Advanced Topics in MATLAB Control System Design: Adaptive and Learning Control
发布时间: 2024-09-15 01:06:15 阅读量: 30 订阅数: 30 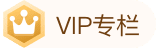
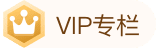
# 1. Fundamentals of Control System Design
Control systems are the core component of industrial automation and information technology development, and their design fundamentals have a decisive impact on the performance of the entire system. Before delving into adaptive control and learning control, we must have a comprehensive understanding of the structure, operating principle, and design methods of traditional control systems.
## 1.1 Components and Functions of Control Systems
Control systems mainly consist of three parts: sensors, controllers, and actuators. Sensors are responsible for collecting system status information, controllers process information according to predetermined control strategies and output control signals, and actuators respond to control signals to operate or adjust the system. The function of a control system is to ensure that the controlled object can operate in accordance with established goals, which usually involves performance indicators such as response speed, stability, and accuracy.
## 1.2 Design Principles of Control Strategies
An excellent control strategy should have good response characteristics and be able to adapt to the effects of environmental changes and internal disturbances of the system. Therefore, design principles generally include:
- System stability: The system should be able to maintain stable operation under various conditions.
- Rapid response: The system should quickly reach or maintain the desired operating state.
- Anti-disturbance ability: The system should have the ability to resist external and internal disturbances.
## 1.3 Control System Design Process
The development of a control system is an iterative optimization process, mainly including the following steps:
- Requirement analysis: Clarify control goals, system environment, and performance requirements.
- System modeling: Establish a mathematical model of the system based on requirements.
- Control strategy development: Select appropriate control algorithms and design controllers.
- System simulation: Simulate the response of the control system on a computer to verify the performance of the control strategy.
- Physical testing: Test the control system under real or semi-physical conditions, and perform tuning and adjustments.
In subsequent chapters, we will discuss in detail the theoretical foundations, design methods, and their practical application cases of adaptive control and learning control.
# 2. Adaptive Control Theory and Practice
## 2.1 Basic Concepts of Adaptive Control
### 2.1.1 Definition and Characteristics of Adaptive Control
Adaptive control is an advanced control strategy, the core of which is that the controller can automatically adjust control parameters according to changes in system performance. The main feature of this control strategy is its ability to dynamically respond to the uncertainties of the system and external disturbances, keeping the system in an optimal or near-optimal state.
In adaptive control theory, the following key characteristics are usually included:
1. **Parameter variability**: The parameters of the controller are not fixed but automatically adjusted based on the gap between the system's output and expected performance.
2. **System identification ability**: Adaptive controllers can identify or estimate changes in internal parameters of the system, such as mass, friction coefficient, inertia, etc.
3. **Feedback mechanism**: The control system includes a feedback loop that collects system output information in real-time for evaluating and adjusting control strategies.
### 2.1.2 Types and Application Scenarios of Adaptive Control
The types of adaptive control can mainly be divided into the following:
1. **Direct adaptive control**: The controller adjusts control parameters directly based on the system's performance feedback.
2. **Indirect adaptive control**: Estimates unknown system parameters through one or more parameter identifiers, then adjusts control inputs based on these estimated parameters.
3. **Model Reference Adaptive Control** (MRAC): Designs an expected reference model to set performance goals and makes the actual system match this reference model as closely as possible.
Application scenarios for adaptive control include but are not limited to:
1. **Industrial automation**: In automated production lines, equipment parameters may change due to long-term use; adaptive control systems can keep equipment operating at optimal conditions.
2. **Aerospace**: Aircraft and spacecraft may encounter uncertain airflow conditions during flight; adaptive control can help stabilize the flight and perform precise control.
3. **Robotics**: For robots executing complex tasks, the uncertainty of the environment and tasks requires the robot control system to be adaptive.
## 2.2 Adaptive Controller Design
### 2.2.1 Parameter Adaptive Control Algorithms
Parameter adaptive control algorithms achieve the adjustment of control inputs by online estimation of model parameters. Basic parameter adaptive control algorithms include the following steps:
1. **System model establishment**: Establish a system model and determine which parameters need to be adjusted.
2. **Parameter estimation**: Estimate these parameters in real-time by observing system outputs.
3. **Control input calculation**: Calculate new control inputs based on the estimated parameters.
