[Practical Exercise] Intelligent Simulink Vehicle Suspension System Simulation
发布时间: 2024-09-14 04:45:22 阅读量: 30 订阅数: 47 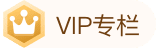
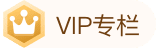
# 1. Introduction to Simulink and Basics of Automotive Suspension Systems
Simulink is a graphical modeling and simulation tool developed by MathWorks, built on top of MATLAB. It is widely used in various fields including control systems, signal processing, and power electronics. Known for its intuitive graphical interface and powerful simulation capabilities, it enables engineers to build and simulate complex systems quickly and efficiently.
The automotive suspension system is a mechanical device that connects the vehicle body to the wheels. Its primary function is to absorb road impacts, ensuring the stability and comfort of the vehicle during operation. Suspension systems are primarily composed of components such as springs, shock absorbers, and linkages, with different types of suspension systems possessing distinct performance characteristics.
# 2. Simulink Modeling and Automotive Suspension System Simulation
### 2.1 Basics of Simulink Modeling
#### 2.1.1 Simulink Work Principle
Simulink is a simulation software based on a graphical user interface (GUI) that allows users to create dynamic system models by dragging and dropping blocks. These blocks represent different components in the system, such as signal sources, integrators, transfer functions, etc. Simulink uses time-domain simulation algorithms to solve the model and generate the system's output signals.
#### 2.1.2 Components of a Simulink Model
A Simulink model consists of the following primary components:
- **Subsystems:** Decompose complex models into smaller, manageable parts.
- **Blocks:** Represent predefined components that perform specific functions in the system.
- **Signal Lines:** Connect blocks and represent the flow of signals.
- **Simulation Parameters:** Control simulation settings, such as simulation step size and duration.
### 2.2 Modeling of Automotive Suspension Systems
#### 2.2.1 Principles of Suspension Systems
The automotive suspension system is a mechanical system designed to isolate vibrations between the vehicle body and wheels, thereby enhancing driving comfort and operational stability. Suspension systems are typically composed of springs, shock absorbers, and linkages.
#### 2.2.2 Building a Simulink Suspension System Model
A Simulink suspension system model can be divided into the following parts:
- **Vehicle Body:** Represented by a rigid body block, its mass and moment of inertia represent the body of the vehicle.
- **Suspension:** Comprised of springs and shock absorbers, represented by transfer functions or state-space models.
- **Tires:** Represented by a linear spring, with stiffness representing the tire's rigidity.
- **Road Surface:** Represented by a sine or random signal, with amplitude and frequency representing road unevenness.
**Code Block:**
```
% Suspension System Model
car_mass = 1000; % Vehicle body mass (kg)
car_inertia = 1000; % Vehicle body moment of inertia (kg*m^2)
suspension_stiffness = 10000; % Suspension stiffness (N/m)
suspension_damping = 100; % Suspension damping (N*s/m)
tire_stiffness = 100000; % Tire stiffness (N/m)
% Road Surface Model
road_amplitude = 0.1; % Road unevenness amplitude (m)
road_frequency = 1; % Road unevenness frequency (Hz)
% Creating the Simulink Model
simulink_model = new_system('car_suspension');
% Creating Subsystems
car_body = add_block('simulink/Sources/Constant', si
```
0
0
相关推荐





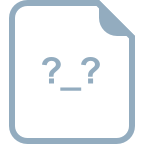


