[Advanced] Boost Converter - Simulink Simulation Model
发布时间: 2024-09-14 04:44:19 阅读量: 53 订阅数: 45 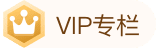
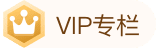
# 1. Fundamental Theory of Forward Converter
The forward converter is a non-isolated buck-boost converter that operates in both buck and boost modes. The basic principle involves storing energy in an inductor and controlling the energy conversion by the conduction and interruption of switching devices.
The primary operating principle of the forward converter is as follows:
- **Conduction Period:** The switching device is turned on, causing the input voltage to be directly applied to the inductor, resulting in a linear increase in inductor current.
- **Discontinuation Period:** The switching device is turned off, allowing the inductor current to flow in reverse through a diode into the output, resulting in a linear decrease in inductor current.
By controlling the on and off times of the switching device, the output voltage and current can be adjusted. The relationship between the output voltage and input voltage of the forward converter is:
```
Vo = Vin * (D / (1 - D))
```
Where Vo is the output voltage, Vin is the input voltage, and D is the duty cycle of the switching device.
# 2. Setting Up the Simulink Simulation Environment
### 2.1 Basic Structure of Simulink Simulation Model
The Simulink simulation model is a graphical interface composed of various components. These components represent different elements in the system, such as power sources, switches, inductors, ***ponents are connected by signal lines, indicating the flow of signals through the system.
The basic structure of a Simulink simulation model includes the following elements:
- **Source Block:** Represents the power source or signal source in the system.
- **Processing Block:** Performs mathematical operations or logical operations.
- **Sink Block:** Receives signals from other blocks and either stores or displays them.
- **Connection Lines:** Connect blocks and represent signal flow.
- **Parameter Settings:** Each block has its own parameter settings for configuring its behavior.
### 2.2 Component Selection and Parameter Settings for the Simulation Model
When constructing a Simulink simulation model, it is essential to carefully select components and set their parameters. The choice of components depends on the system to be simulated, while parameter settings affect the accuracy and efficiency of the model.
**Component Selection:**
- **Power Source Block:** Choose a power source block that matches the type of power source used in the system.
- **Switching Block:** Choose a switching block that matches the type of switches used in the system.
- **Inductor and Capacitor Blocks:** Choose inductor and capacitor blocks with appropriate values and characteristics.
**Parameter Settings:**
- **Power Source Block:** Set parameters such as voltage, current, and frequency for the power source.
- **Switching Block:** Set parameters such as on-time, off-time, and duty cycle for the switches.
- **Inductor and Capacitor Blocks:** Set parameters such as inductance and capacitance values for inductors and capacitors.
**Code Block:**
```
% Forward Converter Simulink Simulation Model
% Power Source Parameters
V_in = 12; % Input Voltage (V)
f_sw = 100e3; % Switching Frequency (Hz)
% Switching Parameters
D = 0.5; % Duty Cycle
% Inductor and Capacitor Parameters
L = 1e-3; % Inductance Value (H)
C = 10e-6; % Capacitance Value (F)
% Building Simulink Model
simulink_model = simulink.Model('Forward Converter');
% Adding Power Source
V_in_block = simulink.BlockDiagram.Source('Voltage');
V_in_block.Parameters.Voltage = V_in;
add_block(V_in_block, simulink_model, 'Position', [100, 100]);
% Adding Switching Device
sw_block = simulink.BlockDiagram.Switch('Switch');
sw_block.Parameters.DutyCycle = D;
add_block(sw_block, simulink_model, 'Position', [200, 100]);
% Adding Inductor
L_block = simulink.BlockDiagram.Inductor('Inductor');
L_block.Parameters.Inductance = L;
add_block(L_block, simulink_model, 'Position', [300, 100]);
% Adding Capacitor
C_block = simulink.BlockDiagram.Capacitor('Capacitor');
C_block.Parameters.Capacitance = C;
add_block(C_block, simulink_model, 'Position', [400, 100]);
% Adding Output
V_out_block = simulink.BlockDiagram.Sink('Voltage');
add_block(V_out_block, simulink_model, 'Position', [500, 100]);
% C
```
0
0
相关推荐