A simple parameter adaptive algorithm can be represented as:
\[ \theta (t) = \theta (0) + \int_{0}^{t} \gamma(s)\frac{\partial f}{\partial \theta} \cdot e(s) \, ds \]
Where, \(\theta (t)\) is the parameter estimation at time \(t\), \(\gamma(s)\) is the adjustment gain, and \(e(s)\) is the error signal.
### 2.2.2 Model Reference Adaptive Control Strategies
Model Reference Adaptive Control (MRAC) strategies involve two models: one is the actual physical system model, and the other is the desired reference model. The goal of MRAC is to adjust the control parameters of the physical system so that its response matches the reference model.
The implementation steps of MRAC strategies usually include:
1. **Reference model selection**: Choose a well-performing reference model.
2. **Adaptive law design**: Design adaptive laws to adjust control parameters to achieve model following.
3. **Stability analysis**: Ensure that the entire adaptive control strategy is stable.
An important step in designing adaptive laws is determining the coefficients of the adaptive law, which typically requires using Lyapunov stability theory to ensure system stability.
### 2.2.3 Stability Analysis of Adaptive Control Systems
Stability analysis is at the core of adaptive control system design. The purpose of stability analysis is to prove that the system's state will converge to a stable state under the action of adaptive laws and that the system performance meets predetermined performance indicators.
Stability analysis generally includes the following methods:
1. **Lyapunov theory**: By constructing a Lyapunov function to prove that the system's energy function is decreasing, thus ensuring system stability.
2. **Barbalat lemma**: When the derivative of the Lyapunov function is bounded and the Lyapunov function tends to zero, the Barbalat lemma can be used to prove the stability of the system.
3. **Popov hyperstability**: For nonlinear systems, Popov's method can be used to analyze its hyperstability.
## 2.3 Practical Application Cases of Adaptive Control
### 2.3.1 Industrial Process Control Cases
In industrial processes, adaptive control can be used to improve production efficiency and product quality. For example, in chemical production, the control of reactor temperature and pressure is crucial for ensuring the correct progress of chemical reactions. Since the dynamic characteristics of the reactor may change due to temperature and pressure variations, traditional fixed-parameter controllers struggle to achieve precise control. Adaptive control can effectively adapt to these changes by adjusting control parameters in real-time, ensuring that the reactor operates at its optimal state.
In practice, adaptive controllers usually include an online identifier for real-time estimation of the system's dynamic parameters and adjust control inputs based on these parameters. While the system is running, the controller continuously monitors the actual values of temperature and pressure, compares them with the set values, and adjusts the output of heating or cooling devices in real-time through control algorithms to achieve the preset control goals.
### 2.3.2 Robotic Control System Applications
The application of robotic control systems is a field of high dynamic complexity, where uncertainty and external disturbances often occur. Adaptive control technology can significantly improve the flexibility and performance of robots. In practical applications, robots may operate in varying environments, for example, during manufacturing, assembly, packaging, and other operations, where robots' tasks may need to face different work objects and environments, which increases the difficulty of control.
Adaptive controllers can dynamically adjust control parameters according to the actual performance of the robot to adapt to load changes, path deviations, or external disturbances. For example, in assembly operations, robot controllers can identify changes in contact forces and adjust their movements accordingly to improve the accuracy and efficiency of operations. With the help of adaptive control, robots can automatically optimize their control strategies to adapt to different working conditions.
In t
0
0
相关推荐
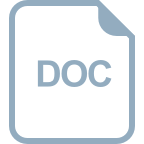
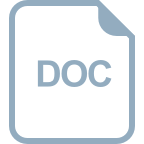
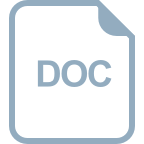
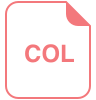
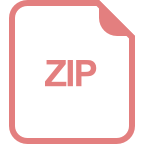
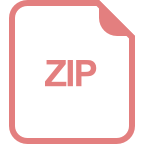
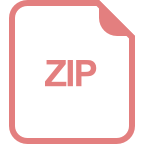
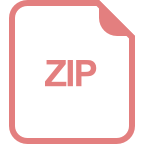
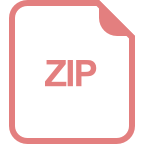