widths.
For instance, if the execution time of the PWM interrupt service routine is 10μs, the PWM pulse width might be 10μs wider than expected. If it's 100μs, the pulse width might be 100μs wider.
**Code Block:**
```c
void PWM_ISR(void)
{
// Update PWM registers
PWM_SetDutyCycle(duty_cycle);
// Clear PWM interrupt flag
PWM_ClearInterrupt();
}
```
**Logical Analysis:**
This code block is the PWM interrupt service routine. It is responsible for updating PWM registers to generate PWM pulses. The PWM_SetDutyCycle() function sets the duty cycle of the PWM pulse. The PWM_ClearInterrupt() function clears the PWM interrupt flag.
**Parameter Description:**
* duty_cycle: Duty cycle of the PWM pulse.
# 3. Practice of PWM Output Precision Optimization
### 3.1 Increasing PWM Clock Frequency
PWM clock frequency is a key factor influencing PWM ou
0
0
相关推荐








